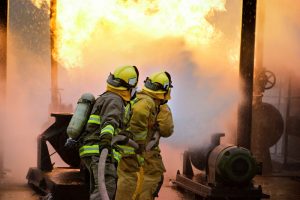
New materials increase part functionality, utility and product differentiation
By Joe Melcher, Patty Berghardt and Shawn Benfield, Bally Ribbon Mills
The advanced technical textile industry uses science, information technology, and specialized materials to provide material solutions to a broad range of niche markets. The industry distinguishes itself from the standard textile industry by its adoption of new ideas and processes to create materials to meet specific requirements. Used primarily for performance, structure, and strength, innovative advanced textiles can improve customer products at a competitive cost, while contributing superior properties.
Advanced textiles experiencing fast growth
According to the Industrial Fabrics Association International (IFAI), a trade association representing the international specialty fabrics marketplace, the overall growth for advanced textiles is estimated to be about 9 percent and is currently valued at $71 billion. The protective textiles contribution to this sector is 6 percent, while other important contributors include high performance clothing, composites, coated textiles, and smart textiles. [1]
A general trend is the use of high tech/specialty fibers with properties designed to bring added value and increased performance to the end use application. These typically include fabrics made with aramids and meta-aramids (Kevlar®, Nomex®), graphite, Vectran™, Teflon™, Dyneema® and Spectra®, as well as composites or other specialty fibers.
Bally Ribbon Mills (BRM) has found that customers are looking to use advanced textiles to differentiate themselves from their competitors. They want to make their product last longer, or make it lighter, or imbue it with other characteristics that give them an advantage. In the personal protection arena, advanced textiles are being used to make products stronger. For example, one BRM customer wanted to eliminate elongation in a belt used in a manufacturing process. By adding low elongation para-aramid and UHMWPE fibers to the existing substrate, the belt was able to maintain its integrity much longer and stay in service 10 times longer than the prior version.
The push in recent years has been toward fabrics that are lighter and stronger and let users do more with less. While advanced textiles can be found in a wide variety of applications, sectors that support quality of life would — or should — use the most advanced technical textiles. This may include medical applications, along with some industrial, and military — like parachutes. The properties they are looking for vary by industry. Some continue to seek out stronger and lighter fabrics, while the medical industry is looking for materials that are less invasive and promote faster healing.
It should be noted that other markets are also looking for innovation and advancements, even on products that have been on the market for decades. Just because an item has been used for a long time does not mean it cannot benefit from a design review. For example, BRM has done design work for dog collars to make them stronger. In advanced design, customers want to differentiate themselves from a million other companies making dog products (and baby products!) Another good example of the use of advanced fibers in long-established products is sun awnings, where manufacturers are developing new methods to weave fibers that wear better and can last 50 years instead of 10. Wherever manufacturers are seeking an edge, advanced textiles have a role to play.

Tips For Customers Looking For Advanced Or Technical Textiles For Unique Applications
Those looking for an advanced or technical textile should begin by discussing the application, the specific material properties they are looking for, the material specifications, and any special requirements, certifications, and testing requirements.
At BRM, we begin by advising customers of our capabilities and experience in weaving two-dimensional and three-dimensional designs and discussing the company’s quality management system and its effectiveness in meeting customer specific requirements. We request a sample from the customer if one is available, and then work with our R&D group to provide examples of materials we have already woven that can be tweaked to meet the customer’s requirements.
BRM gathers as much information as possible on the application, the location within the product that the material will be placed, and any properties the customer is specifically trying to address. Typical information gathered from customers includes:
- Application details;
- Width;
- Tensile strength;
- Elongation;
- Color;
- Quantity; and
- Special requirements including flammability, conductivity, moisture, and abrasion resistance.
Where the customer knows the application but is not familiar with textiles, BRM application experts help determine required properties and the most appropriate weave pattern. A back and forth approach is used to tweak products to improve existing designs that will help the team arrive at the optimal webbing. Then, manufacturing experts conduct small sample runs, which are tested in the BRM textile lab. For all materials, BRM tracks raw material testing. Customers then use the tested material to manufacture their products.
