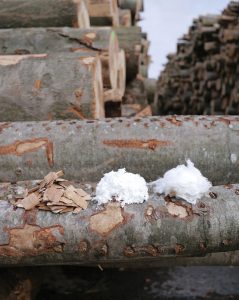
Closed loop systems and circular economies are two ways the fiber, yarn and fabric industries are tackling sustainability issues.
By Dr. Kavita Mathur
The fiber and yarn chapter was launched at ITMA 2011 in Barcelona in response to industry demands for a comprehensive, one-stop sourcing platform for textile and garment manufacturers. Since its addition to ITMA, this chapter has continued to grow. At ITMA 2015, the chapter included another subchapter on recycled fibers and yarns to support the industry’s commitment to sustainability. For ITMA 2019, the chapter was expanded to include an innovative fabrics section as well. The fiber, yarn and fabric chapter offered innovative and eco-friendly solutions with a focus on recycling, waste reduction and production efficiency at ITMA 2019.
According to a new report from Grand View Research, the global textile market was valued at $925.3 billion in 2018 and is projected to reach approximately $1.2 trillion by 2025 at a compound annual growth rate of 4.24 percent. Within this growth, the textile yarn market is estimated to be worth $12.6 billion by 2020 according to B2B research company MarketsandMarkets™. As the global textile industry continues to grow, it is generating greater demand for raw materials, novel applications and new production processes.
The fiber and yarn sector is an integral part of the textile and garment industries. To stay competitive, these industries are striving for continuous improvement and therefore are constantly looking for innovative solutions to meet the changing demands and industry standards. These standards are geared mainly towards sustainable solutions such as recycling, waste reduction, production efficiency and closed-loop production. With increasing involvement from governments, these standards now are becoming crucial for trade and businesses.
It is obvious that sustainability is a rising concern of brands, equipment and fabric manufacturers, and consumers. The industry is still very recycled-centric, which is clearly not enough. There has been a greater push for water savings, durability and waste management, as well as reduced emissions, water pollution, and carbon footprint. The yarns, fibers, and fabrics chapter at ITMA 2019 offered a very crucial component of the textile industry as more industrial and fashion companies look for innovative and sustainable materials.
Sustainable Solutions
Second to oil, the textile industry is one of the largest contributors to harmful environmental effects. According to the UN Partnership on Sustainable Fashion, it is responsible for approximately 10 percent of greenhouse gas emissions and 20 percent of wastewater production globally. As a result, the need for textile companies to alter their approach to manufacturing and production is drastically increasing. Across the board, companies are developing fibers and yarns as innovative solutions to address the need for more sustainable systems. There are two major sustainability initiatives exhibited by various companies — circular fashion and closed loop systems.
Circular Economy/Circular Fashion
Today’s current textile industry follows a linear economic structure with a very short lifespan — textiles are sourced, produced and ultimately thrown away. This economic structure, although fast, is very inefficient, unsustainable, and detrimental to the environment. Recently, the reuse economy has gained a lot of attention to tackle this situation. This platform improves the linear process by reusing textiles over and over again. However, this kind of cycle eventually ends when the item can no longer be repurposed or recycled and ultimately ends up in the landfill as it would in a linear economy. This type of economic structure is referred to as a circular economy or circular fashion, which not only addresses the ability to extend the life of a product, but also protects the environment at the same time. In a circular fashion industry, every aspect of the production process is pushed to be circular, ethical, and ultimately environmentally friendly and sustainable. This includes recycling materials, using biodegradable solutions, sourcing raw materials ethically, and using more efficient manufacturing and production processes.
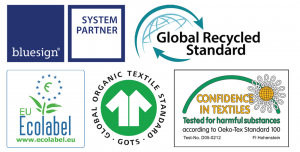
At ITMA 2019, companies emphasized their circular fashion initiatives by showcasing efficient manufacturing and production processes including reduced emissions, waste, water, chemicals and energy usage; and by finding ways to biodegrade post-consumer materials in order to fully close the loop. Various companies were able to ensure the credibility of their products through the use of eco-labels including the bluesign® standard, Global Organic Textile Standard (GOTS), the EU Ecolabel, STANDARD 100 by OEKO-TEX® and the Global Recycled Standard (GRS).
