media.Filtration is divided into two broad classifications gaseous filtration and liquid
filtration. The proper filtering medium must be selected based on the material to be filtered, the
operating environment and the actual operating conditions. There is no universal fiber for
filtration. Neither is there a single fibrous or textile form suitable for every type of
filtration.The food and beverage industry is diverse, offering many opportunities for filtration
products. Filtration is important in dairy, meat, poultry, alcoholic beverages, soft drinks and
bottled water. The largest single application for beverages is beer filtration. Filtration is one
of the key unit operations in the manufacture of most types of basic raw materials and in the
production of most industrial and commercial products. Choosing The Filter MediumFollowing are
some of the major criteria that must be met in selecting the proper filter medium for a specific
application:Which is the most valuable component the filtrate or the filtered streamWhat is the
particle size to be retained by the mediumWhat is the permeability of the clean filtration
mediumWhat is the solids-holding capacity of the filtering medium, and what is the resistance of
the filtering medium to the passage of the filtered streamWhat is the physical state of the
suspension to be filtered, and what is the chemical constitution and temperatureThe choice of a
filter design for a given process depends on some of the following factors:the properties of the
solids to be removed and their concentration;particle size and shape as well as the properties of
the fluid;the quantity of material to be handled;whether the solid or the liquid, or both, are to
be retained after filtration;whether the filtrate must be washed; andwhether the filtration process
should be batch or continuous. Bag Filters For Liquid FiltrationBag filters have become more
popular for liquid filtration for process filtration and for hydraulic and lubricating filtration.
Polypropylene is the favored material for most liquid filtration because of its chemical resistance
and competitive price. Nonwovens For Protecting Membrane FiltersThe use of reverse osmosis is
growing by about 12 percent per year, gas separation types are growing by about 12 percent per
year, and electrodialysis is growing by about 8 percent per year.Polymeric microporous membranes of
cellulose acetate, polysulfone, polyvinylidene fluoride, acrylonitrile polymers and nylon are used
in chemical, pharmaceutical, food processing and waste treatment operations. Submicronic particles
must be removed from fluid process streams in these operations.Membrane filtration is the
separation of the components of a pressurized fluid, effected by polymeric or inorganic membranes.
The pores of the membrane are so small that significant fluid pressure is required to drive the
liquid through them.The pressure required varies inversely with the size of the pores. These
membranes have pores so small that they will plug and blind off instantly unless they are run in
the crossflow mode.Unlike traditional filtration, in membrane filtration, all the influent does not
pass through the media, but instead is split into the permeate (filtrate) and concentrate streams.
The concentrate stream flows parallel to the membrane, hence the term crossflow.The crossflow
membrane is a pressure-driven process in which the semipermeable medium acts as a surface filter to
split the feed stream into two effluents a purified stream and a stream concentrated in solutes too
large to pass through the pores of the particular membrane.Moving from the smallest to the largest
pore sizes, there are four categories of membrane filters.reverse osmosis (RO)nanofiltration
(NF)ultrafiltration (UF)microfiltration (MF)Reverse osmosis effects separation of small solutes,
including salts with ionic radii in the Angstrom ( range. The exact mechanism of rejection in RO is
more complex than in UF and MF.Nanofiltration is a term that was coined in the late 1980s to define
membranes that were already in use and were referred to as loose RO. They have pores close to one
nanometer in diameter (1- and effect partial salt rejection.NF membranes pass a higher percentage
of monovalent salt ions than divalent or trivalent ions. Nanofiltration membranes span the gap
between RO and UF classes of membranes. Ultrafiltration standards have been developed under ASTM
Standard D-1129, but no such official definition yet exists for reverse osmosis or
nanofiltration.Microfiltration is understood as the fine end of particle filtration, with pores
from 0.1 to 1 micron in diameter. MF membranes have pores two to five orders of magnitude larger
than the other classes.MF media are actually membranes and can be run in the crossflow as well as
in the normal flow mode. This can provide longer media life. In order for the membrane filter
systems to work properly, membrane fouling must be prevented.In membrane filtration, nonwovens can
play an important adjunct role. Some of the functions of nonwovens in membrane filtration systems
follow.protection during manufactureprotection and support during testingpleat separation for fluid
distributionpleat support to prevent collapseprefiltrationThe membrane films used are usually thin
and often in the range of 4 to 6 mils in thickness. While many of these membranes have good
chemical resistance and tensile strength, they are susceptible to puncture, damage from abrasion
and fatigue failure from flexing.Also, the membranes must be protected during fabrication into
cartridges and other forms. To protect the membranes during fabrication, they are often sandwiched
between two or more layers of nonwoven material. The nonwovens are typically polypropylene or
polyester.Extruded nettings as well as spunbonds and meltblowns are used extensively as protective
media.Polypropylene is commonly used because of its broad chemical compatibility and low cost.
