(Editors Note: The following report was filed from the Paris Expo, site of the 13th
International Exhibition of Textile Machinery ITMA 99 which opened its 10-day run on June 1. This
report is a first look at some of the innovative technologies exhibited in Paris. For complete
technical details on ITMA exhibits, look for articles in the August and September issues of ATI,
following the annual July Buyers Guide issue. This report was compiled by ATI Executive Editor
Alfred Dockery; Technical Editor Eric Vonwiller; Technical Editor Dr. Mansour Mohamed and Editorial
Director Monte G. Plott.)
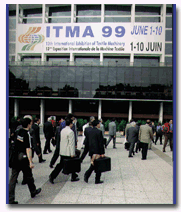
PARIS, France How eager were leaders of the global textile industry to see their futures at
ITMA 99More than eager; in fact, downright aggressive. Consider: Not even a strike that shut down
the Paris subway system on the second day of the show could keep crowds away. There were reports of
four-hour waits for taxis, and two-hour walks through the unseasonably hot streets of Paris to get
to and from ITMA, still visitors came by the hundreds. The show drew a whos who of American textile
leaders early on. Spotted walking the aisles during the early days were Roger Chastain (Mount
Vernon Mills), Duke Kimbrell and Andy Warlick (Parkdale Mills) and Ed Schrum (Carolina Mills).
There were reports that in the days leading up to the show, Roger Milliken had dramatically
increased the delegation from MillikenandCo., to better assess the technology on display. With some
1,250 exhibitors on display and 150,000 visitors from 130 countries expected during the 10 days of
ITMA, people got busy early. Weve been busy since the show opened at nine this morning, Allen
Thompson, Staubli technical and sales representative, said on opening day. We had Americans waiting
to get in when the doors opened.Robert Antoshak, vice president of Werner InfoTex Division said:
Were doing four on-line presentations a day, and were booked solid through the show. Werner is an
internet website and database provider that was exhibiting at ITMA for the first time.Computer
software was one of the hot topics at ITMA 99, with CAD, CAM and computer-aided production control
systems prevalent at stands throughout the massive 160,000-square-meter exhibition space. It was
commonplace to see visitors spending as much time examining computer systems attached to machines
as they did do the machines themselves.Another area of technology drawing attention was
environmental products. Reflecting increased emphasis on environmental matters, ITMA 99 organizers
added a new special category for exhibitors of environmental products such as equipment for liquid,
solid and air recycling.For visitors at the show, the search was not just for new technology or
improvements in existing manufacturing systems. It was for a competitive edge in the global
marketplace. The systems and machines that caught the eyes of key American manufacturers were as
readily available to their competitors around the world as they were to their competitors down the
road.ITMA 99 provided a window on the future of the industry not just for the next four years but
for the next century. Here are some first impressions of what could be seen through that
window: Dyeing, PrintingandFinishing
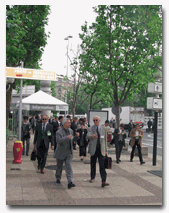
Gaston County Dyeing Machine Co., USA, had several new developments to show including its new
Millennium dyeing system. Key features of the system include a central control center, automated
weighing and dye dissolving, automatic chemical dispensing, central charge tank, automatic pH
control and conductivity monitoring, and high performance dyeing machines.The Millennium Piece
Dyeing Machine also made its debut at ITMA 99. This new jet-dyeing machine has a nominal capacity
of 450 pounds (205 kilograms) per tube and a 5:1 liquor to cloth ratio.Finally Gaston County
introduced new automated dye preparation systems. AccuWeigh provides accurate weighings of dyes in
a cost effective and timely manner. AccuMix delivers accurately dissolved dyes according to
dyestuff manufacturer recommendations for mix time and temperature.Datacolor International,
Switzerland, focused on getting the Right Color from Mind to Market at ITMA 99. The company
introduced its new Colorite color communication products for the first time to the worldwide
textile industry.The Colorite line of products provide precise color communication based on what
the company calls the most accurate computer screen calibration to date. Using a sophisticated CRT
Colorimeter and a highly developed conversion process the RGB signals of any good quality monitor
