New direct disperse ink technologies will simplify the polyester ink-jet printing process and help grow this printing segment.
By Rene Wolferink
Over the past few years there has been an increase in the use of polyester fabric for the fashion printing market. Polyester is making its mark as a “green” fiber, and fiber prices are down as well — although polyester prices have risen again since oil prices stabilized. Many companies in the more traditional printing arena — reactive and acid digital — have tried digital disperse printing. At the same time, flag and banner companies also have tried to enter the fashion market. Some companies have entered this rapidly growing market successfully, but many other companies have been unsuccessful. Printing with disperse dye inks may seem to be easier than printing with reactive dye inks, but the fact is, there are many challenges presented by the process.
Failure Areas
There are many failure areas to consider including the fabrics, inks, printing machinery, and auxiliary equipment for fixation and washing.
For a reactive dye ink-jet printing company to change to disperse dye ink-jet printing, the fabrics do not have to be that different. But a producer that operates in the flag and banner market is often less knowledgeable about flexible, stretchy and lightweight fashion fabrics. Depending on the company’s background, there may be a steep learning curve, especially in fabric handling.
Disperse sublimation (transfer) inks are a common choice, but there also are disperse direct inks available on the market. Each type of ink has its own specifications, and the choice of ink usually will also determine the machine type. This could be a low-, medium- or even high-speed machine. Current machine speeds range from a very low 10 linear meters per hour (m/hr) to 4,000 linear m/hr.
The manufacturer also has to select auxiliary equipment to permanently fix the inks to the fabric. In the dye sublimation sportswear market, dye sublimation calenders — transfer calenders — are commonly used. In the flag and banners market, it is very common to have fixation done using a beltless fixation system, usually featuring a heated roller that guides the fabric. In the traditional fashion fabric printing market, it is most common to steam fix using superheated steam, followed by a reductive washing cycle. Each method has its positive and negative side effects.
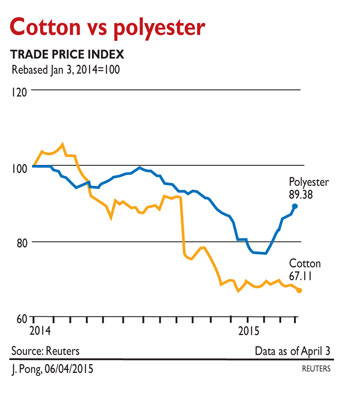
Decreasing polyester prices made the fiber competitive with cotton for fashion apparel.
Digital Dye Sublimation Printer For Sportswear
There are specific difficulties associated with converting to digital disperse printing for ladies fashion.In the case of a digital dye sublimation printer for sportswear, a typical set-up involves printing and cutting panels of paper or printing complete rolls of paper. The dye sublimation process usually takes place in some kind of table setting or in a roll-to-roll setting. In the press the design is then transferred from paper to fabric. No washing is needed, so it’s a fairly straightforward process, with only a few parameters to determine.The pros of this process include: ease; no washing required; fast; cost-efficient; and level printing results. Cons include no through-print — the back of the fabric remains white; limited fastness with migration and pleating possible; loss of fabric texture because of high pressures and temperatures used during processing; and fabric yellowing may occur.The main problems these cons create when trying to convert to the ladies fashion market include: through-print, at least to a certain extent, is in many cases required because the ladies’ fashion market uses fairly thin fabrics; delicate fabrics, sometimes with some structure may get flattened/hardened in a calender, which are not desirable qualities; and fastness requirements may not be achieved with standard dye sublimation inks.
Digital Disperse Printer For Flags And Banners
In the case of a printer producing flags and banners, the most common setup would be a digital roll-to-roll printer using either dye sublimation inks or disperse direct inks. These direct inks have a colorless carrying medium, while traditional dye sublimation inks may have a light brownish carrying medium. Fixation is performed on calenders or a contact heat roller system. For certain end-uses, no washing process is required after fixation. For any product that is to be used outside, a washing procedure is performed to clear any unfixed colorants.A special capability in this scenario is the option of double sided printing. By printing directly onto a non-pretreated fabric in most cases, the inks will easily migrate to the backside of the fabric.This process is still a fairly easy process requiring little to no washing, and it offers two-sided printing possibilities. Drawbacks to this method include a chance of colors bleeding; fabrics require washing in order to be used outside; fabric stretching during fixation; and dull finished colors.Issues this type of producer can experience when trying to move to the fashion market include: needing pretreatment in order to prevent migration and/or bleeding and to maximize color depth; requiring reductive clearing to diminish all non-fixed dyestuff and those types of companies often have no washing equipment; and fabric finishing is needed to give the fabric the necessary properties.