Polyester provides a better combination when used with nylon membranes because of the higher
melting temperatures of the two materials. Nonwovens made from virgin resins with minimal additives
are required in processes where materials must meet FDA requirements.Care must be taken when using
meltblown nonwovens to prevent shedding of particles, particularly with finer denier meltblowns.
Often meltblowns will be calendered to prevent fiber shedding.
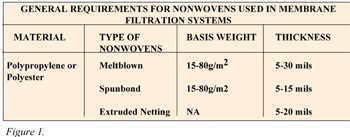
Downstream Nonwoven LayerA layer of nonwoven material adds structural support to the
folded membrane and must allow the fluid to move out of the pleat. This becomes more important as
differential pressure increases with contaminant buildup, increased fluid velocity or increased
fluid viscosity.Spunbonds are very suitable for the downstream layer because of their higher
strength and freedom from fiber shedding. Extruded nettings are also used, but they are thicker
than spunbonds. Upstream Nonwovens LayerIt is important to maintain proper fluid flow dynamics
above the membrane. The upstream nonwoven layer must keep the flow channels open between adjacent
pleats. Without support from a nonwoven layer, adjacent pleats may pinch together and impede fluid
flow. The upstream layer reduces the particle contaminant load on the final membrane filter. Proper
prefiltration greatly enhances the filtration performance of the membrane filter.The major
objective of the prefilter is to remove large, oversized particles so that the narrow pores of the
membrane filter do not become prematurely clogged. Important parameters for selecting a prefilter
are mean flow, pore size, pore size distribution and bubble point. The mean pore size correlates
well with filter retention efficiency. A narrow pore size is usually preferable. Generally, a
separate prefilter unit with nonwoven media is preferable. A separate prefilter can extend the use
of the final membrane filter by up to two times its normal life.There are some requirements for
nonwovens used with membrane filtration systems (See Figure 1). Benefit Of
Pre-FiltrationOsmonics SPIRALTEK® rolled filter medium with a spiral-wound design creates a
tangential crossflow motion that sweeps particulate across the medium and traps contaminants in
special nonpermeable sections, rather than in the medium itself. Rolled filters, much like pleated
filters, are made with different types of polymer membrane.Some of the following applications use
prefiltration systems based on the Osmonics SPIRALTEK rolled filter medium:Magnetic Media
Filtration Rolled filters provide the sharp cutoff to separate oversized particles from metal oxide
slurry. They also help to eliminate gel slugs.Specialty Inks Inks used for ink-jet printers,
ballpoint and roller pens and other specialty uses require highly efficient filters that can handle
viscous fluids and achieve the fine separation of contaminants from pigments. Rolled filters work
well in these applications.Biotechnology In processing blood serums, or biological extracts,
removal of unwanted bacteria, protein and other materials is essential. The ability of rolled
filters to hold a large volume of particulate is very beneficial. They also help to increase the
longevity of downstream sterilizing filters.Fermentation Broths In pharmaceutical and beverage
production, enzymes have to be removed once they have completed their work. Rolled filters, because
of their holding capacity, help to improve the efficiency of downstream membrane
filtration. Dry-Gas FiltrationFor many years, woven fabrics were the most typical media, but
during the last 20 years, nonwovens have become the dominant filtration media.A major advantage of
nonwovens is versatility, since almost all major types of nonwovens can be used alone or in
combination in some type of filtration application.For air and hot-gas filtration applications,
there was earlier acceptance of needlepunched nonwovens in Europe than in the United States. This
is no longer the case. Higher-speed needlelooms, improved needles, high-temperature resistant
fibers and specialized fabric finishes have broadened the uses of needlefelts in both dry and wet
filtration. Needlefelts can be engineered to provide varied pressure drops and dirt holding
capacity.Polyester fibers are important for dry-gas filtration for use up to 275°F (135°C). Where
higher temperatures are required, fiberglass, DuPonts Nomex®, PPS (polyphenylene sulfide) and
Inspecs P84® polyimide fibers are used.Polypropylene is limited in dry-gas filtration to areas
where only relatively low temperatures are encountered. This excludes its use from baghouse
installations for power generation plants, as well as asphalt-, cement- and metal-processing
installations.However, polypropylene use is growing in applications for clean rooms and hospital
operating rooms, for which polypropylene filter media are available in a wide range of types from
bulky to paper-like structures. Filters For Gaseous FiltrationClass A filters are for coarse
dust and can even retain 60-micron particles. Class A filters are not suitable for filtering
sub-micron particles.Class B filters cover a wide range of efficiencies for removing sub-micron
particles. They are often used in the form of bags supported on a metal framework, or as
cartridges. They are commonly used as filters for air conditioning systems or as prefilters for
Class C filters.Class C or HEPA (High Efficiency Particulate Air) filters are specifically designed
to deal with very fine particles at low loadings. They are typically used in combination with a
Class B filter as a prefilter.Typical applications for Class C filters are electronic and
pharmaceutical clean-room manufacturing and fermentation processing.