The bluesign standard provides a means of pre-testing and analyzing all components required to manufacture a product before those components go into production. By analyzing the environmental footprint of these components, it helps to eliminate sources of harmful environmental contamination from the very beginning. The GOTS certificate ensures that fibers going into production are organic, production is ethical both on an environmental and social level, and that the consumer will receive a responsibly made product. The EU Ecolabel is a label that identifies products that were made with the environment in mind for manufacturing processes, distribution methods and safe disposal capabilities. Standard 100 by Oeko-Tex is a certification system for all aspects of the manufacturing and production process, which helps safeguard the consumers’ and environmental health by ensuring that no harmful chemicals are utilized during the production process. The GRS label is provided to companies who utilize recycled content in their products, and certifies that the recycled material used is traceable, environmentally friendly, and labeled correctly.
Switzerland-based Archroma provides “safe, efficient, and enhanced” textile chemical solutions, according to the company. Its chemicals are bluesign approved, GOTS certified, biobased, perfluorinated chemical (PFC) free, formaldehyde free and metal free. By certifying its products with eco-labels and utilizing sustainable practices, Archroma is able to effectively protect the environment against harmful wastewater and also save valuable natural resources.
Switzerland-based Clariant International Ltd. demonstrated its sustainability initiatives by introducing dope-dyed yarns that use 98-percent less energy and 99.9-percent less water compared to package-dyed yarns. In addition, the Clariant introduced new functional additive masterbatches such including fluorine-free hydrophobic and anti-soil masterbatches for polyester; chain extender masterbatches to help recycle polyester; and soft touch masterbatches for polypropylene, polyester, nylon and polylactic acid fibers, filaments and nonwovens.
Italy-based DBT Fibre promoted sustainability in its long and short staple spinning processes with the aim of optimizing the environmental and social impact through its sustainable business model in a circular economy. As part of its Eco Fiber Green Action Solutions, the company installed a photovoltaic system with a capacity of more than 650 kiloWatts, which generates savings in carbon dioxide (CO2) emissions equivalent to 390 tons per year. In addition, its geothermal plant replaced the use of fuels and therefore eliminated any type of emissions into the atmosphere. DBT also has a system to recover waste materials from its manufacturing processes and recycle 100 percent of all packaging materials.
In response to the need for environmental awareness, Spain-based Nylstar S.L. showcased its NATEO Sustainability Program — which is focused on zero water pollution, water-savings and recycling initiatives — for its Meryl® nylon brand. Meryl NATEO nylon yarns offer an eco-friendly alternative to cotton and address recycling options.
Meryl EcoDye yarns are dyed using a dope-dyeing method in which the color is added to the polymer dope before extrusion. This method provides excellent color fastness and color take-up while eliminating the need for water during the dyeing process, according to the company. Meryl Cotton 66 is a yarn that was made in response to the environmental damage done by the cotton farming industry. This yarn looks and feels like cotton and eliminates the need for large amounts of water and agricultural chemicals that are required for cotton farming. Meryl Eco Denim is a technology that eliminates up to 11,000 liters of water per pair of jeans made. Nylstar also offers Meryl Skinlife, a silver ion-based antimicrobial treatment that eliminates odors while maintaining a balanced environment for the skin and therefore does not require the fabrics to be laundered as frequently. In its zero water pollution program, Nylstar also has developed variety of performance yarns that do not incorporate any topical chemical treatments under the Meryl Touch brand.
Spain-based Antex’s YNVIRON™ recycled dyed yarn solution, significantly reduces harmful greenhouse gas emissions, saves energy, reduces water consumption, and conserves natural resources, according to the company. The fiber, made using a blend of post-industrial and post-consumer waste, is colored using a dope dying solution.
Beaulieu International Group, Belgium, introduced its UltraBond staple fiber that doesn’t require latex or other binders when used in nonwoven applications. This product allows for a significant decrease in water consumption which results in a 93-percent reduction in energy use, and reduces CO2 emissions by more than 35 percent without the addition of any other agent.