can be converted to CIE coordinates, allowing accurate screen representation within Delta 0.5
CIE.Colorite uses a process called Digital Sampling to let users communicate colors digitally
through e-mail or by network. The colors can be visually assessed immediately on screen without the
cost and time involved in shipping physical lab samples.The company also exhibited a new printer
calibration product that provides the dye house or color specifier with more accurate hard copy
prints that match the screen image.Scholl AG, Switzerland, presented the new piece dyeing machine
Rapidstar Century, that provides fast process cycles for a large variety of knitted and woven
fabrics. New is the patented Rapidflex option, a unique new chamber adjustment mechanism for
creating a highly versatile piece dyeing machine. It accommodates varying load sizes, fabric
weights and fabric styles.With a liquor ratio of 1:3 for synthetics, and 1:4,5 for cotton fabrics
the machine has a low consumption of steam, water, energy, salt and chemicals.Another new
piece-dying machine is the Scholl Intensity for densely knitted and tightly woven fabrics that are
prone to rope marks. The Intensity is equipped with a special fabric transport system that assures
intense contact between the dye liquor and the fabric rope.Scholl introduced its new Hot Water
Module systems that can boost productivity in a plant up to 25 percent by reducing fill times and
cycle times with re-heated water.Stork Digital Imaging B.V., Netherlands, presented its new true
digital printer, Amethyst that can print on demand and produce more than 350 square meters of high
quality prints per day. With Amethyst, all textile key requirements, such as light and wash
fastness are guaranteed. Stork says it is unrivaled in print quality and can print unique design
sizes of up to 5 meter length.This printer needs no engraving of screens, nor any paste
preparation. It was designed for the ever shorter becoming production runs, and the requirements of
being able to satisfy customer orders instantly, in just one or two days. Biancalani SpA,
Italy, demonstrated its new Airo Quattro machine for fabric washing and drying. The Quattro is a
further refinement of the companys Airo machine. According to the company, there are 550 Airo
machines installed worldwide.
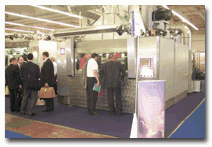
Biancalani showed its new Airo Quatro machine for fabric washing and drying in rope form. The
machine features improved versatility and increased capacity. It can now handle knit fabrics as
well as wovens. The Airo Quattros major improvements include increased capacity and more
flexibility. The unit handles fabric in a tensionless manner and can be used to process knit goods.
Up to four different fabrics can be processed simultaneously. Cycle times can be as short as 40
minutes. Of course, this varies with fabric type.Biancalani also exhibited the Idra modular
milling-washing machine with independent channels. Its major features include newly designed
milling units, process automation and an air-jet device. WeavingBenninger Co. Ltd.,
Switzerland, announced a strategic alliance with the Moenus Group to be effective as of June 1,
1999. The announcement declared that the two companies will work together to open up positive
prospects over the long term. The marketing and service network will be extended and strengthened
worldwide and will facilitate closer customer contacts.Benninger showed a wide range of warping and
sizing machines. Also shown a number of creel configurations for sectional and direct
warping.
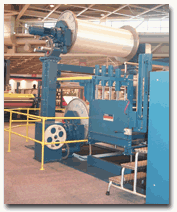
Benninger showed several innovations for weaving preparation and finishing. Pictured is an
independent motor drive on a Benninger assembly beamer.The BEN-V-CREEL for direct beaming with low
thread tension. Assembly beaming with perfectly regulated tension control offering more flexibility
through width adjustment. New for ITMA is reliable process monitoring via an abrasion-proof
infrared touch screen.Also new at ITMA, although has been in use the beginning of the last year is
a new generation of sectional warpers. An example is the BEN-trONIC for universal application. A
PLC receives the signals from the measuring roller and controls the thread tensioners via motorized
drive. Benninger also exhibited several section and direct warping creels. BEN-CREEL provides
a modular system which makes customized solutions for warp preparations possible. One of the new
developments for this ITMA is the precise tangential unwinding, leading to uniform tension.Another
development which is a first for ITMA, but has been available for about a year is the cold sizing.
