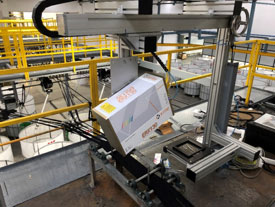
By Nicolas Seyfried
The term Denim is a contraction of “de Nîmes”, the city in France where Serge de Nîmes created the tissue made originally of a mixture of wool and silk. Since the beginning of the 19th Century, Denim is known as a strong fabric made of cotton. More than 50 percent of denim is actually produced in China, India, Turkey, Pakistan and Bangladesh1.
The denim yarn is made of cotton and dyed with synthetic indigo dyes. Indigo is one of the most famous and oldest dyes used for textile dyeing, originally extracted from plants. A pair of blue jean trousers requires 3 to 15 g of indigo.
To dye the yarn, it is necessary to dip the yarn in several consequential baths of dyes. In between, the yarn with the dye undergoes an oxidation process. The more dye baths, the deeper the color of the indigo2.
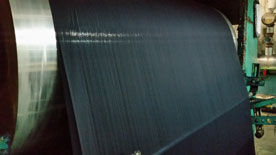
Meanwhile Denim is used to realize pants, skirts, shirts, vests and many more. The numbers of colors used in the production process are endless and it is almost impossible to distinguish the colors without the use of a color measuring instrument. Such instruments can be used to check the final color of the tissue but at that stage, it is almost too late, as the Denim will be ready to be transformed into clothing. The most efficient way is to measure the color during the production process. As soon as a color drift is “observed” with the color measuring instrument, a color correction can be induced.
Actually there are several places where color of denim can be measured during the production process. Depending of the dying machine, the color is measured for example directly on the rope of rope dying machines, which has proven to be very efficient. Naturally, the color can be measured on slasher dying machines as well. In this case, the yarns are dyed continuously, side by side and allow immediate reaction if color drifts away of specification.
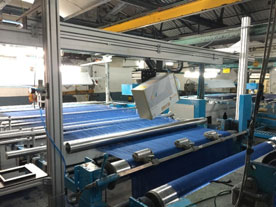
The color measuring systems have to measure contactless3. Moreover, they have to fulfill a series of unconditional and proven parameters for best results such as:
- The light source of the instrument has to be a flashed Xenon light because the visible spectrum of the Xe-light is similar to the visible spectrum of the sun light, flashed Xe-light to avoid any influence of parasite light.
- The optical resolution shall be as high as possible. With a resolution of 1 nm the obtained results have proven to be significant and useful.
- The instrument shall have no movable parts and be made to measure in harsh environmental production conditions. This is an important aspect, as the producers want reliable color measuring systems, operating 365 days per year without unplanned interruption
- The entire production and not just samples taken out of the production once every shift, has to be measured. Only if the color of the entire production is measured, a color drift can be detected and corrected. This will avoid producing waste; this will allow using the production machine to produce only sellable Denim in accordance with the customer’s specification. As a result, the production site will save considerably amounts.
- The measured color values shall be saved in a Data base, in order to document the complete productions. At any time it must be possible to retrieve past production data, to be able to compare various productions and if necessary prove the color is right.
- On a Slusher Machine, the Color measuring instrument shall be able to move in cross direction, either manually or motorized, to allow a precise positioning of the instrument wherever it shall measure. A visualization of the results shall be easily possible on a screen.
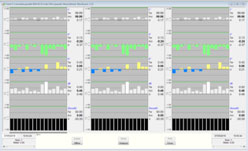
References:
1 Agarwal, Sandeep (13 October 2009). “World Denim Market – A Report on Capacities, Market Size, Forecasts etc”. com. Retrieved 25 August 2015
2 Bojer, Thomas Stege (16 December 2016). “How Denim Is Made: Indigo Dyeing”. Denimhunters. Retrieved 2 September2019
3 X-rite “Color Measuring System ERX130”, December 2019
Editor’s Note: Nicolas Seyfried is international sales manager for X-Rite GmbH
April 24, 2020