T
he
technology for processing fibrous
batts on a needleloom to produce a fabric was invented by William Bywater of Leeds, England, more
than 100 years ago. A number of terms are used to describe fabrics the technology produces, and
these terms often are used interchangeably. They include “needlefelts,” “needled nonwovens,” “
needlepunch” or “needlepunched nonwovens.” “Needlefelts” and “needlepunched nonwovens” are used
interchangeably throughout
the industry.
Needlepunched nonwovens are produced by mechanically interlocking the fibers of a carded,
airlaid or spunbonded web using a needle-loom. Early needlelooms operated at relatively low speeds
of up to 100 strokes per minute. Jute, sisal and animal hair were the major fiber materials used in
the early needlefelts for carpet underlay and spring insulators for furniture and mattresses.
Needling requirements for making papermaker felts for the papermaking industry drove the need for
higher speeds and greater precision in needlelooms.
John Foster, vice president, Foster Needle Co. Inc., Manitowoc, Wis., has provided the
following description of the basic types of needlelooms:
The most commonly built needleloom in the world is the singledown punch machine. This basically
consists of one single needle board going across the entire length of the machine. The single board
machine does a good job needlepunching those products that do not require a high degree of
integrity of strength — such as paddings and waddings, carpet pads, etc. For more intense
needlepunching, the needleloom producers will add needle boards to their machines. This machine is
a double board up and down punch. In other words, the needleloom has four boards, two of the boards
needle from the top and two needle from the bottom. So for lower intensity needle-punching, single
board needle-looms are commonly used, and by adding more needle boards to the needlelooms, they are
better suited to produce products that require higher needle penetration levels. The degree of
needle penetrations is measured as needle penetrations per square inch (ppsi). Since ppsi is
related to throughput speeds, this variable is important.
PPSI plays an important role with such product characteristics as tensile strength, surface
characteristics, porosity and much more. Up to a certain point, [the higher the fabric’s ppsi, the
higher its strength]. Beyond this point, higher ppsi will lower fabric strength because of fiber
breakage.
Listed below is the general range of ppsi needed to produce various types of needlepunched
products:
• man-made leather substrates: 5,000 ppsi;
• geotextile — 4 ounces per square yard (oz/yd2): 1,500 ppsi;
• filter media — 12 oz/yd2: 1,200 ppsi;
• blankets — 10 oz/yd2: 800 ppsi; and
• carpet cushion — 30 oz/yd2: 200 ppsi.
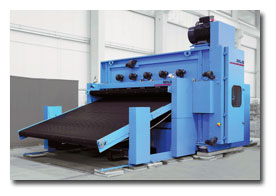
The elliptical needling process of the Dilo DI-LOOM HSC Hyperpunch provides increased
productivity and improved surface appearance, according to Dilo Systems Group.
Broadening Markets
The continuing growth of
needle-punched nonwovens has resulted from close cooperation of fabric producers with needleloom
and needle manufacturers and fiber producers. The three major producers of needlelooms — Dilo
Systems Group, Germany; Dr. Ernst Fehrer AG, Austria; and NSC Group, France — are all strong
competitors, and their competitive efforts have enabled needlepunch fabric producers to increase
productivity and boost quality levels. The needleloom producers have formed strong alliances not
only with their suppliers, but also with the suppliers of auxiliary equipment such as cards,
crosslappers and control systems.
In addition to the formation of alliances, there have been acquisitions such as the
Switzerland-based Saurer Group’s acquisition of Fehrer via its Neumag nonwovens machinery
subsidiary
(See “
Nonwovens/Technical Textiles News,”
TW, July/August 2005), which previously had acquired North Adams, Mass.-based
needleloom producer Morrison Berkshire’s intellectual property rights for the design and
manufacture of paper machine clothing web-forming, needling and finishing machinery; and
Switzerland-based Rieter Textile System’s recent cooperation agreement with NSC.

Recent developments for needleloom technology include refinements in structured needlelooms that
have enabled production of a wider range of rib and velour patterns including large repeat patterns
and borders at higher speeds. An example of this type of machine is Fehrer’s NL 11/Twin-SE
Carpet-Star.

higher productivity and improved surface appearance. This unit reduces drafting during the needling
process.
NSC’s development of the A.50-SDB
needleloom is designed to rib a heavy carpet product at speeds of up to 16 meters per minute, which
corresponds to 1,250 kilograms per hour.
Major suppliers of needles for needlelooms, such as Foster Needle and Groz-Beckert USA Inc.,
Fort Mill, S.C., are keeping pace with machinery developments. They are supplying needles that are
more resistant to breakage and have a longer wear life, as well as finer needles.
These developments enable structured needlepunch fabrics to be used in interior trim and
floor coverings for automotive, recreational and boating products. Needlefelts’ market share in
filtration is increasing. Improvements in control systems for needlepunching lines simplify product
changeovers and improve quality control.
