Spinning In Control
Murata keeps competitors on their toes with its spinning, winding and texturing
technology. In the intensively competitive worldwide market for textile machinery,
manufacturers are constantly looking for an edge – either a real difference or a perceived one – to
differentiate product offerings from those of competitors. The 7th OTEMAS, Osaka, Japan, provided
just the forum for some of the world’s pre-eminent machinery manufacturers to showcase their latest
products on the continent where the bulk of the world textile machinery is sold.It was in this
heady environment that Textile Industries caught up with Japan-based Murata Machinery Ltd.’s
Junichi Murata and Larry Kenyon. In a refreshingly frank interview, these Murata executives
discussed their products, the history of product development and future directions for the company.
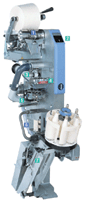
Murata’s No. 21C Process Coner has a straight yarn path from the center of the photograph
above shows (1) Pac 21 process cartridge winding system; (2) indicator; (3) waxing device; (4) yarn
clearer; (5) splicer; (6) process cartridge tension manager; and (7) Bal-Con balloon
controller.Murata has made headlines over the past few years with the development of its high-tech
vortex spinning system, but it was a more basic product that had Kenyon gleaming in Osaka – the No.
21C Process Coner, a new Muratec automatic winder. The winder features such improvements as a newly
developed tension/pickup/monitoring and winding control system, and a more stable traverse
mechanism. Winding technology has been in development for more than 20 years at Murata, resulting
in the first completely new winder for the company since 1979. Murata, according to Kenyon, was the
company that first developed the splicer that reduces knots and facilitates linking of the winder
to ring-spinning frames. By getting good splices and efficient winders, he said, smaller bobbins
can be used as well.”That’s [smaller bobbins and linking] the real key of this process. By making
smaller bobbins, the spinning frame can run faster and use less power. It’s like a really small,
efficient car that can run pretty fast and uses less gas than a big fast car, you know. So that’s
the theory behind that, and it probably made ring spinning survive for these last 20 years.”A lot
of people can modernize and buy new ring spinning now,” he continued. “If they had to run really
big bobbins – and the operators had to carry them to the winder and put them on by hand – I don’t
think there would have been any payback to ring spinning. So that’s where Murata started, you know,
roughly 20 years ago.”Murata, according to Kenyon, was a pioneer in linking. “When we designed our
winder link, we made a winder where the wound bobbin came into the back – and the empty one came
out to the front and circulated around. Everybody else brought their bobbins down the front, put
them in and brought them back, so they have these cumbersome methods to handle bobbins. “We’ve had
this patented direct-link system, and I say over the last years, our winder was a really great
winder,” Kenyon said. Murata’s manufacturing was automated, which enabled the company to produce
its winder at a low cost. “We could compete on a cost basis where everybody else had to go to a new
design to compete on a cost basis,” he said.Competitors were forced into revamping designs because,
during the profitable 1980s, a number of companies did not invest in new manufacturing processes,
Kenyon said. Murata, however, did. “One of the nicest things about [Junichi Murata] is he owns this
company, and he puts all his money back into the company. So through all these years, when our
competitors were owned by people who knew they were going to sell their companies – so they took
all the money and sold – he modernized our company. We’ve been staying highly modernized in
manufacturing. We were not forced to change our winder like the other people were.But as winding
features became more widespread – such as the ability to remove a length of yarn with a slub –
Murata began considering a new design for its offering. “More and more, we did see the need to
redesign our winder and come out with a more electronically controlled winder.” Murata’s new
product, first shown at OTEMAS, features a far greater degree of electronic control. “It allows us
to put more features in without dramatically changing the design of the winder,” Kenyon said. “You
just change the software – rewrite some software portions as you change features in the future. Now
we have clearers that take out long, thin places, and we have clearers that detect hairiness. It
takes a long time to detect hairiness, so you only want to unwind it for a hairiness fault. You
don’t want to unwind 80 meters for slub when a half-meter will do. You want to unwind exactly the
amount of yarn that you need to, so that’s what made us go to a more electronic winder.” Texturing
In texturing, Murata has also been selling machines for more than 20 years, primarily to Asian
customers. “I think we listened to the Asian market, and we dominate the Asian market in texturing
machines, and for spinning winders,” Kenyon said. The company, however, has not always been as
attuned as it would like to the Western market. “The Asian market was big, and they wanted simple
machines and they all wanted the same machine, so it’s pretty good for us because, remember, our
concept is to go very quickly into automated manufacturing, not to have an army full of people
running around making things by hand. We jumped very quickly into automated manufacturing, and that
concept worked well in Asia, because there’s very little difference in Asian machines from company
to company or country to country. We are very big in the texturing market and the spinning winder
market in Asia. We haven’t been in America. We do have a nice installation of texturing machines in
America, but they are specialty machines. No one has bought the commodity texturing machine in
America for a number of years. The people that have them have a lot of machines not running.
