Nature does an excellent job of protecting living plants from invasion by harmful external agents
that could interfere with a plants healthy growth.In the case of cotton fiber, the shield that
nature uses for protection consists of the cuticle and primary cell wall, which remain with the
fiber after growth has stopped and the fiber has been removed from the seed.The cuticle/primary
cell wall membrane is located in the outermost zone of the cotton fiber and consists of a thin
matrix of waxes, pectins, proteins, and other substances.This matrix renders the cotton fiber quite
resistant to water absorption in the absence of wetting agents, and can cause subsequent
wet-processing problems for the textile manufacturer.No matter if the textile material is in the
form of a cotton fiber, yarn, knitted or woven fabric, it is essential that the substrate be
subjected to one or more chemical processes that can remove or modify the cuticle to make the
cotton fiber water absorbent.It is imperative that the substrate be adequately prepared if the
textile material is to be given a wet-processing treatment such as bleaching, dyeing, printing, or
finishing.Lack of adequate and consistent preparation continues to be a source of quality problems
for the textile manufacturer, and improvements in this area continue to be eagerly sought.
Conventional PreparationOne of the earliest techniques for preparation of cotton fabric
involved the use of potash, the by-product of wood combustion.A major component of wood ash is
potassium oxide, and when wood ash is added to water, the potassium oxide reacts to produce
potassium hydroxide, a strong alkali.Early textile chemists prepared their fabric for subsequent
processing by treating the fabric in hot slurries of potash, followed by neutralization of the
treated fabric in solutions of buttermilk.Although it can be argued that the chemicals used by
ancient textile chemists were of natural origin, the release of these natural substances did not
have a positive impact on the environment.Today, alkaline scouring of cotton is still the most
widespread commercial technique for removing or interrupting the fiber cuticle to make the fiber
absorbent for processing. However, the modern textile chemist uses sodium hydroxide in place of
potash, and acetic acid in place of buttermilk, but the release of these modern chemicals into the
effluent still does not have a positive environmental impact.In addition to the alkali used in
preparation and the acid used in neutralization, other chemicals also are included in typical
preparation baths.These chemicals include: wetting agents that reduce the surface tension of water
so that the preparation chemicals more easily can penetrate the cotton fiber; emulsifying agents
that assist in removing waxy materials; chelating agents that remove polyvalent metal ions such as
calcium, magnesium, iron or other salts that can have a harmful effect on subsequent wet-processing
operations; and polymeric materials that also can act as chelating agents or as pickup enhancing
agents for use in continuous preparation processes.These various chemicals tend to be used in
excessively high amounts, and this fact is another source of needless environmental
contamination. EnzymesIt has been known for a very long time that enzymes can be used as
positive environment alternatives to harsh chemicals in textile wet-processing. Enzymes are nothing
more than biological catalysts, consisting of complex, three-dimensional proteins that are composed
of polypeptide chains, and usually have either a fungal or a bacterial source. These proteins only
accelerate reactions: enzymes cannot cause a reaction to occur that ordinarily would not occur;
however, in the absence of enzymes an extremely long time may be required for some reactions to
occur. A primary textile use of enzymes is in the promotion of hydrolysis of specific substrates, a
process for converting water-insoluble material to products that dissolve in water and can be
washed away.Until recently, enzymatic hydrolysis has found widespread textile use in only three
areas: desizing, stone washing, and bio-polishing. DesizingThe enzymatic removal of the warp
size, starch, from fabric by use of the enzyme, amylase, is a very old process that first was begun
about 1850. Although starch can be removed from fabric by use of acid hydrolysis, such a process
can have a detrimental influence on the strength of the cotton fabric if the process is not
carefully controlled. Also, acids have a much more negative environmental impact than does
amylase.Enzymatic hydrolysis of starch has long been accepted as being by far the preferred process
from a standpoint of ease of control and environmental stewardship. Stone WashingThe popular
washed-down or worn look that is so prevalent in denim jeans initially was obtained by the use of
pumice stones that were soaked in sodium hypochlorite or potassium permanganate oxidizing agents.
When jeans were tumbled with these bleach-soaked stones, dye was destroyed where the stones rubbed
against the fabric.Since the decomposition of dye occurred in a random manner, a distinctive look
was obtained. Needless to say, the chemicals used in the process were by no means environmentally
benign.During the 1980s it was discovered that the same look could be obtained by the use of
cellulase enzyme. When denim jeans were tumbled with solutions of cellulase enzyme under the proper
conditions of temperature and pH, the surface of the dyed fiber was hydrolyzed, releasing dye in a
random manner to produce the desired effect. Enzymatic washing of jeans gradually has replaced the
use of environmentally harsh chemicals in the stone washing process on an international
level. Bio-PolishingCellulase is highly effective in removing loose fibers from fabric
surfaces. The term, bio-polishing, has been coined to describe the process. Bio-polishing has
benefit both in producing a smooth fabric surface and in helping a dyed fabric retain its color
depth during laundering. In the later process, cellulase enzyme is included in the detergent
formulation to hydrolyze any fibers brought to the fabric surface by abrasion during laundering. By
eliminating surface fiber, the light scattering phenomenon that reduces color depth is avoided.