Fabrics may also have to meet a variety of safety standards/specifications and certifications, which include ISO9001, AS9100, ISO13485, ISO14000, NFPA, ASTM, ANSI, *UL, and CSA. BRM continuously monitors these standards and has established accurate and streamlined in-house systems to support required testing and tracking – from raw material to finished parts. Test reports and certifications are provided according to the particular specification or the customer’s requirements. Providing simple and timely documentation and test reports is critical, especially for lifesaving products like parachutes, where documentation is required so any errors can be followed back to the yarn manufacturer.
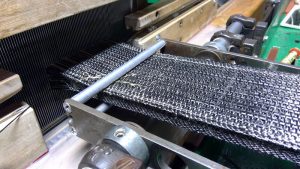
Unique Advanced/Technical Textiles
Working with companies that include NASA, Tier 1 Defense suppliers, as well as directly with the Department of Defense (Army, Air Force), BRM has developed advanced textiles used in parachutes, safety harnesses, personal protective equipment, and chemically resistant webbing. With a Class 8 Clean Room and multiple loom styles (shuttle, needle, jacquard, rapier), BRM can scale up from prototype to full-scale production.
E-WEBBINGS enable electronic transmission of data, sensations and power.
Examples of the newest advanced textiles include:
E-WEBBINGS®: Woven narrow-fabrics that are conductive, enabling the electronic transmission of data, sensations (light, noise, vibrations, heat), and power that can be stored or used to actuate/transform objects. These unique conductive fibers can be woven in conjunction with other fibers and can be used in embedded sensors in both wearable and integral technology, including the Internet of Things
One new project currently in development utilizes advanced conducting/sensing technology that is composed of a sophisticated weaving process to comingle fiber-optic filaments with high-performance, structural materials. Optical “carriers” are the structured output of the weaving process, which serve as component parts in the eventual construction of assemblies that can capture and transmit information to downstream computing technology. The optical technology can take corrective action based on improved monitoring capability and assist in the optimization of manufacturing processes and the integration of non-destructive inspection tools.
TPCM™ woven thermoplastic localized reinforcements: These thermoplastic composite materials are 2-D or 3D-woven, thermoplastic structures for incorporation into composite parts produced within varied, continually-evolving molding processes. The woven structural shapes are used in hybrid composite structures used in numerous industries, including aerospace/aviation, automotive/transportation, defense, architecture/infrastructure, marine, and sports/recreation.
TPCM fabrics are comprised of structural and matrix/resin fibers oriented to maximize X, Y and/or Z directional properties. They can produce lighter-weight, quality parts at reduced materials and labor costs, with reduced process complexity and bills of material. Potential fiber combinations include a varied mix of structural yarns (fiberglass, carbon, aramid) and matrix/resin yarns (such as PE, PA6, PEI, PPS and PEEK). TPCM in a customized and engineered weave design, provides localized reinforcement where superior properties are required.
TPCM fabrics are being advanced as part of a collaborative development effort in which BRM is teaming with suppliers and downstream fabricators. One partner is Concordia Fibers, Coventry, R.I., which supplies Comingled Yarns for the project. Its technology produces a better mix of structural and matrix yarns, which in turn improves the properties of the woven structures. Customers purchasing this type of fabric are working with expert knowledge provided by the complete supply chain, including the entire process and product development process. This is the most forward-looking way to work with suppliers to ensure product success.
TPCM fabrics can produce lighter-weight, quality parts at reduced materials and labor costs, with reduced process complexity and bills of material.
Benefits Of Advanced Textiles
Advanced textiles can increase a part’s functionality, utility and product differentiation, at a competitive net cost, while contributing superior properties such as lighter weight, specific strength, durability, stability, abrasion resistance, and sustainability. BRM’s unique ability to produce advanced technical textiles through innovation, experience, design, research, development, quality, technological advancements and customer service separates it from the competition.
Reference
[1] Growth meets change in protective textiles, Innovating and commercializing to participate in future opportunities, by Seshadri Ramkumar, Advanced Textiles Source, May 20th, 2019, https://advancedtextilessource.com/2019/05/20/growth-and-change-in-protective-textiles-innovating-and-commercializing-to-participate-in-future-opportunities/, retrieved 10/25/19.
Editor’s Note: Joe Melcher, Patty Berghardt and Shawn Benfield work in business development for Bally Ribbon Mills, Bally, Pa.
April 24, 2020