They’re going to get their machines that are idle running before they buy some more.”
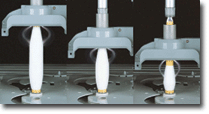
Murata’s Bal-Con balloon controller maintains even winding tension from start to finish,
enabling more stable, high-speed winding for high-quality packages.MarketsOf all the markets Murata
serves, China is definitely the hottest right now, Kenyon said. “In fact,” he said, “if you take
China and then you take the South Asian countries around China, almost all the machines are going
either to China, or they are going on the border of China. The yarn’s going to China. Some
companies maybe don’t quite have the courage to install in China yet. They want to wait and see a
little longer, but most of the machines are being sold to Chinese people, although not always in
China. Remember, a lot of Chinese people are outside of China, but they have the contacts to sell
yarn to China.”Added Junichi Murata: “Chinese competition is not fair because it is not a
democratic country. They don’t have any labor unions, and their welfare and insurance are not very
good. For all intents and purposes, they can produce textiles so cheap, and they export to all of
the world. They are talking double deal – okay, it’s both ways, we can export to many countries,
but we also have to import. But I don’t think it’s true because when we export our machines to
China, there are many expensive duties and also some discrimination from government. But in the
United States and Japan, it’s free… the government doesn’t touch anything. Then we can compete on
the same ground.”SpinningDespite advances in winding and texturing, it is spinning that has earned
Murata its reputation as an innovator. In the late 1970s, the company succeeded in developing and
commercializing the Murata Jet Spinner (MJS), the world’s first air-jet spinning frame, Kenyon
said. The MJS feeds sliver directly to the package, integrating the roving, spinning and winding
processes; and reducing labor, energy and maintenance costs.
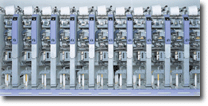
Murata’s No. 21C Process Coner“We right now have an AO2HR, and that is our MJS series,”
Kenyon said. “We’ve sold about 2,500 of these machines, most of them in the States. This machine
will run 100-percent polyester and 100-percent acrylic. It really is a poly/cotton machine. That’s
the sweet spot on the tennis racket. It goes at bottom-weight twills and some knits, but it really
is a poly/cotton knit machine, where you want no pilling.”After the MJS, Murata turned its
attention to its acclaimed vortex line. The Murata Vortex Spinner (MVS), according to Kenyon, is
the world’s first spinning frame to achieve knotless yarn with 100-percent carded cotton at speeds
up to 400 meters per minute (m/min). Murata currently has about 200 machines installed and hopes to
increase that considerably, Kenyon said. “I think, with the time in the market, we would like to
have been at 1,000. But the market has been changing over the last few years. We started installing
these machines and perfecting them. As we got them perfected, the market became unperfected.” When
the MVS was first introduced, there was considerable interest from U.S. companies, but Murata had
difficulty making the machines fast enough to meet demand, and lost a window of opportunity. “When
you first come out with a machine, it’s expensive to make. We sold 100 machines roughly to two
people, and I frankly would imagine [Murata] lost money on those machines. Everything’s made by
hand, and we were changing our hardware know-how. When you change your hardware know-how, you
redesign. Then you go to those first customers and you say, “you know, I’m sorry, but this part is
not the way it should be,
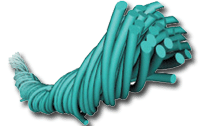
The Murata Vortex Spinner produces knotless yarn from 100-percent carded cotton.it should be
this.” So you give them this and, frankly speaking, I imagine you lose a lot of money. We have to
go through a period of that and then, once we get the machine design stable, we go into automated
manufacturing, and that’s when you can get aggressive on the price and still make money. If you
look at a car, every part is designed the cheapest possible way. Even on a Lincoln Continental, the
parts are made economically. No one can hand-make car parts anymore. So I think we’re at the stage
now where we have pretty well frozen the design, and the people in the factory can start making the
parts more automatically. We will be more aggressive, but the market is kind of slow right now. But
a good number of people in the market want this machine.”Kenyon continued: “Mr. Murata has always
given us the technology and tools to dominate markets, and once he decides to go into a market,
you’ll notice he doesn’t make a me-too machine, does he”
December 2001