Austria-based Lenzing AG, a producer of environmentally friendly wood-pulp-based fibers, showcased EcoVero™ fibers at ITMA. According to the company, the production of EcoVero fibers “generates up to 50-percent lower emissions and water impact compared to generic viscose.” Tencel™ x Refibra™ is another new product that is a combination of cotton textile scraps and wood pulp made using Lenzing’s efficient closed-loop manufacturing process. This product is 100-percent bio-derived, compostable and biodegradable, and results in overall 95 percent reduction in water used, according to Lenzing.
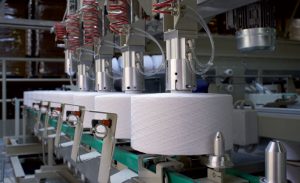
Spain-based S.Vilarrasa S.A., a manufacturer of open-end spun yarns, introduced a recycled cotton yarn that was produced using pre-consumer cotton garment waste. This replaces virgin cotton which reduces water use, agricultural chemicals and garment dyes. Vilarassa’s recycled cotton yarn results in a reduction of 4,800 kilograms (kg) of water, 16.5 kg of chemicals, 233.8 kg of CO2 emissions, 3500 kg of water contamination, and 500 kiloWatt hours of energy. The company has the GTS certificate that ensures its recycled material is verified.
Closed Loop Production
Based on the most recent statistics provided by the U.S. Environmental Protection Agency (EPA), there were 16.9 million tons of textiles generated in 2017 in the United States. From this, 11.2 million tons of textile waste was landfilled, and only 2.6 tons were recycled. This waste not only impacts the environmental condition on land, but it also contributes significantly to man-made waste polluting the oceans. Every year, more than 8 million metric tons of plastic waste enters the ocean.
Several ITMA 2019 exhibitors in the fibers, yarns and fabrics chapter addressed a closed loop production system through recycling and waste reduction means.
First established at ITMA 2015, the Sustainable Innovation Award aims to encourage companies to address textile sustainability by coming up with innovative solutions. The 2019 award went to Italy-based denim company Candiani S.p.A.’s for its Re-Gen, a “circular denim” fabric created using regenerated and recycled raw materials. The fabric is comprised of 50-percent Tencel x Refibra lyocell and 50-percent post-industrial recycled cotton waste from Candiani’s own operation. The chemicals and dyes used also are environmentally friendly, according to Candiani. Additionally, Refibra incorporates fiber identification technology, creating transparency in the supply chain.
Seaqual™, a fiber from Spain-based Textil Santanderina S.A., stands out it its mission to reduce the amount of waste currently in the ocean and to reduce more waste from entering the ocean. Seaqual is a 100-percent recycled marine plastic fiber, and the company partners with local fishermen to help collect the waste to produce the fiber. Textil Santanderina reports that for every kg of Seaqual fiber created, it removes 1 kg of trash from the ocean.
Some of Nylstar’s Meryl fibers also are created with waterways and the ocean in mind. The NATEO program ensures that high tenacity Meryl fibers do not deposit microplastics in the environment. In addition, Nylstar’s recycling program offers two products — Meryl Recycled fibers, which reuse post-production waste to create a new raw material; and Meryl Pure, which is designed to be 100-percent recyclable by using natural stretch instead of elastane for stretch in garments.
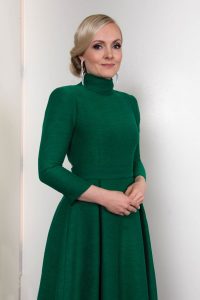
Finland-based Infinited Fiber Co. displayed an innovative recycling solution at ITMA not only for pre- and post-consumer textile waste, but also for cardboard scraps and agricultural waste. Its waste material is separated, turned into a liquid and then spun into a high-performance fiber. This system allows the company to reduce its water usage by 20,000 liters per kg of cotton and greatly lowers CO2 emissions.
