I
taly-based automation specialist U.T.I.T. Automation S.p.A. was established in 1953 by
the Ognibene family to manufacture material handling systems for an array of industries including
textiles, chemicals, food, pharmaceuticals, paper, metals and others. The company, whose Textile
Division designs, manufactures and installs material handling systems in staple-fiber spinning
plants, installed its first transportation system in a spinning mill in 1965. Solutions offered
include bobbin transport systems and package handling systems. Recently, it has organized its
offerings relevant to the specific ways for the spool transport from the roving frame to the
spinning frame.
Bobbin Transport System
According to U.T.I.T., the bobbin
transport system is the area in spinning mills where investments in automation are most easily
justified. Noting that automated bobbin transport offers the advantages of labor savings and a
substantial increase in bobbin quality, the company explains that the flyer bobbin is one of the
most delicate intermediate products to handle for two reasons: the roving wound around the bobbin
is completely unprotected and is therefore highly susceptible to damage; and all roving defects are
transferred to the yarn and cannot be corrected. Automated bobbin transport eliminates the need
both to handle the bobbin or touch the textile product and to maintain intermediate storage areas,
where bobbins can accidentally age, get dirty and deteriorate.
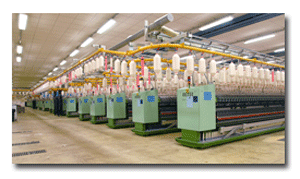

bobbin.
Random Creeling
The random creeling method of bobbin
transport takes its name from the way the empty bobbin is changed with the full one on the ring
frame creel — randomly, when the bobbin naturally runs out of roving. Bobbins are transported via a
closed-circuit overhead chain routed along the aisles between ring frames. The chain interfaces to
the flyer that feeds the system with full bobbins.
The overhead circuit slowly moving on ring frames works as a dynamic buffer of spare full
bobbins ready to be used by the operators. Whenever a bobbin is changed, the empty one taken from
the creel is loaded onto the circuit and carried back to the flyer; here, either by means of the
roving frame automatic exchanger or manually, empty bobbins are exchanged for full ones. Whenever
the flyer frame automatic exchanger sees an empty bobbin coming, it stops the circuit and exchanges
the empty bobbin for a full one.
Block Creeling
The main characteristic of the block
creeling transport solution is that flyer bobbins on the ring frame creel are changed in preset
quantities, or blocks. Components called trains run along this circuit, with each train conveying a
bobbin block to be changed. During the working cycle, a full bobbin train positions along the
spinning machine in front of the bobbin block to be changed, and the operator replaces empty
bobbins on the creel with full ones, transferring the empty bobbin block to the train.
The train returns to the roving frame area, where empty bobbins are unloaded automatically
and full bobbins are loaded for the next conveying cycle.
Automatic Block Creeling
According to U.T.I.T., the automatic
block creeling system maximizes flexibility by combining flyer, product and ring frame. Such
combinations can be modified easily and quickly using a monitoring PC, which functions as the main
user interface.
In this system, empty bobbins on the ring frame creel are changed by creel lines — blocks
that equal one-sixth or one-quarter of the total number of bobbins on the ring frame. The spinning
frame consists of pairs of tracks — one per line A, B, C, D, E, F. In each track pair is inserted a
bobbin train, which supplies the spindles.
As soon as the bobbins on a train are nearly empty and the bobbin diameter is thin enough,
the operator introduces a train of full bobbins in the twin track beside it. The creel operators
then splice the rovings to new bobbins and send the empty bobbin train back to the flyers, where
the empty bobbins are unloaded and full bobbins are loaded automatically for the next conveying
cycle.
Such a system also can be used for total changing of ring-frame bobbins without stopping the
spindles.
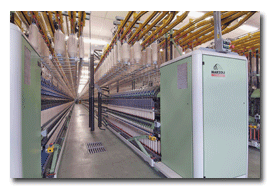

poor-quality bobbins.
Total Creeling
In U.T.I.T.’s total creeling system,
all the bobbins on the ring frames are replaced simultaneously. The four or six working lines of
the ring frame creel are made of U.T.I.T. MWL track on which the transport chain, or train, carries
the line bobbins. As soon as the bobbins are nearly empty, the operator orders the bobbin change by
means of a user panel; empty bobbin trains leave the creel one by one, and full bobbin trains are
introduced in the creel.
An overhead storage area, which works as a buffer between the roving frames and ring frames,
contains full bobbin trains, available for the next bobbin change, and empty bobbin trains, as
supply for flyers.
The automatic total creeling transport system maximizes flexibility in the link between the
spinning and roving frames, with the flyer-product and product-ring frame pairings, U.T.I.T.
reports. Such combinations can be modified easily and quickly using a monitoring PC, which
functions as the main user interface.
Wool Bobbin Transport
The company points out that the
aforementioned transport solutions also have applications in the long-staple wool and acrylic
fibers field to transport bobbins from finishers to ring frames. Bobbins from the finisher are
automatically loaded onto the transport circuit by means of a special bobbin lift. Bobbin tubes,
after stripping, are automatically unloaded from transport and collected in a container.
When bobbin weight, product variety and small lot sizes are taken into consideration, the
total creeling system is the most suitable for wool spinning, according to U.T.I.T.
Automatic Bobbin Stripper
After the empty bobbins have been
unloaded and transported from the ring frame, they must be stripped of any unused roving before
they can be filled again and returned via transport system to the ring frame. Building on 15 years’
experience with bobbin-stripping processes, U.T.I.T. has developed an automatic bobbin-stripping
machine that it says offers an innovative, efficient and reliable solution for a fully automated
spinning plant.
In the automatic stripping process, an empty bobbin is removed from the transport system
hanger as it passes through the stripper, while full bobbins remain on their hangers and also pass
through. A patented air veil on the stripper spike prevents the roving from being trapped between
the spike and the bobbin. The machine also checks for and finds the roving if it should break
during the stripping process, opens the fiber during stripping, features a variable stripping cycle
and prevents fiber pollution from other blends or colors.
Package Handling Systems
U.T.I.T. also offers automated
centralized and end-of-line package handling systems, pointing out that installation of such a
system represents a considerable turning point in the automation of spinning mill processes. The
automated collecting and packing system allows operators the flexibililty to break the production
rhythm and customize the flow of the final packed units. The automated system interfaces directly
with the production line and provides fully independent package handling and packaging processes.
According to the company, the main advantages of an automatic package handling system
include: labor rationalization and savings; optimization of spinning and storage space; production
reliability and continuity; final production feedback; elimination of manual handling of packages;
and separation of production and packing operations.
Editor’s Note: European Correspondent Piergiuseppe Bullio and Associate Editor Janet Bealer
Rodie contributed to this report.