Wet Processing UpdateATI Special ReportpH Control In The Dyeing Of Polyamide
DyStars Optidye N program calculates optimum conditions for dye penetration and shade
stabilization.Uptake of acid and metal-complex dyes by polyamide is temperature-dependent. The
fiber takes up the dye at temperatures above the glass transition point because the segments in the
polymer chains become more mobile at higher temperatures. The fibers thus open and allow the dye,
which is attracted to the positive charge on the amino end groups in the fiber, to penetrate the
polyamide. It is then bonded to the fiber through intermolecular forces. At the end of the dyeing
process, a thermodynamic equilibrium is established between the dye dissolved in the liquor and the
dye that has diffused into the fiber. The relationship between the dye concentration in the liquor
and on the fiber is roughly described by the well-known Langmuir and Nernst isotherms.A finite time
is required to achieve this state of equilibrium. The time required depends on the substrate, the
dyes and the process parameters. This process can be described by the laws of dyestuff diffusion.
Applying these physical chemical principles in conjunction with practical experience shows the
dyeing process.Systematic OptimizationThere are two established methods of dyeing polyamide with
acid and metal-complex dyes: the constant-pH process and the pH-sliding process. While the
constant-pH process ensures that the dye exhausts onto the substrate by raising the temperature,
the pH-sliding process achieves exhaustion by a combination of raising the temperature and reducing
the pH.In the constant-pH method of dyeing polyamide (Polyamide S process), the aim is to produce
dyeings that are as level as possible from the outset and have good reproducibility.
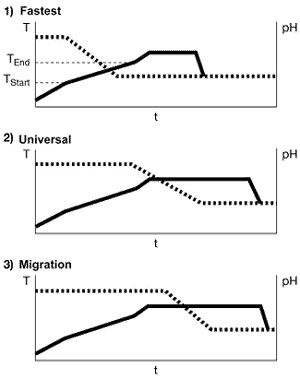
Level application of dyes, particularly at the start of the dyeing process, can be ensured if
all of the dyes exhaust onto the substrate uniformly. This is what is referred to as their
combination behavior (See right). It can be achieved in two ways. The first is to select suitable
dyes with good combinability. If this is not possible on coloristic grounds or because of the
fastness properties required, a second method can improve the combination behavior of some dyes by
using an auxiliary with affinity for the dye. The optimum concentration of such auxiliaries depends
on the type of dye, dye concentration and the auxiliaries used. The combination behavior of the
dyes may deteriorate if the amount of auxiliary exceeds the optimum level.To ensure good levelness,
the dyebath must contain enough dye to allow sufficient migration. However, if bath exhaustion is
too low, too much dye is wasted. As well as raising dyestuff costs, which are relatively low
compared with the overall process costs, this alters the final shade and thus impairs
reproducibility. A low pH increases bath exhaustion and reduces migration, while an increase in the
concentration of an auxiliary with affinity for the dye has the opposite effect. The pH therefore
needs to be optimized to ensure optimum bath exhaustion. At the same time, the strike rate (i.e.,
kinetic properties) plays a major role in regulating the dyeing process. During the heating-up
phase, the dyes exhaust onto the fiber in a given temperature range. This is known as the critical
temperature range. The beginning and end of this range are indicated by TStart and TEnd (TStart
must not be confused with the temperature at the start of the dyeing process). The optimum heating
gradient depends primarily on the unit used.To ensure good penetration of the fiber and thus
stabilize the shade and improve fastness, a diffusion phase is required after exhaustion of the
dyes. The time required for this depends on the substrate and diffusion properties of the dyes. In
practice, the diffusion period is often unnecessarily long. This raises process costs and can
damage the goods. Optimum conditions can be calculated using DyStars Optidye N computer program,
which includes both the underlying theory and the necessary dyestuff data.The Optidye N ProgramThe
Optidye N program contains the formula required for systematic optimization of polyamide dyeing
(See below). It contains data on the properties of DyStar products and a number of auxiliaries.
Users enter details of the recipe, dyeing units and substrate for each batch. The program then
calculates the optimum dyeing profile, the pH required to achieve average bath exhaustion of
approximately 95 percent and the auxiliary concentration required to ensure optimum compatibility
of the dyes. Alongside the recipe data, details of the substrate are very important.
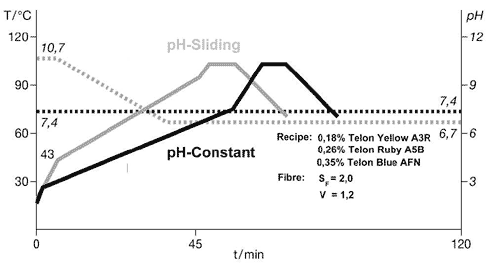
Two parameters are required to describe the dyeing properties of polyamide to be dyed in the
constant-pH process. The V value shows how quickly a standard dye exhausts onto the substrate. The
fiber saturation value (SF value) shows the maximum amount of dye that can exhaust onto the
substrate. Any dyehouse laboratory can determine these values by carrying out a few dyeings. Values
determined in bulk conditions vary between 1 and 3 for SF and 0.2 and 5 for V. For a typical recipe
with Telon A dyes, the following exhaustion ranges may be calculated on the basis of the SF and V
values given above.For V=0.2 a range of T
Start=74°C and T
End=102°C is calculated. To save time, the bath can be heated to 74°C as fast as the
equipment allows, without any risk of unlevelness. By contrast, for V=5, the final temperature T
End=31°C, while T
Start would be below the normal water temperature (theoretically below 0°C).