Two-sided cold sizing application by splashing has long been a familiar alternative to waxing. What
is new is the use of cold size with high adhesive power. The size application is followed by
cylinder drying. The Teflon-coated cylinders are steam-heated and operate at temperatures below 100
C. Lindauer Dornier GmbH, Germany, showed several of their rapier and air-jet weaving machines
with many new refinements. Examples of the new additions include: Permanent control on timing of
all nozzles. If a valve malfunctions one time, a message is relayed to the main control panel to
indicate which valve needs adjustment. Mobile Tandom Booster Nozzles (TMD) for up to eight colors,
all of which are moving with the lay.
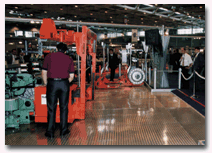
Dornier demonstrated an impressive quick style change from a fine worsted to a pure cashmere
fabric. The high speed Type HTVS/S18 rapier machine was running at 500-520 picks per minute.
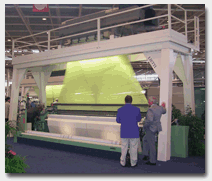
Dornier showed a 430-centimeter air-jet machine driven by a jacquard head. This is the widest
air-jet machine ever shown, according to the company. Air-operated tucking motion with fully
electronic control for flat, terry, and tire cord fabrics. The operating speed is up to 1,000 picks
per minute. Disc leno operated by a motor which is integrated with the disc. This available for
both air-jet and rapier machines. Triple filling sensor with stretch nozzle to sense the arrival of
the pick, as well as detecting broken picks.
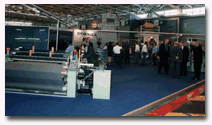
The range of yarns used for filling on air-jet machines has been extended; for filament yarns
from 20 to 2,000 deniers and for spun yarns from Ne 5 to Ne 71. Improved start marks prevention. A
1,500 mm diameter warp beam placed above the machine.The most noted improvement in the rapier
machine is the increased speed to 550 picks per minute for 190 centimeters width. One of the
machines was shown with a Staubli Jacquard head having 10,000 hooks. This machine is capable of
changing the fabric design while it is running. As an indication to the wide range of yarns which
can be woven on the Dornier rapier machines, one was shown weaving screen glass fabric. Nuovo
Vamatex SpA, Italy, had many improvements at this ITMA including its FTS (Free Transfer System).
This means there are no guide teeth in the shed to control the tapes. This was shown on two
Leonardo machines, one weaving tie fabric and the other weaving industrial fabric. This FTS is
available only on loom widths of up to 230 centimeters.The company also showed its Motorized leno
device, a leno system driven with a stepping motor directly controlled by the microprocessor. The
alternating movement of the leno is activated by a patented Vamatex mechanism. This device offers
the advantage of setting the crossing time directly from the microprocessor.The speed range for the
Vamatex machines was over 600 picks per minute for the 190 centimeters width and 400 picks per
minute for the 360 centimeters version.Picanol NV, Belgium, showed its Gamma Rapier machine for the
first time at ITMA. The most important features of this machine can be summarized as follows: Free
flight system, no guide teeth for the rapiers reducing warp damage for filament yarns, known as
Omni-FF. SUMO, super motor which is capable of changing machine speed in one cycle during running
over a wide range. This makes the drive maintenance free, since there are no belts or clutch.
