There are more ways to make a manufacturing operation smart than simply investing in the latest
state-of-the-art equipment — which, as well as requiring a good bit of investigation and planning
ahead, may turn out not to be the optimal solution by the time it is implemented.
Knoxville, Tenn.-based QualPro Inc.’s Multivariable Testing (MVT®) process is one smart tool
manufacturers can use to quickly and cost-effectively optimize plant operations without investing
in new, advanced equipment. The concept is relatively simple; it isn’t high-tech in the way that
smart manufacturing solutions typically are, but it can be used to optimize even the most advanced
manufacturing operation. The main components are ideas, which represent about 75 percent of the
input; and data, which account for about 25 percent. And the input of employees who are directly
involved with the processes being optimized adds another benefit because they have a stake in the
project’s success and will work hard to see that it succeeds.
MVT traces its roots back to the 1960s, when QualPro founder Charles Holland, Ph.D., was
working as a statistician specializing in process control and improvement at Union Carbide Corp.’s
Nuclear Weapons Manufacturing Division in Oak Ridge, Tenn. There, Holland began to develop the
process to help solve a problem at the plant.
Holland founded QualPro in 1982 and began to offer training seminars and consulting services
— originally to manufacturers wanting to improve processes at their plants, but eventually also to
other types of businesses including transportation, logistics, service, retail and others. Over the
years, QualPro has worked with more than 1,000 enterprises, including textile manufacturers such as
Milliken & Company, Beaulieu of America, DuPont, Unifi Inc. and Sage Automotive Interiors Inc.,
among others.
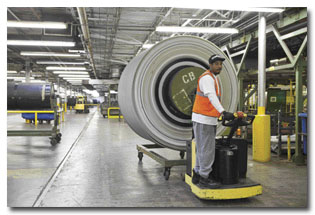
An associate transports fabric between processes at Sage Automotive Interiors’ Cotton
Blossom laminating plant, which used MVT to help it correct a quality problem.
MVT Methodology
The MVT process uses statistics to test ideas for improving an operation. It is a very
disciplined, multi-step process for testing multiple variables simultaneously, thereby reducing the
number of tests needed to find the best solution. From the beginning, the process has included
brainstorming among the employees who are closely involved with the operation in question, and who
are encouraged to bring all their observations and ideas to the table. The ideas are culled, and
those deemed practical, fast and cost-efficient are put into the test. As it turns out, in any
given project, about 25 percent of the ideas acted on are found to be beneficial, about half have
no effect, and the rest have a negative effect.
“MVT takes a lot of haphazard thoughts and quantitative data and rapidly tests them and
enables you to improve processes with the resources you already have, without having to invest in
big capital and new technology,” said Vice President and Principal Art Hammer, who has been with
QualPro since its beginnings. “And, if you were going to buy new smart technology, you could run a
MVT to figure out how to better use the technology and make it even smarter.”
People Power
The participation of people working directly with the targeted operation is key to MVT’s
success in any given situation. “That is absolutely core to our entire process and always will be,”
Hammer said. “Get a person from the third shift, someone from maintenance who knows the
idiosyncrasies of different machines and how they may not be operating to standard expectation. You
need to be in there elbows and elbows with all those from the different shifts.”
Data tools include a wide range of factors — for example, denier, online instrumentation,
machine speed, temperature, flow rate, tension or pressure as a polymer is extruded, the size of
the holes in the spinneret, or an additive being sprayed on a textile. There are also variables
among the people doing a given job, Hammer said. “Say the job is to correct breaks. All have been
trained, but no two people do it the same way.
“By looking at both historical and dynamic bases, you can see long-term trends as well as
what is happening at this moment,” Hammer said. “However, the data never replace what’s coming from
the local workforce. The integration of brainstorming and data tools brings better MVT results.”
Unifi: 14-step MVT Yields Improved Product Quality
Textured yarn manufacturer Unifi Inc., Greensboro, N.C., has used MVT to improve many
different operations over several years. At its REPREVE® Recycling Center, which opened in May
2011, the company had installed optimized, state-of-the-art processing equipment, but it wanted to
push the machine’s capabilities further. QualPro designed a 14-step process that helped Unifi
expand those capabilities.
“That process allowed us to look at the machine in more detail — to look at every different
knob and parameter, break it down into different sections and go to the upper and lower side of
every function,” said Todd Baker, plant manager at the recycling center. “We found that the
optimized processes the supplier gave us were not truly optimized. For example, we moved the needle
quite a bit on the color we were able to achieve.” In addition, improvements were achieved in
viscosity and other characteristics of the polymer itself.
Unifi also was concerned about variations in the quality of the polyethylene terephthalate
(PET) bottles and other PET waste it processes into Repreve fiber and yarn. It was able to refine
the filtration system to eliminate contamination in the raw material derived from the PET waste,
thus enabling improved, more consistent quality of the product it supplies to downstream customers
such as Patagonia, Nike, The North Face and many others.
Baker said the results enabled Unifi to develop a troubleshooting guide for use in the
plant. The company now is using MVT to test its lab formats and other practices.
“If you take the MVT tools and break out everything in a methodical way, you can really
identify ways to improve your business, costs and efficiencies,” Baker added. “It goes far beyond
just the machines.”
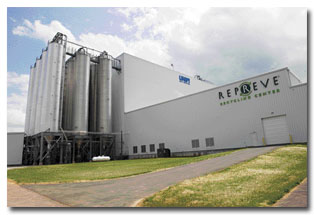
Unifi Inc.’s REPREVE® Recycling Center implemented QualPro’s MVT® process to help it push
the capabilities of its machinery as well as achieve consistent high quality in the Repreve fibers
it sends to its customers.
DuPont: Reduced Costs, Increased Productivity
DuPont, Wilmington, Del., also has utilized MVT to improve efficiencies in numerous
operations. In the 1990s, when it was producing polyester yarn and staple fiber in Wilmington,
N.C., it implemented the process to help it reduce costs and remain competitive with imports from
lower-labor-cost countries.
“At that time, capital was hard to come by, and returns on polyester weren’t large enough to
justify a lot of new capital,” said Ron Burger, former plant manager at the Wilmington facility.
“MVT offered us the best opportunity to remain competitive and get costs down, which we did through
a number of projects. We dropped maintenance costs because of our success in reducing the number of
equipment failures, dropped unit costs by 25 to 30 percent and got productivity increases of 25 to
35 percent.”
The plant’s workforce got heavily involved in the project. “We tapped into their ideas, and
that’s what made it so successful,” Burger said. “MVT is a very disciplined system of trying out
ideas and evaluating them using actual data. Not all of them work, and you begin to home in on the
good ideas right away, and that’s where all that productivity and quality improvement came from.”
Burger found MVT to be an excellent training tool for the employees. “It trains them to know
what’s important on their processes, and it will sort out myths and legends and throw out things we
all believe to be true that aren’t,” he said. “Some real leadership develops within your employees
once this process starts because it begins to tear down any barriers within your organization that
keep good employees from contributing fully.”
May/June 2013