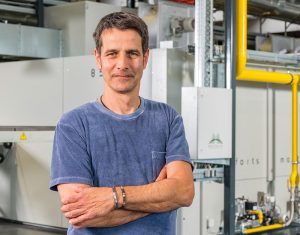
MÖNCHENGLADBACH, Germany — July 27, 2020 — Following the successful commissioning of two new Monforts Montex wide-width tenter lines and additional environmental management equipment at its plant in Germany, GtA — Society for Textile Equipment GmbH — is aiming to be the first textile finishing company to become entirely carbon dioxide (CO2)-neutral in the manufacture of all of its products by 2025.
GtA is a partner company to Germany’s large-format digital printing fabric leader, Georg and Otto Friedrich GmbH, which has has this year been able to considerably expand its portfolio with the new Monforts lines.
Headquartered in Gross-Zimmern, close to Frankfurt, Georg and Otto Friedrich GmbH and its partners in Germany have an annual production of 37 million square meters of warp knits for a range of end-use applications, including garments, automotive interiors and technical textiles, but increasingly with a concentration on digital printing substrates.
Fault-free textiles
A new standard in pure white, 100-percent clean and fault-free textile substrates has been demanded by this market in recent years due to the rapid growth in digitally-printed banners and billboards — often referred to as ‘soft signage’.
The substrates of choice for digital printing are 100-percent polyester warp knits which are resilient and allow excellent take-up of inks, and vibrant colors and clear and precise images to be achieved with digital printing techniques. The knitted construction also has the advantage of elasticity, which is a plus in terms of flexibility for installers.
Critically, the warp knitted fabrics have extremely smooth surfaces which is becoming increasingly important due to the general move away from PVC coatings which were the standard in the past.
It was to finish these fabrics for Georg and Otto Friedrich GmbH as well as providing such services for many other customers, that the GtA plant in Neresheim, Baden-Württemberg, was established in 2015.
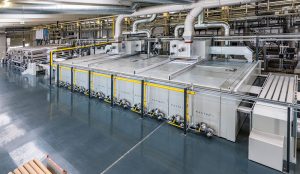
The purpose-built plant on a greenfield site was initially equipped with a fully-automated, 72-meter-long Monforts installation comprising a washing machine integrated with a 3.6-meter-wide, seven-chamber Montex tenter. The line quickly went from single to double shift production and then to 24/7 operation to meet demand.
Expanded widths
Building on the success of this installation, GtA has now installed two more Montex tenter lines — both in expanded working widths of 5.6 meters and purpose-built at Montex GmbH in Austria.
A six-chamber Montex unit is combined with a washing machine to guarantee the purity of the substrates, while a five-chamber line is integrated with a wide-width coating machine. This new coating capability at GtA has led to a number of new additions to the Georg and Otto Friedrich DecoTex range for digital printing, including wide width fabrics with flame retardant, antimicrobial and non-slip finishes.
The new Montex tenter lines benefit from all of the latest innovations from Monforts, including the Smart Sensor system for the optimized maintenance planning of key mechanical wear components on the tenters. A comprehensive overview of the condition of all parts at any time is now available for operators within the highly intuitive Qualitex visualization software.
With Qualitex, all article-specific settings can be stored and the formulations for thousands of treatment processes called up again at any time. Individual operators can also personalize their dashboards with the most important machine functions and process parameters.
Environmental commitment
GtA is run by a seasoned team of textile professionals led by Managing Director Andreas Niess.
“We have received excellent service from Monforts from the outset and we were happy to place the order for these two new lines as part of our ongoing cooperation,” he said. “With all of the latest Monforts advances in technology we are fully in control of all production and quality parameters with these lines, as part of our significant commitment to innovative environmental technology.”
The GtA plant, which operates in near-cleanroom conditions, has also been equipped with proprietary technology to fully exploit the Monforts air-to-air heat recovery systems that are now standard with Montex tenters.
“Around 30 per cent of our investment volume at the site goes to energy-saving measures and we are sure that this commitment is worthwhile,” Niess said. “As an example, our integrated heat recovery system fully exploits the waste heat from the process exhaust air and the burner exhaust gases of the Monforts tenters, allowing us to achieve an exhaust air temperature of between 30 to 34°C, compared to what would conventionally be between 140 to 160°C. Another focus has been on exhaust air purification technology and here too, the latest technology has been installed with integrated heat recovery elements.”
This, he adds, saves 52% of the energy that would normally be used — equating to 5,800,000 KwH per year. The necessary audits for energy-efficient companies are also carried out annually.
In addition, GtA has purpose-designed the automatic chemical mixing and dosing systems that feed the padders for the key treatments that are carried out on the fabrics through the tenters.
The company is going further, however, in its pursuit of clean production and raw materials.
“We want to be an asset and not a burden on our immediate environment and therefore do not use any additives containing solvents,” Niess said. “We were the first to use fully halogen-free flame retardant chemistry, and we use bio-based, finely ground alumina products for the washing process instead of surfactants. PES polyester yarns made from recycled material are also increasingly used and the latest additions to our raw materials portfolio, the RC-Ocean products, are made from recycled sea plastic.
“We are now planning a combined heat and power plant for the production of electrical energy and heat and we will also build a photovoltaic system that converts solar radiation into electrical energy. GtA wants to be the first textile finishing company to be CO2-neutral in the manufacture of all of its products by 2025. The complete heat supply and heating for the 13,000 square meter production hall, as well as the office building and the hot water supply for the domestic water, is already energy-neutral. We are convinced that this commitment will pay off in the long term and our positive business development proves that sustainability and business profitability are perfectly compatible.”
In addition to the products for Georg and Otto Friedrich GmbH, GtA offers its manufacturing capacities for other customers as a contract service.
All products are manufactured in accordance with Öko-Tex Standard 100, product class 1 and the company is also involved in the research and development of new sustainable manufacturing processes, in cooperation with many regional universities and funding project partners.
Posted July 27, 2020
Source: A. Monforts Textilmaschinen GmbH & Co. KG