Bio-PreparationAs a result of the international research efforts directed to treatment of
cotton fabric with cellulase enzyme, it was discovered that cellulase ostensibly had the ability to
make the cotton absorbent.In fact, fabric treated with cellulase was more absorbent, but the
cellulase enzymes used in various investigations were not pure. Now it is known that it is the
pectinase impurity present in cellulase that is responsible for the greatly improved water
absorbency of cotton that is found to occur when cotton is subjected to a mild cellulase
treatment.Of course when cotton is subjected to a vigorous treatment with cellulase, the cotton
becomes absorbent because so much of the cotton structure is destroyed by hydrolysis.The pectin
which is present in the cotton fiber cuticle is a powerful biological glue. This glue consists of
polygalacturonic acids that to a great extent have been converted to calcium, magnesium, iron, or
other salts during fiber growth. These pectin salts are not very soluble in water and serve to bind
the waxes and proteins together in the cuticle to form the fibers protective barrier, the primary
cell wall.Not all pectinase enzymes are equally effective in promoting hydrolysis of the pectin.
The best ones seem to be those that can function under slightly alkaline conditions even in the
presence of chelating agents. Most conventional pectinases are not active under those very
commercial conditions that promote the best interruption of the cuticle matrix to achieve superior
fabric absorbency. Alkaline PectinaseA very powerful, novel alkaline pectinase has been
isolated by scientists at Novo Nordisk. This robust pectinase functions well at moderate
temperatures under buffered, mildly alkaline conditions – even when chelating agents and selected
wetting agents are included in the preparation bath.The possible mechanism by which this new
alkaline pectinase functions is illustrated schematically in the figure.As shown in Figure 1,
pectinase has a quite specific three-dimensional structure and is adsorbed onto the
three-dimensional pectin substrate in lock-and-key fashion. At the interface between the
pectinase/pectin associated complex, hydrolysis of the pectin is very strongly accelerated.
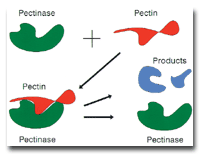
Figure 1. Simplified schematic diagram of the mechanism of enzymatic hydrolysis of pectin by
alkaline pectinase. The hydrolysis produces products that diffuse away from the primary wall
matrix, loosening the matrix structure and releasing the enzyme to become very rapidly attached to
another area of the pectin substrate.The process of hydrolysis interrupts the cuticle structure
more and more, releasing some wax and protein and results in a cotton fiber that is just as
absorbent as is one that has been prepared by environmentally harsh, conventional processes. An
unexpected, positive aspect of bio-preparation with alkaline pectinase is that the prepared cotton
fiber is much more soft than is fiber prepared by the use of sodium hydroxide. It is believed that
the reason for the improvement in softness is the retention of more of the beneficial wax by the
cotton fiber.Although wax selectively is removed by bio-preparation, the resulting fiber still has
excellent water absorbency.An ongoing investigation at The University Of Georgia with regard to the
dyeing properties of conventional versus bio-prepared cotton continues to reveal no statistically
significant differences with regard to color depth or hue and no significant differences in
fastness properties.Dye migration in exhaustion dyeing appears to be somewhat better on
bio-prepared cotton, and this fact can contribute t improved levelnes.Results of plant trials with
the new bio-preparation technique has revealed the process to be even less expensive than that of
conventional preparation processes.It is expected that within a few years bio-preparation will
become the preparation method of choice among textile chemists internationally. Opportunities
AheadOpportunities exist in the vast textile complex for significant improvements in environmental
stewardship, while lowering overall processing costs.Nowhere is this fact more evident than in the
area of wet processing, where enormous quantities of environmentally-hostile chemicals are used
daily. This massive chemical use continues to result in textile effluents that place great stress
on the environment.As the international textile complex continues to expand to keep abreast with a
rapidly expanding world population, it is critical that more attention be given to environmental
issues.Substitution of enzymes for currently used harsh chemicals can have a positive environment
impact, and explorations for new enzymatic processes that can fulfill the functions that are now
the exclusive domain of conventional wet-processing chemicals will become increasingly
important.There is no doubt the area of bio-preparation of cotton and other cellulosic fibers will
continue to be a source of much research in both industrial and academic settings.
May 1999