Consequently, heating the bath too quickly at the start would entail a risk of unlevelness. A dwell
time at the start of the process (e.g., 15 minutes at 20°C) can reduce this risk but not eliminate
it entirely. Moreover, a higher starting pH would be required. In other words, a pH-sliding process
would have to be used. Using a pH-sliding process, the bath could be heated rapidly from 31°C.
These examples show how effective optimization of the dyeing profile can be. The next section looks
at the progress made on the basis of these theoretical findings.Extending The Polyamide S ProcessAs
we have seen, it is necessary to regulate bath exhaustion to ensure the correct level of migration.
In the constant-pH process, the aim is to achieve final bath exhaustion of around 95 percent.
However, to increase reproducibility, bath exhaustion of nearly 100 percent would be ideal. This
can be achieved by reducing the pH. Similarly, if the V value of the substrate is very high and the
strike rate cannot be controlled solely via temperature, a modified version of the constant-pH
process is required. The pH-sliding process was developed from the constant-pH process specifically
for critical shades and problematic units and substrates. This process uses a combination of
temperature rises and a reduction in the pH during dyeing to control exhaustion of the dye. Under
standard dyeing conditions (pH 7), the amino end group and the carboxyl group are protonated. In
other words, viewed from a distance, this material has a positive electrical charge. A negatively
charged dyestuff molecule is therefore attracted to the PA and tries to react with it. Raising the
pH in other words, reducing the concentration of H
+ ions deprotonates the carboxyl group, leading to a negative charge. The fiber thus
takes on a neutral or negative charge, and the dyestuff molecules are not so keen to react with
it.Therefore, pH plays a major role in the exhaustion of the dye from the liquor onto the surface
of the fiber and in the diffusion of the dye in the fiber. The optimum pH range required for the
pH-sliding process depends to some extent on end groups in the fiber. Practical trials have shown
that a pH
Start that generates bath exhaustion of around 70 percent is most suitable. Since the
reproducibility of a dyeing is best at 100-percent bath exhaustion, wherever possible the pH should
be reduced to a level where this is achieved. pH
End thus depends on the substrate, dyeing recipe and auxiliaries used. This value can be
calculated using the Optidye N program. It is about 3 points below pH
Start and 0.5 points below the pH used for the constant-pH process.
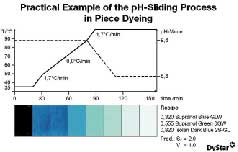
To optimize the pH-sliding process, we look at three different ranges in which the pH can be
reduced (See right).Depending on requirements (i.e., the level of difficulty), three different
points are recommended for the addition of the acid. In the process shown in Figure 4 as the most
rapid method, the pH is reduced as soon as the temperature reaches the start of the critical range.
This method is suitable for relatively uncritical conditions. The dyeing time at T
max is then equivalent to the diffusion time in the constant-pH process. The critical
temperature range can be passed through faster because the pH at the start of the process is above
the level used in the constant-pH method, allowing for more level dye uptake.In the second method
illustrated here (the universal method in Figure 4), which has proved reliable in practical trials,
the pH is reduced when the temperature reaches the end of the critical range. This generally
ensures an optimum balance between dyeing time and reliability.The third method, which is shown in
Figure 4 as the most reliable method, should be used only for very difficult shades such as
turquoise. In this method, the pH is not reduced until the temperature reaches T
max. The low level of bath exhaustion at the higher initial pH value is utilized for
migration of the dyes. Compared with the constant-pH method, the dyeing time at maximum temperature
is increased by the length of time required for dosing.Regrettably, the most suitable of these
three methods can only be determined empirically at present, as no mathematical formulae are
available. Alongside the migration properties of the dye, other major influences are the equipment
used and the composition and pH-dependence of the polyamide.Constant-pH Vs. pH-Sliding MethodsThe
two methods used to dye polyamide are the constant pH method and the pH-sliding method. The
parameters used in this illustration were calculated on the basis of the same recipe with the aid
of the Optidye N program. The unbroken curves show the temperature profile for each method (the
gray curve shows the pH-sliding process and the black one shows the constant pH method), while the
broken line shows the pH profile. The fiber saturation value of the substrate used in this example
is SF=2.0, and the strike rate is V=1.2. Both curves show that the liquor was heated as fast as
possible up to the critical range. Since virtually no dye is exhausted onto the fiber during this
heating phase, the highest possible heating gradient should be selected to save time. The critical
temperature range depends on the pH; it is slightly higher for the pH-sliding process than for the
constant pH process. A higher heating-up rate can be selected in the critical temperature range
when using the pH-sliding method than when using the constant pH method. Once the temperature has
reached TEnd, at which point exhaustion of the dyes is completed or the desired level of bath
exhaustion is achieved, depending on which method is being used, the heating rate is increased
significantly. The temperature is held at the maximum point until full penetration of the fiber is
achieved. This is necessary to stabilize the shade and achieve the desired fastness properties. The
dwell time at maximum temperature may be longer in the pH-sliding process if the maximum
temperature is used for part of the pH-sliding phase.The amount of auxiliaries needed to optimize
the combinability of the dyes varies in the examples shown here. Virtually no auxiliary is required
for the constant pH process (the optimum concentration is 0.2 percent), whereas 0.6 percent is
required for the pH-sliding process.Although the pH-sliding takes longer and requires buffers and a
control unit, it has proved effective, especially for shades where it is difficult to achieve level
dyeings. The process also improves reproducibility because it raises bath exhaustion. Setting The
pHChanging the pH during the dyeing process is a method that has been used since the 1970s to dye
carpets on winch becks, for example. Methods such as the Telomat and Dosacid processes are
well-established. Since the pH is an inverse logarithm of the concentration of H+ ions, it is often
difficult to regulate automatically. Methods used to control the pH during dyeing include pH
buffers, acid or alkali donors and automatic control and regulation units.While a pH buffer
maintains a constant, predefined pH, acid and alkali donors alter the pH as the temperature rises.