The increase in productivity is resulting in overcapacity in larger commodity-type fabrics
for geotextiles, hospital/medical, furniture and apparel applications. Product development efforts
have accelerated to find more profitable niche specialty markets for needlepunch fabrics.
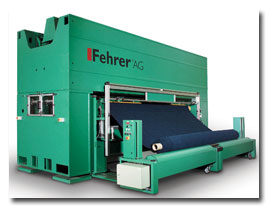
Dr. Ernst Fehrer AG’s NL 11/Twin-SE Carpet-Star is one example of structured needlelooms
that enable production of an increased range of rib and velour patterns.
Tex-Tech Industries
Portland, Maine-based Tex-Tech
Industries, a producer of a broad range of industrial woven and nonwoven fabrics, sells products
for the aircraft industry that include duct insulation, over-frame aircraft blankets,
flame-resistant sound insulation and thermal barriers.
“Needlefelts provide a simple process for controlled fiber orientation. [T]he felting
process mechanically moves fibers into the Z direction to ensure strength,” the company reports.
Needlefelt properties include:
• controlled fiber orientation in the machine or cross-machine direction, or at an
intermediate angle;
• Z-directional strength, which improves shear strength and reduces the potential for ply
delamination;
• high void volumes for easy absorption of resins;
• cost-effective thickness of composite structures by reducing the number of plies, weight,
lay-up times and overall costs;
• ease of blending diverse fibers and fiber structures such as high-strength and
thermoplastic fibers during the needlepunching process;
• distinct batt layering of two or more layers of distinct fiber types in one needlefelt,
and the ability to incorporate lightweight woven fabrics, films and other fabric forms into the
needlefelt structure; and
• compressibility for easy molding or shaping, which allows for intricate design.
Tex-Tech has used its experience in products for the commercial aviation industry to develop
fire-blocking products for school bus, railroad and racing car seating. Its patented fire-blocking
fabric is a nonwoven needlepunched fabric layer preferably saturated with a treatment as a means
for imparting water and stain repellency to the fabric. The surface treatment consists of a
fluoropolymer, such as Wilmington, Del.-based DuPont’s Zonyl™ or St. Paul, Minn.-based 3M’s
Scotchgard™. This treatment is applied using a conventional textile padding process, and is
subsequently dried and cured.
Precision Custom Coatings LLC
Totowa, N.J.-based Precision Custom
Coatings LLC (PCC) is unique in its backward integration into the needlepunched nonwovens business
from its base coating and lamination skills. PCC currently supplies a polyester-blend fabric used
as a sheath for the hoodliner of Cadillac cars. The fabric is embossed with the Cadillac emblem.
The company uses its coating skills to apply materials to the needlepunched fabric to provide the
necessary embossing and molding properties, as well as fire-retardant protection.
PCC also produces a hot-melt coated needlepunched fabric laminated to a spunlaced nonwoven
used in Princeton, N.J.-based Church & Dwight Co. Inc.’s Brillo Scrub ‘n’ Toss® scrubbing pads.
The scrubbing action of the pad results from the proper selection of a lower-melt fiber blend
component and the hot-melt coating.
Goodrich Corp.
After exiting the tire and chemical
businesses, Goodrich Corp., Charlotte, restructured. Its prime business became the fabrication of
components and the provision of services for the aviation industry including wheels, landing gears
and brakes.
The company’s patented process is used to form fibrous preform structures such as carbon or
graphite products suitable for subsequent processing into high-temperature-resistant composite
structures such as aircraft brake discs.
The process compensates for fiber pullback induced by fiber resilience, and for compaction
in previously needled layers induced during subsequent needle passes. The displaced fibers
generated by the needling process are referred to as Z-fibers because they are generally
perpendicular to the layers comprising a fibrous preform structure. Z-fiber distribution throughout
the thickness of the fibrous preform structure may be manipulated as necessary to achieve a desired
distribution. Z-fiber distribution throughout a brake disc can have a profound effect on disc wear
life and on performance of the brake disc in slowing or stopping an aircraft.
Bridgeman, Ritter And Montgomery
William A. Bridgeman, Eric D. Ritter
and Eliza L. Montgomery have developed a nonwoven, carbon-based weld blanket that protects
automobile exteriors and interiors and industrial equipment from weld spatter.
The blanket is made of a needlepunched webbing of pre-oxidized polyacrylonitrile fibers. The
fabric then is assembled using carbon precursor fibers that have been interlocked using a
needlepunch process to produce a nonwoven and non-plush fabric. The resulting weld blanket is
light-weight and effective at a cost-effective thickness and density.
In use, the weld blanket can be taped to automobile components or industrial equipment to
ensure the security and protection of equipment from molten spatter near welding locations.
November/December 2005