Filling tension sensor which displays the filling tension during the weaving cycle. Double pick
insertion with the possibility of inserting more than two picks based on the yarn size. PFL, pick
tension release which provides optimum filling tension during insertion. This is electronically
controlled. New scissors positioning, close to the fabric edge thus reducing the amount of
waste.The maximum speed for this machine is 600 picks per minute.The Picanol Omni air-jet machines
displayed the on-loom fabric inspection in collaboration with EVS, Elbit Vision System. This system
can stop the machine when a major defect is made, and is capable of feeding the information to a
central computer. Another new feature for the Omni machine is the use of double insertion system by
means of one or two nozzles. A super-wide Omni, 380 centimeters width was shown weaving percale
sheeting fabric.
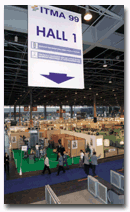
Somet, Italy, featured several rapier and air-jet machines. The company showed two different
rapier machines, Thema Super Excel and Super Excel HTP. Super Excel HTP is for high textile
performance rather than high speed. The Thema machine maximum width is 360 centimeters are inserted
simultaneously increasing the rate of filling insertion to 2841 meters per minute. Another Super
Excel machine was weaving heavy weight fabric from three beams behind each other. New additions are
also electronic weft selector and a fully electronic leno device.The Clipper air-jet machine was
shown weaving 14.5 ounce per square yard denim at a speed of 1,000 picks per minute.Another
development is the Somet Telesystem Service (STS) which allows machines in Italy to be connected to
a Somet facility through the internet. This system uses bidirectional communications to check the
operations of the machines and reprogram them. Examples of parameters which are controlled are warp
tension, machine timing, picks per inch and speed. Staubli, Switzerland, showed all three
types of shedding systems with major new developments for each: cam, dobby and Jacquard.The company
showed a new positive cam motion series 1700 for weaving heavy fabrics at high speed. There were
two types: the 1751 with no shed leveling device and 1761 with shed leveling device.There was also
a new positive dobby for high speed in two types: 2861 for 16, 20, 24 and 28 harness frames, and
2871 for 16 harness frames. Both heads can be mounted low or on a super structure, the e22 for low
and e62 for high mounting.Staubli showed electronic Jacquard heads from 72 to 12,288 hooks. A new
CX 160 machine with 96 hooks was shown. Also new is LX60 with 896 hooks and the LX 1600, double
lift with cam drive and coaxial shaft for 3072, 4096, 5120 and 6144 hooks.
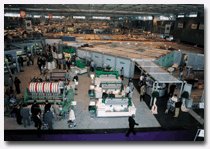
The LX 1690 and LX 3290 were shown for weaving all types of velvet. This machine can mix for
two or three positions. What is new is module two position. The shed can be adjusted to separate
the shed for the ground from the shed for the pile. This machine saves the weavers from having to
couple two machines together.Another new machine is the LX 2490 for carpet weaving. The same
principle of the previous two machines is used here with the exception of larger shed opening. This
head can have 3042, 6720 and 8064 hooks. Sulzer Textil Ltd., Switzerland, showed a multitude
of innovations. The G 6300 rapier machine was introduced. This is the first product after the
merger with Pignone and combines some of the features from the two rapier machines, G6200 and FAST.
The machine has a new drive system which is suited for high speed with industrial speed of up to
700 picks per minute. A 32 bit microprocessor controls the machine. It can be used without guides
or when necessary support guide teeth can be used. The G 6250 rapier represents a further
development of the proven G 6200 concepts with a 10 percent increase in speed. Refinements were
made in the filling yarn path to reduce friction. It features new electronics with touch screen
terminal. Completely new programming features for filling feeders and filling sensors as well as a
new electronic color selector, with 8 colors for dobby and 12 colors for Jacquard machines round
out its capabilities.
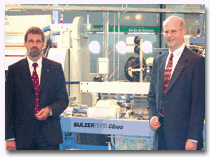
Sulzer Textil’s Philip Mosimann (l), president and CEO, and Christopher Somm, worldwide sales
and marketing manager, presented the company’s new G6300 high speed rapier machine.