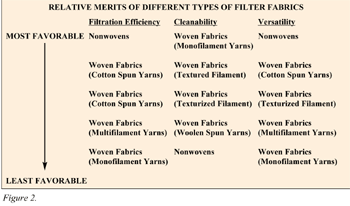
Collection Mechanism In Dry-Gas FiltrationIn dry-gas filtration, particulates are
collected by three mechanisms direct interception, impaction and diffusion.In collection by
impaction, the particles have so much inertia that they cannot follow the streamline around the
fiber; thus they impact on its surface. The mechanism involves a collision of the particle on the
barrier. Another mechanism involves particle interception. In this case, the particles have less
inertia and can barely follow the streamlines around the obstruction. Even if it doesnt actually
touch the fiber, the particle is immersed in the viscous stream around the barrier, which will be
enough to slow it down so it will graze the barrier and stop. When this happens, the porosity of
the filter medium decreases and the true filtering surface begins to form.The third collection
mechanism is important for particles that are below 1 micron in aerodynamic diameter. Diffusion is
considered immaterial for particles with diameters smaller than 0.1 micron, which is in the
Brownian motion range. In this case, the particles are so small that their individual motion can be
affected by a collision on a molecular or atomic level.Other important factors are electrostatic
attraction and gravitational settling. As the particle loading in a filter increases, the
collection efficiency increases, but so does the pressure drop across the filtering unit. The
pressure drop is used to monitor the condition of the filter and to determine when it needs to be
cleaned or replaced. Baghouse FiltrationsOne of the most common uses of baghouses is in the
electric utility industry where coal is used. A baghouse is a large metal box divided into two
functional areas. One area, the dirty-air plenum, may be a part of the baghouse proper, or it may
take the form of a gas-distribution manifold.The function of the dirty-air plenum is to distribute
the incoming gas evenly to the filtering elements or bags. The clean-air plenum is part of the
baghouse where recombination of the air from each of the individual bags takes place. The interface
separating clean-air and dirty-air plenums is the filtering medium or bags. The baghouse hopper is
a receptacle for collected particulate materials and is part of the dirty-air plenum.As discussed
in the previous section, the filter mechanisms involved in removing particles from a fluidized gas
stream are impaction, interception and diffusion. These mechanisms are responsible for the
collision of a particle on a target (the filter fabric) and are of paramount importance when the
baghouse is first brought on-line and the filtering elements are still clean.After a short time,
however, the bags become caked with a layer of flyash, and the dust cake actually becomes the
filtering medium. No matter how vigorously the bags are shaken, collapsed or pulsed, a residual
dust cake is retained after each cleaning, and the bags now act mainly as a matrix to support the
flyash. Classification Of BaghousesBaghouses are characterized and identified by the method
used to remove flyash from the bags. The bags in shaker-type units are suspended from a structural
framework, which is supported in such a way that it is free to oscillate when driven by a small
electric motor. Periodically, a damper isolates a compartment of the baghouse so that no air flows
into it. The bags in that compartment are then shaken for about a minute, during which time the
collected dust cake is dislodged from the bags. The dust falls into the hopper and is later
removed.Reverse-flow baghouses are equipped with an auxiliary fan that forces air through the bags
in an isolated compartment with the airflow in the opposite direction to filtration. The backwash
action collapses the bags and fractures the dust cake. When the bag is reinflated by being brought
back on-line, the fractured dust cake is dislodged into the hopper. If the unit operates under
suction (that is, if the main process fan is located on the clean side of the baghouse), the
reduced pressure in the baghouse may eliminate the need for an auxiliary fan. Some units combine
shaking and reverse-flow cleaning in the same unit.Reverse-pulse baghouses use a short pulse of
compressed air directed from the top to the bottom of the bag. This primary pulse usually lasts
less than a tenth of a second and aspirates secondary air as it passes through a nozzle or venturi.