The pretreatment, clearing and finishing steps all require large equipment — washing lines, padders and tenters — that typically only are available at large conventional printers.
Printed polyester fabrics have become a popular choice in the fashion world.
Digital Reactive Dye Printers
Manufacturers printing reactives using digital equipment operate digital-printing machinery that has a printing blanket, which stabilizes the fabric during printing. Such manufacturers commonly pretreat the fabrics themselves, and after printing they steam and wash the fabrics.Pros associated with this method of manufacturing include: high fastness; large color gamut; and the fabric is heated but it remains untouched, so normally fabric hand does not change too much. The biggest con associated with this method of manufacturing is that many parameters have to be monitored including pretreating, steaming and washing, which results in a difficult to manage process.When a reactive-dye printer wants to change to printing with direct disperse dyes, there are only a few things that change. Because of the changes in dye and fabric, there is a need for a different pretreatment process. Furthermore, the fixation process needs to be performed at roughly 175 °C instead of 102 °C.So what is holding manufacturers back from switching to using direct disperse dyes considering the market for digitally printed polyester fashion fabrics is increasing and therefore attractive? Manufacturers actually are not being held back, but unfortunately it’s not only the issue in play.As a supplier to the traditional reactive printing market, The Netherlands-based SPGPrints BV has seen many producers invest in digital dye sublimation equipment. Not because they wanted to, but because no real solution was available for direct printing onto polyester.As the market was demanding polyester, producers had to deliver but struggled because the inks for direct disperse digital printing were not reliable enough.So numerous textile printers added smaller-sized equipment to their production portfolio, and they started to print on paper and then perform the sublimation. Although this is easy and cheap, the quality isn’t what the market demands.On the supply side, things also have changed. In the early days of printing direct disperse on high-speed machines, it was obvious there were some problems including too much glycol in the inks; unstable dispersions; and open time at the nozzle.
The glycols create multiple issues during the printing process. They help elevate the viscosity of the inks, which is good for ink-jet print performance, but the elevated viscosity has a negative effect because less dyestuff can be dispersed in the inks causing less color yield.
Another negative effect of the glycols is during ink drying — the inks become different. The boiling point is higher than 130 °C, which causes a dryer that runs at a fairly standard 130 °C to not dry the fabric. This can cause staining or marking of the design on other parts of the fabric when it’s rolled.
The fact that not all inks are very stable dispersions can cause havoc. Most inks tend to dry slowly, but when they do dry, they dry almost like a pigment with binder. When this happens on the nozzle plate, the heads can easily become clogged. It is of utmost importance that dried ink in the printhead is avoided at all costs.
So making a reliable ink for direct printing polyester is therefore a challenging task. The initial ranges of disperse direct inks had a dramatic effect on lifetime of the Kyocera heads. This effect was improved, where the second generation of direct disperse inks had a much improved runnability and lifetime score, but all of them were lower on the available color gamut.
Current Status
After two years in development, SPGPrints has created the next generation of direct disperse inks that combine good runnability and lifetime scores with very bright and vivid colors, and that are also easy to dry. Fixation of the dyestuffs can be performed in traditional ways such as high-temperature steaming or hot-roller fixation. This therefore also opens up possibilities for companies that have been acting in the dye sublimation field.
Pretreatment of the fabric is necessary to maximize color gamut, but is limited to simply padding a recipe containing mainly thickeners onto the fabric. Washing also is necessary, as with all direct print methods to meet the requests of customers.
The latest Nebula Disperse Direct ink (for Kyocera) is available in eight colors — black, cyan, magenta, yellow, orange, red, blue and violet. The ink also is available as Flare type ink, for Epson DX4/DX5 heads. By having a large color gamut available in a direct print method, manufacturers can achieve the qualities that are needed by their customers.
Through-print is not an issue anymore on thinner fabrics. If needed, through-print is even possible on thicker fabrics by using SPGPrints patented penetration fluid. fastness of the direct method commonly outperforms fastness of dye sublimation.
Drying of the ink on the heads is prevented, due to the chemical build up of the inks.
All in all, there are no reasons anymore why the volume of digital printing of polyester fashion fabrics using true direct disperse inks cannot grow dramatically.
Editor’s note: Rene Wolferink is an application specialist on digital textiles with the Netherlands-based SPGPrints BV.
November/December 2015