As previously mentioned, Antex’s YNVIRON product aims to reduce energy consumption and environmental impacts through recycling post-industrial and post-consumer waste. The waste that is collected is shredded, melted, and extruded before being turned into a chip for future processing.
Eco-Friendly knitted fabrics from Haksa Tekstil San Tic A.S., Turkey, feature yarns that utilize recycled raw materials from pre-production textile waste to create a product that in turn saves billions of liters of water, saves thousands of tons of cotton fiber, and reduces thousands of tons worth of chemical contamination entering the environment, according to the company. The waste used can be combinations of cotton, polyester, Unifi’s Repreve®, acrylic or wool.
In addition to its EcoVero, Tencel and Refibra fibers, Lenzing offers Veocel™, a combination of cotton scraps and wood pulp for nonwoven purposes. Veocel fibers feature EcoDisperse technology, which allows nonwoven moist toilet tissues to disintegrate and biodegrade after flushing. Lenzing’s Veocel fibers produced using EcoColor technology are dope-dyed with color pigments to deeply embed the color while using water and energy only sparingly throughout the production process to reduce the environmental impact.
To ensure that all waste is utilized in its production processes, Lenzing utilizes a biorefinery to repurpose any leftover wood materials. This include biobased acetic acid, furfural, magnesium lignosulfonate, soda ash, sodium sulphate and xylose. These biobased coproducts may be used in the food, animal food, pharmaceutical, cosmetic, chemical, and textile industry for various applications.
Germany-based Kelheim Fibres GmbH introduced specialty viscose fibers that are made using 100-percent cellulose. This allows the fibers to be completely biodegradable. Kelheim works with CanopyStyle to ensure it does not source wood from ancient or endangered forests.
Another trend seen in this ITMA 2019 chapter, was alternative ways of making biodegradable alternatives to man-made materials currently used in the textile market. Taiwan-based Nan Ya Plastics Corp. displayed its GREEN ONE biodegradable polyester filament. Testing has shown Green One biodegrades in landfills into CO2, methane, and soil matter in approximately 98 days. This material can be combined with Nan Ya’s recycled polyester, heavy metal-free polyester and biopolyester.
Man-made fiber technology manufacturer Oerlikon, Switzerland, introduced a new fiber production method to fully recycle partially oriented and fully-drawn filaments via a process of homogenization drying, extrusion, pre-filtration, a vacuum filter from BB Engineering, and pelletizing and downstream melt application. Its process allows for all spinning waste to be directed back into production.
Beaulieu also displayed range of fibers, yarns and technical textiles that can replicate any type of staple fiber spinning technology using different type of polymers and additives with a variety of cross sections. These HT8 high-tenacity staple fibers offer unique high tensile strengths without compromising on elongation.
The Woolmark Company, Australia, showcased its cradle to cradle initiative that evaluated the impact its products have on the environment in order to ensure they contribute to a sustainable and circular economic structure. To measure the sustainability of the products, cradle to cradle assesses the materials’ health, reuse capabilities, renewable energy, carbon emission contribution, water usage and social impact. Woolmark works with parent company Australian Wool Innovation Ltd. to research, develop, certify, educate the community, and provide quality wool products for the textile industry. Since wool is an inherently sustainable natural fiber that is 100-percent biodegradable, it doesn’t negatively impact the environment. Woolmark is an advocate for conducting life cycle assessments to assess a product’s environmental impact from the beginning of its life to the end. This includes how the material was sourced, the manufacturing process, the products use and disposal of the product.
The Textile Industry Versus The Environment
The textile industry is a contributor to harmful environmental effects and waste generation in the eco-system. As a result, the necessity for textile companies to alter their approach to manufacturing and production is drastically increasing. ITMA 2019 provided an integrated platform of eco-friendly solutions including recycling, waste reduction, and pollution reduction and prevention. This theme was evident across the board as companies showcased a range of their fibers, yarns and fabrics to address sustainability issues.
Editor’s Note: Dr. Kavita Mathur is associate professor, Textile and Apparel, Technology and Management, at NC State’s Wilson College of Textiles, Raleigh, N.C.
May/June 2020