The resulting air mass expands the bag and casts off the collected flyash. Shaker and reverse flow
units collect flyash on the inside of the bags, while reverse-pulse units collect flyash on the
outside of the bags.Baghouses have some practical limitations. Most bags have rather
low-temperature capabilities, ranging from 180°F to 300°F and above. Thus a practical limitation
exists when using fabrics able to withstand air-preheater outlet temperatures of 300°F and above.
Abrasion is a natural phenomenon that results from contact with flyash-laden gases. Some wear on
the filter bags occurs when flyash strikes a bag tangentially.The destruction of a bag from
chemical attack is generally due to misoperation. Processes that evolve gases at elevated
temperatures frequently produce water vapor and acid radicals, which at the acids dewpoint will
concentrate into a liquid. The acid dewpoint depends on the concentration of the constituents in
the gas, and it is almost impossible to predict.The bags tend to wear out with age. After hundreds
of cleaning cycles, the fabric weakens and will ultimately fail. The better the bag maintenance and
the better the equipment design and materials selection, the longer the bag will last.
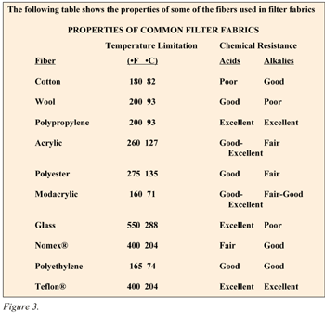
Overall Trends In FiltrationNonwovens will continue to grow in importance. Higher
performance requirements for filtration systems are being driven by industry needs for improved
productivity and by stricter environmental requirements. The ability to engineer nonwoven materials
to meet these more stringent requirements is responsible for the growing use of all major types of
nonwovens in filtration applications. The use of automotive cabin filters is now a growing market
for nonwovens. Greater household use of drinking water filter systems and home air and household
cleaning devices present good growth potential for nonwovens. In wet filtration uses, polypropylene
will continue to be the dominant material because of its superior chemical resistance and
relatively low material cost.Meltblown nonwoven use in filtration is expected to continue to grow
by more than 8 percent per year over the next five years. Meltblown technology providing higher
strength webs is now under development and will further improve its versatility as a filtration
medium. Spunbond nonwovens will also show healthy growth in filtration, both alone and in
combination with meltblown materials. Needlepunch nonwovens continue to improve their performance,
particularly for more demanding dry-gas filtration applications based on improved manufacturing
technology.In wet filtration, needlepunched and meltblown combination fabrics are growing in
importance. Dry-laid nonwovens have lost some market share to spunbonds, but higher carding speeds
and improved thermal bonding techniques will help stabilize their position in filtration
applications.Use of specialty fibers will grow in filtration. Governmental clean air requirements
are boosting the use of high-temperature resistant fiber such as DuPonts Nomex, Inspecs P84, BASFs
Basofil® and PPS for industrial and utility systems. The use of fibers that incorporate additional
functions, such as antistatic and antifungal properties, is growing.There will be greater use of
fabric functional finishes. Use of additives and treatments is growing. The use of materials in the
form of finishes or microporous film laminates of silicone or fluorocarbons, which provide better
cake release properties, will continue to grow. The application of selective absorbents, such as
carbon and zeolite, to filter media is another important trend. The formation of electrets in
filter media to improve efficiency has now been widely commercialized.There will be major areas of
growth for nonwovens in filtration. Reverse osmosis is a growing industrial process for a wide
range of industries including food, pharmaceutical and microelectronics, and it will require
nonwoven filtration media for prefiltration of liquids. There is a growing need for nonwovens of
greater uniformity for use as casting support for membrane filters.Nonwoven use will not only grow
in automotive and household applications, but will become better known to the public because of
these growing uses.
August 2000