Since its 1985 debut in Frankfurt, Techtextil, the International Trade Fair for Technical Textiles
and Nonwovens, as the organizer, Messe Frankfurt GmbH, has named it, has been among the leading
exhibitions dedicated to technical textiles and their applications. The more than 24,500 visitors
from 96 countries at Techtextil 2011 attest to the show’s success.
Not only the record visitor numbers, but also the fact that 1,207 exhibitors came from 50
countries confirms the importance of Techtextil Frankfurt. On top of that, 55 percent of the
visitors were international — 9 percent more than in 2009. According to the organizers, after
Germany, most of the visitors came from other European countries, Turkey and the United States.
Top-level visitors from India, South Korea, China and Japan also were present.
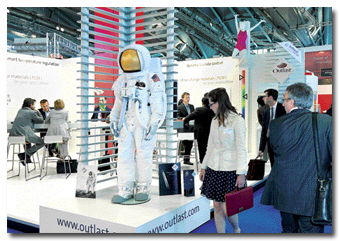
Phase change materials, first developed for aerospace applications, today offer a wide
range of application possibilities.
Still Going Strong
After the crisis years 2008 and 2009, most of the global players in the textile machinery
manufacturing sector reported a considerable upswing in 2010 and the beginning of 2011. After the
successful INDEX 11 nonwovens exhibition in Geneva, Techtextil further signals that textiles for
industrial and technical applications are key components for the future success of the textile
industry. Whether and how the current battle on the currency front will influence the markets is
still unpredictable.
The record new visitor numbers go along with the increasing technical textiles applications
and, of course, with more favorable projections for 2011. Many exhibitors said they were surprised
by the number of visitors who had concrete plans and investment strategies for the near future. The
positive mood reflects the fact that research and development of new machinery, fibers, yarns,
fabrics and such are generating new products nobody could dream of some years ago.
New Products
Techtextil is a marketplace for new ideas and products. The list of products is virtually
endless, because there is no standard range: Every product is tailor-made for the end-use.
Following is a very limited selection of products shown.
Austria-based Lenzing AG seems to be in a very comfortable position. Its fibers are derived
from a sustainable raw material, wood. Tencel® is normally used for apparel, but at Techtextil, the
company presented fiber types for a wide range of automotive applications: in powder form for
compounds for injection molding; and as a special fiber type for seat covers, headliners and
carpets. Another application of the viscose fibers is heat protection. Lenzing FR® offers
protection from heat and flame in a variety of applications. Lenzing reports that distinctive
thermal insulation properties combined with permanent flame resistance enable the body to stay cool
and dry, and prevent heat stress and heat stroke. The flame-resistant (FR) fiber is now also
available in colors that remain fast in the textile even after washing.
Flax, or linen, is still an underestimated fiber with excellent inherent properties. Norafin
Industries (Germany) GmbH presented nonwovens made of flax, which combine flax fiber’s natural
characteristics — robustness, ultraviolet resistance, vibration-absorbing properties, relatively
low weight and positive eco balance — with the spunlaced texture. Applications include wind energy,
innovative interior designs, boat building and packaging. The nonwovens can be finished to have FR,
hydrophobic or oleophobic properties.
Phase change materials (PCMs) have been on the market for years. At Techtextil, Outlast
Technologies Inc., Boulder, Colo., presented a new bicomponent fiber featuring a PCM core and
polyester sheath. The fiber is said to combine the PCM’s temperature-balancing property with
conventional polyester fiber characteristics.
Textile membranes have become increasingly important for stadiums and other public
buildings. One problem is the treatment of the fabric. Sanitized AG, Switzerland, presented
Sanitized® PL 24-32, an Oeko-Tex®-certified phthalate-free additive that protects soft polyvinyl
chloride (PVC) against fungi and pink stain. It is also effective against streptoverticillia and is
said to be the first product on the market that offers optimal material and hygiene protection as
well as good ultraviolet and heat resistance.
Weaving is probably the cornerstone of technical and industrial fabrics. Stäubli S.a.s.,
France, producer of dobby and jacquard machines, also supplies clever accessories for technical
textiles weavers: the Magma T12 warp tying machine is especially suitable for coarse to
medium-count technical yarns and polypropylene tapes. Its rigid design features cutting-edge
technologies and includes an optical double-end detection system that checks the separation process
thread by thread, eliminating tying of double ends.
Picanol NV, Belgium, is a leading producer of weaving machines for industrial fabrics.
Marketing Manager Erwin Devloo said he was pleased with Techtextil visitor feedback. Picanol
commits some 30 percent of its product management capacity to technical textiles. A similar
percentage of R&D is dedicated to novelty applications. The company has developed technically
advanced solutions for applications such as tire cord, conveyor belts, canvas, industrial glass,
monofilaments, one-piece-woven airbags, and many more. Devloo said the OMNIplus 800 airjet and the
flexible OptiMax rapier machine are designed for the mid- and high-end technical textiles markets.
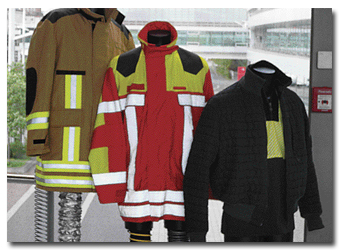
Protective garments comprise one of the most promising technical/industrial fabrics
sectors.
Recycled Fibers
Filature Miroglio, Italy, is following a new path: Its Newlife™ yarn comprises a complete
and certified system of polyester filament yarns made of 100-percent recycled polyethylene
terephthalate (PET) bottles sourced in Italy. By 2015, this fiber should replace all of Miroglio’s
virgin polyester filament yarns. The innovative platform is certified through a comprehensive
production approach and offers a wide range of high-performance recycled PET filament yarn
including partially oriented, flat, textured, microfiber and hollow yarns for numerous
applications. Because the yarns are spun-dyed, additional colors can be supplied as well as the
existing color range.
Happy Exhibitors
According to a survey conducted by Messe Frankfurt, 90 percent of all exhibitors were very
satisfied with the fair results, which are attributed to growing demand from the various
application areas and improved general economic conditions.
Regina Brückner, CEO of Germany-based Brückner Trockentechnik GmbH & Co. KG, a leading
supplier of finishing machinery for industrial fabrics, expressed her satisfaction with this
Techtextil: “Our booth was occupied all three days with a lot of promising and even firm contacts,
particularly those asking for our coating technology.”
Rudolf Feucht, sales manager, Toyota Textile Machinery Europe AG, Switzerland, reported high
demand for glass filament fabrics. He said fine yarns are especially in demand and the Toyota
weaving machines are highly suitable for fine filament glass yarns, which are used mainly for
electronic products.
Expanding Coverage
For some 10 years, there have been discussions about whether Techtextil should last three or
four days. In the beginning, there was an exhibition only; then, an extensive conference program
was launched; and then, Avantex was added to present high-tech apparel textiles; followed by
Material Vision featuring new materials for design and architecture; and, this year, Texprocess
presenting textile and flexible materials processing technologies. More than 500 participants
attended the restructured Techtextil and Avantex Symposiums, which presented some 60 lectures
covering trends and developments for products, materials and technologies. After this extensive
program with all the competing events, many exhibitors feel three days are not enough anymore.
The next Techtextil in Frankfurt will be held for four days — June 11-14, 2013 — again
concurrently with Texprocess and in association with Material Vision.
July/August 2011