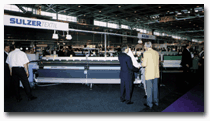
The P 7150 projectile machine represents a speed improvement of approximately eight percent
due to a newly designed picking unit. A new electric terminal is used to control filling breaks,
projectile identification and any textile related basic information. The machine has a pre-heating
unit to heat the oil which lubricates the projectiles and other machine parts.The P7MR3
(S360-N4-SP-D12) is a heavy duty projectile weaving machine with increased warp tension capability.
The machine shown on display had a total warp tension of 6.5 tons weaving a filter fabric with only
a 6.5 kw drive motor.The P7250 projectile machine was shown weaving a curtain style with four
different filling yarns. The machine has a special constant tension cloth take-up system and a
redesigned 4-color unit.The P7300 projectile machine was demonstrated to show the speed potential.
The machine width was 390 centimeters, weaving at a speed of 360 picks per minute. This machine has
a new electronic and redesigned drive system with touch screen terminal.The L5300 air-jet ma-chine
featured several improvements including a terry version; a 390 centimeters width; air saving
features; new shedding motions from Staubli and Toyoda; and a redesigned drive system for high
speed weaving.The T4300, the air-jet version of terry weaving was shown using a swing reed, and had
up to six colors. It had a speed of 540 picks per minute for a reed width of 250 centimeters.There
were two M8300 multi-phase machines shown. The first was weaving print cloth with show speed of
3230 rpm(equivalent to 6,088 meters per minute rate of filling insertion). The second was shown
weaving a 2/1 twill at a speed of 2,430 rpm (equivalent to 4,180 meters per minute. Both machines
were 190 centimeters wide. Tsudakoma, Japan, showed air-jet and water-jet machines. Highlights
of new developments for air-jet machines include the following: Needleless tuckers (air operated)
which eliminates all the mechanical parts; Electronically activated filling cutter on the insertion
side; eight colors with eight feeders;
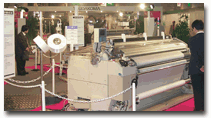
Tsudakoma showed its complete line of high-speed air-jet and water-jet looms. Pictured is the
ZW405 water-jet machine. relay nozzles with a tapered hole; improved APR (automatic pick
removal) system; and a maximum width is 390 centimeters weaving from one or two beams.The fastest
machine exhibited was 1,800 picks per minute for 190 centimeters weaving pongee fabric. West
Point Foundry And Machine Co., USA, introduced and displayed more new products in Paris than at any
show in company history. Products for pre-wet sizing, filament sizing and large diameter beam
winding capabilities were emphasized. The company showed its new Model 863-PW Size Box with
accompanying Size Concentration Control System for precise pre-wet sizing. The unique concentration
control system is applicable to both pre-wet and non-pre-wet.The company also introduced its new
Model 998 Filament Size Box. Features of the box included a new loading system for a larger
immersion roll, independent adjustment, load-cell monitoring on each end of the loaded rolls,
Teflon-coated vat, and both PLI and PSI loading display. The Model 950-A Beam Winder with its
delivery roll section and beam winding can wind up to 63-inch (1600 mm) diameter loom beams while
having convenient waist-high access to the comb. Spinning
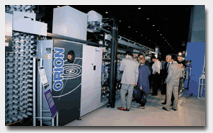
Savio Macchine Tessile SpA./Radici Group, Italy, introduced the brand new automatic winder
called Orion. The machine features a sophisticated C.A.P. system (computer aided package) that is
revolutionary in its design and function when compared to conventional electronic on-off
modulation. It allows the user to produce a perfect package without any patterns and avoids
acceleration and deceleration of the winding drum. The Orions principle function is based on a
constant drum speed and makes use of minute servo commands to shift the axle angle of the
individual packages.
