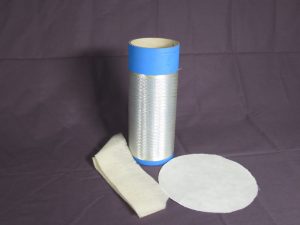
TW Special Report
When mentioning chitin, many people first think of insects or crustaceans. However, the sugar, which is widely used in animal shells in nature, could soon be used in medicine, for example in wound dressing materials. This can be realized by a new method developed by researchers at the German Institutes of Textile and Fiber Research (DITF).
Whether crab or beetle: the carapace of many insects and crustaceans consists mainly of the polysaccharide chitin, which makes their shells and wings flexible. Although chitin is abundant and inexpensive in nature, it has so far played any role as a renewable raw material for the textile industry. This is about to change. Researchers at the German Institutes of Textile and Fiber Research (DITF) have developed an innovative method that enables the excellent combination of chitin as a biopolymer with naturally occurring cellulose. The chitin is extracted from crab shells, of which there is more than enough. “We first remove the proteins and minerals from the crustacean before we produce fibers from them,” explains scientist Dr. Antje Ota, who is a researcher at the DITF’s Biopolymer Materials Competence Centre and is a major contributor to the project.
Novel Combination Of Cellulose And Chitin
The production process of the new fiber is based on the application of ionic liquids. They prepare the sparingly soluble chitin in an environmentally friendly way for bonding with cellulose. “We have chosen our ionic liquid solvent in that way that it is equally suitable for processing of cellulose and chitin. For the first time, it is possible to process these raw materials into fibers in a single process step,” explained DITF scientist Ota.
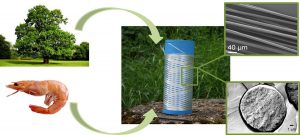
Speed Up The Healing Process
Ionic liquids (ILs) are salts that are already liquid at temperatures below 100 degrees centigrade and can dissolve many polymers, including the long-chain polysaccharides of chitin. In the DITF process, the chitin content of the biodegradable fibers reached up to 50 percent. A further advantage: the water retention capacity increased by 20 to 60 percent compared to pure cellulose fibers. “We expect the completely novel cellulose-chitin blended fiber to have great economic potential, e.g. for wound dressings in medicine that accelerate the healing process,” Ota said. The high air permeability of the new nonwoven is one of the main reasons for this.
The environment also benefits from the new production processes. The environmentally friendly production of the fibers is carried out without additives, and the solvent is almost completely recovered. Not only for the raw material itself, but also for its processing, the DITF researchers are thus orienting themselves towards the circular economy.
After cellulose, chitin is the second most common biopolymer worldwide. In contrast to bioplastics made from agricultural plants, this means that questions of raw material competition do not arise for the time being — unless other industries also acquire a taste for crab shells, for which the DITF have found a high-quality potential use in medical applications.
The DITF’s chitin research was funded by the Federal Ministry of Economics and Energy and the Ministry of Economics, Labour and Housing in Baden-Württemberg.
As part of the Zuse community, a well-known German research-community, the DITF also carries out practical research. The Cellulose Chitin Project is an example of application-oriented research that supports Germany as an industrial location.
June 25, 2020