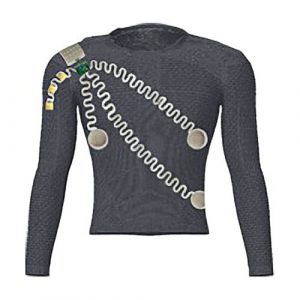
Technologies for effective and durable wearable electronics are advancing and show promise.
By Amanda Myers, Allison Bowles, Hasan Shahariar, Raj Bhakta and Jesse S. Jur
What if a shirt could sense the wearer’s vitals? What if the curtains in a home could sense lethal gas concentrations? These use-cases may seem futuristic, but they are some of the technologies under development right now in the field of textile electronics at North Carolina State University (NCSU), Raleigh, N.C. Adding this sort of electronic functionality to textiles adds value to the textile. The field of textile electronics has numerous applications within sensors, home textiles, internet-of-things and wearable textiles spaces. However, given that the textile industry operates on low-cost and high-scalability, technologies that allow integration of electronic functionality onto textiles must satisfy those two requirements. Researchers at the National Science Foundation Engineering Research Center on Advanced Self-powered Systems of Integrated Sensors and Technologies (ASSIST) and the Nano Extended Textiles (NEXT) research lab at NCSU’s College of Textiles seek to solve these problems.
Blending Electronics With Textiles
Integrating electronics and textiles together seamlessly requires two manufacturing procedures to be blended. Currently, electronics and textiles are manufactured via two very different and well-established production methods neither of which is suited for modifications from a different industry. A custom manufacturing strategy separate from traditional electronic and textile production methods is required for electronic, or smart garments, to be fabricated efficiently and cost effectively.
Cut-and-sew is the cheapest and most commonly used method of apparel manufacturing. It is labor intensive, but is the easiest way to scale-up production to manufacture large quantities of garments. Costs for this type of production can be reduced by sourcing lower-cost labor and cheaper raw materials, as well as by reducing the amount of sewing per garment. Each additional operation added to the production of the garment has a large impact on the cost of production. For example, a shirt with an embroidered design costs more to make than a plain shirt because embroidery is an extra step in the production process.
There are emerging technologies that have the potential to streamline the garment production process so that it would be easier to integrate e-textiles in a customizable way. For example, fully fashioned knitting technologies — such as WholeGarment™ from Japan-based Shima Seiki Mfg. Ltd. and knit and wear® from Germany-based H. Stoll AG & Co. KG — permit a complete garment to be knit in a single process on one machine so no additional finishing is required. This significantly cuts down on processing time, waste, as well as hands-on personnel time. Conductive yarns also can be knit into the garment in precise locations using the same process instead of being appliqued in an additional step, which adds to the cost of production. This process also reduces the amount of expensive yarn waste by using only the conductive yarn in the areas where it is required, such as in locations for sensors in interconnects. The possibilities for creating complex patterns or circuits during the design and programming stage of production using specific knit structuring are endless.
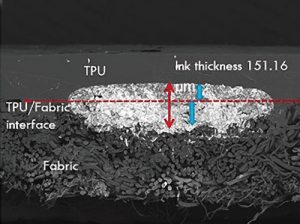
Conductive Yarns
Conductive yarns are a logical pathway to creating textile circuitry using these fully fashioned knitting processes. Biocompatible yarns featuring stainless-steel or silver can be used as the conductive components. Silver is the more conductive of the two materials, but stainless steel yields a cheaper yarn. Currently, the textile industry is trying to use the same spinning and knitting machinery that has been used for decades to make conductive yarns and fabrics, which limits the scalability of e-textiles. Yarns containing stainless-steel or silver can be difficult to run on traditional machinery because of friction and the abrasion of metal yarn on metal. Unlike typical textile materials like cotton or polyester, conductive materials are more rigid with less extensibility, which makes them difficult to bend and twist during textile processing. Machines must be run much slower than during traditional textile production processes in order to prevent yarn or fabric defects as well as machine damage. Efforts have been made to improve conductive yarn processing by blending conductive materials with non-conductive fibers; however, this generally leads to higher electrical resistance in the finished yarn. To create a functional circuit, the interconnects between electronic components need extremely low resistance — or high conductivity. Therefore, most conductive yarns currently available are not suitable for textile circuitry because of either high electrical resistance or difficulty during knitting and/or weaving.
Some manipulation of the final conductivity of a textile can be performed at the knit level by changing the stitch length or knit structure. A more dense knit structure will show a higher electrical conductivity because of increased interaction between the conductive yarns. However, the benefits gained from increased density are not enough to enable textile circuits. Instead, current conductive yarn technology is most suitable for electronic sensors or actuators that do not have the stringent conductivity requirements that circuit interconnects do.
Printing is another integration approach for bridging the electronics and textile industries. The electronics industry uses conductive inks to create components for printed circuit boards (PCBs). PCBs, along with sensors and actuators, are manufactured on thin films using various printing processes. While conductive inks traditionally are used for printing on films and papers, varying the viscosity of a conductive ink makes it possible to print on different substrates including textiles. Printing, regardless of the industry, can be an inexpensive, high-throughput process. The ability to print directly on textiles creates a pathway for integrating electronic devices, sensors and interconnects on textile substrates or pre-fabricated garments. This process is critical to the marriage of the electronics and textiles industries for future development of wearable technology.
Long-Term Durability
One of the biggest challenges of integrating textiles and electronics is the durability of the wearable device. Most electronic components are rigid and inflexible, whereas textiles can have a range of flexibility and stretchability based on the end use. Electronic components must be modified to withstand the repeated mechanical stresses induced by the textile. Currently, printed circuits on textiles lose conductivity and mechanical robustness after multiple uses or washes. The addition of a protective layer over the conductive ink can help preserve the integrity and performance of the textile circuit.
Researchers at NCSU investigated the robustness of textile circuits after laminating a polyurethane film over screen-printed conductive ink (See Figure 1). The thermoplastic film not only encapsulates the ink, protecting it from mechanical damage, but the film also exhibits a self-healing effect where microcracks in the conductive ink can be repaired as the textile returns to its unstrained state. The result is a sturdy circuit that can be ironed onto an existing textile substrate in any position, allowing for easy individual customization of each device. Other printing technologies, such as a direct-write process — widely used in the electronics industry — permit highly detailed conductive designs that cannot be achieved through screen printing processes (See Figure 2). In this way, wearable prototypes can be fabricated quickly and tested without the detailed manufacturing processes currently used.
NSCU students and researchers have an immediate goal to conduct human trials for a electrocardiogram sensing smart garment in conjunction with the ASSIST center, as well as continue interfacing with the standards organizations to develop the right standards for this burgeoning industry. The work in wearable technology occurring at ASSIST bodes well for the future of healthcare. Imagine a smart shirt that monitors vital signs daily and transmits the information to your doctor. The possibilities that textiles offer as a platform for wearable technology is promising, and the technology is now closer than ever before.
Editor’s note: Dr. Jesse S. Jur is an assistant professor in the Textile Engineering, Chemistry and Science department at NCSU’s College of Textiles. Amanda Myers, Allison Bowles, Hasan Shahariar and Raj Bhakta are members of Jur’s research group on Nano EXtended Textiles (NEXT).
March/April 2017