I
n recent years, the term “nanotechnology” has spread across the globe like wildfire.
Millions of dollars in research grants and investments are being devoted to making products less
than 100 nanometers in size. Unlike many other aspects of the US textile industry, which face
considerable pressure, nanotechnologies are generating significant interest.
Within the past decade, the industry has rediscovered and continues to develop technologies
that enable production of extremely small fibers – nanofibers – using a process called
electrospinning.
The Electrospinning Process
Electrospinning is not by any means a new discovery. Its roots go back to the early 1930s,
when the first patent was issued. Simply stated, electrospinning is a process that uses the
electrostatic attraction between a charged polymer and a grounded or oppositely charged collection
plate to produce extremely fine fibers ranging in diameter from less than 10 nanometers (nm) to
several micrometers. Recent developments have shown it can be performed on polymers both in the
molten state and in solution.
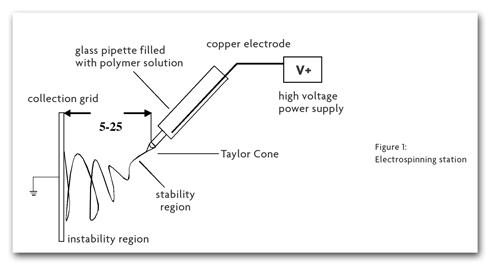
The polymer is held in a syringe or other type of container
(See Figure 1). The charge can be applied directly to the syringe so that when polymer
passes through, it receives a surface charge similar to that applied to the syringe. As the voltage
to the system is increased, the strength of the electric field generated eventually becomes greater
than the viscoelastic properties and surface tension of the polymer, and a tiny cone – often
referred to as a Taylor Cone – is formed.
Further increasing the electric field’s strength will deform the Taylor Cone until a fine
fiber is extruded from the cone’s apex. When working with solutions, this strand will continue as a
stable jet for a short period of time before the instability or whipping region occurs. This region
further decreases the fiber’s diameter as the solvent evaporates from the solution, leaving an
extremely small fiber. It is important to note that due to a much higher viscosity and lack of
solvent evaporation, fibers electrospun from the melt do not undergo an instability region and as a
result have much larger diameters.
Electrospun fibers typically have been collected as a random nonwoven mat, and most of the
applications developed today reflect this configuration
(See Figure 2). However, advancements in collection techniques continue to be a major
focus of research. As a result, it is possible to collect aligned continuous fibers that can be
twisted to form yarns composed of nanofibers.
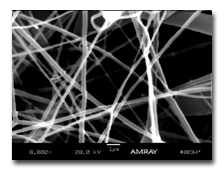
Figure 2: A scanning electron microscope (SEM) micrograph showing electrospun polylactic
acid glycolic acid (PLAGA) nanofibers
Nanofiber Applications
It is one thing to successfully produce nanofibers, but it is more important from an
economic standpoint to find a suitable application for them. One of the main goals for nanofibers
has been to produce the strength they should theoretically possess. In conventional fibers produced
today, there are fairly defined limitations to the percentage of crystallinity that can be obtained
in a fiber/yarn form.
Another potential benefit of nanofiber technology is the tremendous increase in
surface-area-to-weight or -volume ratios. The lure of nanotechnology stems from the possibility of
redefining these limitations.
For example, the actual thickness of a carbon/carbon bond is approximately 1 nm. If a
5-nm-diameter fiber is produced, the molecular chains are effectively forced to align in a highly
crystalline manner. Ideally, the resultant strength of the fiber produced will be determined by the
strength of the carbon/carbon bond in the molecular chains of the polymer.
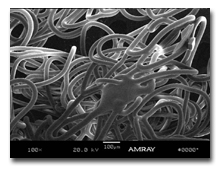
Figure 3: SEM micrograph example of a nanofibrous mat
Varied Applications
These advantages of electrospun fibers make them very appealing for a broad array of
potential applications in many industry segments. The composites industry is especially interested
in nanofiber technology because it potentially allows the creation of products that are much
smaller and lighter in weight, yet capable of performing at the same or enhanced mechanical
standards compared to traditional composites. If the fibers can be collected individually and
aligned to specific orientations, it is possible to increase the maximum volume fraction of fibers
in a matrix, thus increasing the material’s strength. The increased surface-area-to-weight ratio
also will allow for improved bonding with the matrix to help prevent failure due to pullout
of the fibers.
In addition to the composites industry, the filtration industry has begun utilizing
nanofibers, and in some cases has generated commercially available products. Nanofibrous mats,
similar to that shown in Figure 3, can be made with varying fiber diameters based on several input
parameters. With differing fiber diameters, the pore size of the mat can be controlled to a fairly
high degree. As a result, nanofibrous mats can be designed to block out molecules of specific
sizes. In addition to mechanical filtration as described above, nanofibrous mats can be treated so
that when molecules of specific design pass through, a chemical reaction takes place that
neutralizes any potential hazards.
Similarly, nanofibrous mats are being explored as biomedical grafts and wound dressings. It
has been found that cells can adhere to and proliferate into the mats with a great deal of success.
Also, because of the extremely small size of the nano-fibers, the potential exists for layering of
different polymers with specific functionalities. Electrospinning techniques can be applied to
nearly every polymer of sufficient molecular weight, including those that are Food and Drug
Administration-approved, thereby limiting issues of biocompatibility.
The application of nanofibers is not aimed only at specialized industries involved in
technical textiles. The introduction of microfibers into traditional textile markets
has created a wave of new garments claiming stain resistance and extremely soft hand. The
introduction of nanofibers and nanocoatings can take apparel innovations further. For example,
man-made cashmere has been developed with a softer hand than that of worsted wool, offering the
feel of cashmere at a fraction of the cost.
The Future Of Nanofibers
One of the greatest attributes of electrospinning and nanofibrous technology is that it is
still in its infancy. Numerous ideas and concepts have been proposed, but in many cases, the
theoretical expectations have yet to be realized. It has been shown that nearly every polymer
imaginable can be electrospun from either solution or melt, so there are no limitations in that
regard. Today, the fibers are collected in the form of a mat of staple-aligned fibers. Future
developments and processing technologies must find a way to orient a continuous fiber for the
technology to advance in the right direction. It has been shown that electrostatic attraction and
repulsion can be used to control the path of the jet. With enhanced methods, it may be possible to
produce woven or braided fabrics directly from the electrospinning station. While the process
awaits mechanical and processing mechanisms that are capable of maneuvering single fibers into
specific configurations, much work still needs to be done to optimize the conditions for making a
specific fiber diameter with a specific polymer. Only after the process can be controlled will the
technology be ready for full optimization and full realization of electrospinning capabilities.
Editor’s Note: Jason Lyons and Jim Kaufmann are affiliated with Philadelphia-based NovaComp
Inc. The authors wish to thank Drexel University, Philadelphia, for use of the scanning electron
microscope, and Frank Ko, Ph.D., for his assistance, both educationally and financially.
August 2004