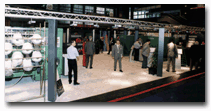
Spindelfabrik Suessen, Germany, presented its new concept rotor spinning machine TT-1 with
spinbox SC. Suessen showed with this machine innovative ideas for the automation of modern
high-speed open-end spinning machines.The TT-1 features improved yarn quality and extended range of
applications of rotor-yarns, reduced maintenance due to significant changes in design, and reduced
power consumption. Suessen feels that the TT-1 will set the trend for future rotor-spinning machine
generations.
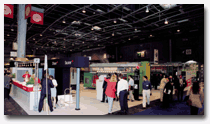
W. Schlafhorst AGandCo., Germany, promoted the evolution model of the new automatic package
winder Autoconer 338. New state-of-the-art sensor technology, drive and information technology
provide the perfect package, according to the company. The Autoconer 338 is offered in the model
types RM, D; the type V is the linkage to the Air-Com-Tex 7000 condenser ring spinning machine from
Zinser. Type K offers automatic feed package change and several special performance features.
Schlafhorsts Autocoro 288 was shown with the new Corobox SE 11, which is the first spinbox to be
manufactured in-house. Schlafhorst claims rotor speeds of up to 150,000 rpm and a maximum delivery
speed of 220 m/min. Schalfhorst also offered upgrades of existing Autocoro machines with SE 8 and
SE 9 spinbox. The company showed its new Belcoro yarn philosophy for high-fashion textiles, and the
foreign fiber detection with Corolab ABS. Murata Machinery Ltd., Japan, showed its No. 851 MVS
Vortex air-jet spinning machine for 100-percent cotton. The machine is capable of delivery speeds
of up to 400 meters per minute. This machine was introduced at OTEMAS 97. This is its first
exhibition outside Japan. It features a fully automatic piecing system that removes and repairs
yarn defects.
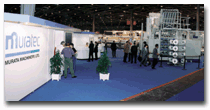
In winding, Murata will show the No. 7V-II Mach Coner Bobbin Tray Type and the No. 7-V Mach
Coner Cone to Cone Type. The No. 7V-II Mach Coner is a fully automatic winder with individual
inverter control. The machines tension manger controls winding tension, and its Bal-Con device
controls yarn ballooning. The No. 7-V Mach Coner is a fully automatic cone-to-cone winder. It has a
new type air-waxing unit and a new high-speed automatic doffer.

Murata’s Mach Coner gets a respectable share of attention from textile executives.On the
man-made yarn side, the company will show its No. 33H Mach Crimper and No. 33J-II Mach Crimper draw
texturing machines; the No. 778 High Speed Take-Up Winder, the No. 748 High Speed Take-Up Winder,
and the No. 459 Spandex Winder; and the No. 37S air-jet crimper air-jet texturing machine.
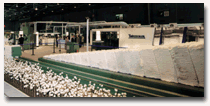
Trutzschler GmbH, Germany, showed for the first time the new high-production card DK 903
which replaces the model DK 803. The 903 incorporates the brand new technology of a motor driven
precision flat setting system (PFS) which allows extraordinary accurate adjustments of the flats
distance to the cylinder within just a few seconds.Flat speed is also electronically variable.