Automatic pH measuring and control units can be used for the constant pH and pH-sliding methods.
Moreover, they are often used to monitor the pH and thus control the process. However, in the past,
such units have not been stable enough to become established. A modern pH-control unit is expected
to meet the following requirements:
- robust technology with low maintenance requirements;
- user-friendliness;
- automatic calibration;
- long-lasting electrodes; and
- simple connection to dyeing units
pH-FiT, a pH measuring and control unit developed by Thies, SETEX and DyStar, has a modern
SETEX 737 control unit with integrated fuzzy logic to match the measurements taken to ideal values
using predefined rules. To make it easier to use, the unit has an automatic calibration device,
which contains buffer solutions and a KCl solution to protect the electrodes. pH-FiT is available
either as an integral system built into dyeing units or as a mobile unit, which can be connected
and operated in the same way as well-known alkali dosing units such as Adcon (automet).The pH
sensor (electrode) is built into a bypass parallel to the liquor pump. To prolong the life of the
electrodes, they are only placed in the liquor to take measurements. The bypass has a back cooling
system that cools the liquor to 80°C. This is also designed to prevent wear of the electrodes. In
the mobile unit, the acid or alkali is added via a dosing pump. If several pH-FiT units are
installed in the same plant, it makes sense to pump the chemicals in a closed-system circuit with a
dosing valve for each dyeing unit.To demonstrate how the Polyamide S process can be used to
optimize the pH-sliding process in conjunction with a pH-FiT unit, Figure 3 shows exhaust samples
taken from the dyebath after beam dyeing of a polyamide taffeta fabric with Supranol and Isolan
dyes. To achieve an optimum dyeing profile, the starting temperature for the critical range was
calculated at 48°C, while the final temperature was calculated at 88°C. Since the dyeing involved a
critical shade with high-molecular dyes, the reduction in pH was selected to ensure maximum
migration (i.e., the pH was reduced after the critical temperature range). The optimum pH range in
this case is 8.5 to 5.6. A statistical evaluation was made of the reproducibility of bulk dyeings
performed using the pH-sliding method and the Polyamide S process on the basis of approximately 300
batches dyed on the jet. After optimization of the process, the optimized and non-optimized batches
were compared.Process times were reduced by 27 percent per batch, mainly due to a 65-percent
reduction in the need to correct faulty dyeings. The use of acetic acid instead of an acetate
buffer cut chemical costs by 48 percent. Altering the chemicals used also reduced effluent
contamination, for example, but lowered the COD.
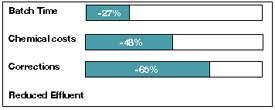
The Compudye SystemOptimizing the pH-sliding process through the Polyamide S process is only
one aspect of our approach to modern dyeing methods. Following successful application of the
Optidye N PC program, where certain data such as the recipe have to be entered manually, it is far
more effective for routine work to automate both these inputs and the transmission of the dyeing
parameters calculated to the control units. Dyehouses often have a host computer system on which
the servers and PCs depend and which is responsible for coordinating routine tasks. The Optidye N
program may use data already in the system. Alternatively, the host system may require data from
the Optidye N program. Once the dyeing recipe has been calculated, data on the recipe, substrate
and equipment are transmitted to the Optidye N program to optimize the recipe. In the simplest
case, this takes place manually. In a fully automated dyehouse, the data would be transferred
automatically via a network. The Optidye N program would then pass the relevant optimized recipe
parameters on to the control unit on the dyeing machine which needs data like T
Start, T
End, heating-up rate, pH range, pH reduction time, etc. and to the color kitchen, which
needs data on the dyes required and the optimized additions of auxiliaries.For more information on
pH control research, contact Karl-Heinz Michel, DyStar, at 49 69 2109 2734.
August 2000