Other new developments in the preparation field are the 800 kg/hr (~1750 lbs/hr) Cleanomat CXL
cleaner, and the foreign fiber separator Securomat SC and SCFO. Trutzschler showed further two of
its HSR1000 draw-frames, of which one was equipped with an automatic can changer for rectangular
cans, as well as the automatic can transport system from Hubtex, Germany.At a separate booth, the
company presented its new range of nonwoven machinery that is extremely versatile and offers high
production rates to the mill.For the first time Trutzschler offers a complete product range for
long-staple fiber processing, from bale work-off through the tuft feeder. The 5-meter wide Scanfeed
FBK can be used for production rates of up to 2000 kg/hr (~4,400 lbs/hr) and features precise
evenness control over the entire production length and width. Rieter Textile Systems,
Switzerland, had one of the busiest stands in Hall 1. The company exhibited its equipment under the
motto: Customers Implement Their Objectives Together With Rieter.The company showed the C 51 card,
the successor to the very successful C 50 card. The C 51 has Trexplus, a further development of the
Trex system used on the C 50.This system sharply reduces the trash content of the sliver without
additional loss of good fiber, according to the company.Rieter celebrated the completion of its
1,000th RSB-D 10/D 30 generation of autoleveling drawframe in January, barely a year after starting
full-scale production. The RSB-D 30 was shown at ITMA. Its major advantages are enhanced efficiency
due to user friendliness and very high speed due to precise sliver guidance and new levelling
technology.Approximately 350 of the companys G33 ring-spinning machines have been sold since its
launch about a year ago. Its features include Servogrip doffing without underwindings; Flexidraft
yarn count changes at the push of a button; Ri-Q-Bridge improved yarn quality due to optimum fiber
guidance; and Intercool integrated liquid cooling system for motors and frequency inverters.The
company also showed its new BT 905/903 rotor spinning machines. The BT 905 is automated, and the BT
903 is semi-automatic. Both are designed for markets where labor costs are low and capital costs
are high. Quality ControlZellweger Uster, Switzerland, had a remarkable number of new
developments to show at ITMA 99. These included the Uster Quantum Clearer, the Uster HVI Spectrum
tester and the Uster Fabriscan automatic fabric inspection system.
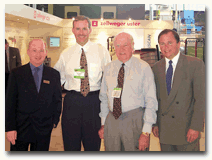
Everything shown at the Zellweger Uster stand was new. Pictured from left to right are:
Rudolph Kagi, president and CEO, Zellweger Uster; Andy Warlick, Parkdale Mills; Duke Kimbrell,
Parkdale Mills; and Harold Hoke, senior vice president, marketing, sales and service, Zellweger
Uster.
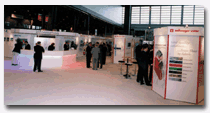
The Uster Quantum Clearer appeared to gather the lions share of attention here. This clearer
is user configurable. It can be used in several different modes including: capacitive or optical
sensing, capacitive and foreign matter sensing or capacitive and optical combined. Its features
include 100-percent digital electronics, self-calibrating measuring heads and on-board diagnostics.
It is retrofittable to many existing machines.The Uster Quantum Clearers product highlights include
computer aided yarn clearing; Foreignclass, a new standard in foreign matter classification and
classification and optimization in the same graph, on screen.We came with no expectations but have
had an incredible first day, perhaps a record day for Zellweger Uster, said Les Ivie, executive
vice president, chief development officer, Zellweger Uster. There has been a tremendous interest in
the Quantum Clearer.The Uster HVI Spectrum tester features reduced need for sample and lab
conditioning, automatic calibration check, maturity index and short fiber index. Some of the new
technology here came from Usters work on its Intelligin process control system for cotton gins.The
Uster Fabriscan automatic fabric inspection system offers 0.3 millimeters resolution at up to 120
meters per minute. It has a learning system for quick and efficient style changes and consistent
fault classification of fabric and yarn faults. Uster Fabriclass and fabric statistics are also
offered. NonwovensFleissner GmbHandCo., Germany, introduced the Fleissner AquaTex Spunlace
System for woven fabrics, which it says is a revolutionary new textile process for pretreatment and
finishing of woven fabrics. AquaTex makes fabrics look, feel and perform better, according to the
company.The InterSpun process with the AquaTex system is the impingement of a fabric supported on a
solid or pervious surface, with very fine high velocity and discreet water jets in the form of a
curtain. The energy imparted causes the cloth to bulk and blossom and individual fibers to be
entangled. This entanglement takes place at crossover points between the warp and the weft, within
the yarns themselves and in the interstices between yarns. The amount of entangling and bonding is
directly related to the energy imparted to the cloth and to the nature of the fabric itself. The
process itself is much more than a fi