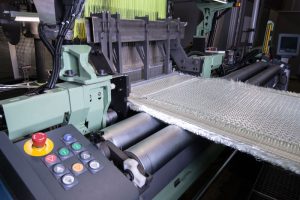
DORNIER is in the midst of re-introducing its Composite Systems® family of technologies focused on the ever-advancing needs of a dynamic composites industry.
By Jim Kaufmann, Contributing Editor
A composite, as discussed in previous issues of Textile World (see “Focus on Performance” TW, May/June 2015), is commonly defined as “the result of two or more distinct components, usually one being fibrous in nature, that when combined behave as one.” Woven 2D and 3D fabrics made from fiberglass, carbon, aramids, or some more exotic combination of fibers generally make up the fibrous component in a large percentage of these composite applications.
Founded in 1950, Germany-based Lindauer DORNIER GmbH is a well-respected manufacturer of weaving and advanced technologies for textiles and other industries. Early on, the company recognized and continues to pursue the opportunities created by the still evolving composites sector with its rather diverse applications and often unique needs specific to fabric forming technologies.
“Our aim is to supply machines and plants for the flexible and economical production of high-quality semi-finished composite products where our skills in textile and plastics technology complement each other perfectly,” said Josef Klingele, head of Dornier’s Composite Systems® Product Line. “The result of this cross-departmental cooperation is Dornier Composite Systems.”
In 2014, Dornier first introduced its Composite Systems suite of products, which was comprised of production technologies for composite intermediates. The suite addressed the extremes required of wide-ranging composite applications, as well as offering a more traditional weaving machine specifically for roving inputs to service the bulk of fibrous reinforcement needs. Given the composite industry’s ongoing evolution, technological advances and broadening spectrum of products, Dornier has continued to make improvements and additions to its system and now is effectively re-introducing the suite to existing and perspective customers.
Under the Composite Systems umbrella, Dornier now offers the fully impregnated or dry tapes and tape weaving production system PROTOS® TP and TW — Polymer and Roving to Sheet. The system encompasses a spread tow fiber tape manufacturing line for thin unidirectional fibrous tapes up to a maximum width of 23.65-inches, or 600-millimeters (mm)-wide. The PROTOS line also includes an improved tape weaving machine to address one end of the composite spectrum.
At the other end of this spectrum is the fully integrated 3D fabric production weaving system TRITOS® PP — Textile Roving into Three-dimensionally Oriented Structure — which is capable of producing complex fully integrated woven structures of up to 4 inches — or 100 mm — and possibly greater, in thickness.
Then, somewhere in between is the P2 Roving Weaving Machine, designed specifically for high-quality reinforcing 2D fabrics (see “3D Textiles: The Difference is Depth” TW, July/August 2016). These 2D fabrics are primarily made using carbon, glass, ceramic and/or aramid technical rovings, and are used in the broader spectrum of composite fabric applications.
“We purposefully tried to exclude the word ‘textile’ and even ‘fabric’ from any of the naming and promotional materials associated with either the TRITOS or PROTOS technologies because potential customers could be misled by the terminology” stated Peter D. Dornier, chairman of the board for Lindauer Dornier GmbH. “Products produced using this equipment are intended primarily for technical, structural and composite applications, not those of the traditional textile markets.”
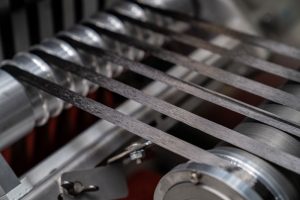
PROTOS® TP and TW
Dornier’s product offerings have included film stretching lines for the packaging industry since the mid-1960s, and spread tow unidirectional fibrous tape (tape) formation was a natural extension of this technology. Spread unidirectional tapes represent a relatively new technology that continues to gain acceptance in composite applications where lightweight, thin, flat, smooth, and consistent unidirectional layers exhibiting a high fiber volume — the ratio of fibrous material weight to that of the composite — are advantageous. Generally, fiber volume fractions for composites fall in the 45- to 60-percent range depending on the combination of fibrous materials, matrix used and product application. Higher fiber volumes in excess of 60 percent are found to contribute to higher strength and stiffness properties in composite products; attributes largely desired in numerous applications where specific high-performance levels are required.
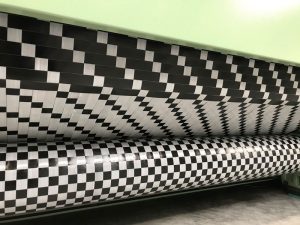
PROTOS TP, Dornier’s spread tow fibrous tape production line, is a stand-alone system engineered to effectively take large bundles of fibers or tows — 12K, 24K or 48K carbon for example — and effectively spread the individual fibers out across the width to a thickness of just a few fiber diameters while remaining unidirectional. The newly spread tow tape formation is then secured through an in-line application of a matrix material, or it can be completely impregnated by using a thermoplastic resin system or other binder. Thermoplastic resin systems continue to gain in favor for numerous composite applications because of their faster processing times, improved scalability, room temperature storage and inherent ability to be reflowed or remolded. Thermoplastic resin systems also present a greater potential for a high degree of recyclability because of their chemical composition when compared to existing thermoset resin systems.
Dornier’s tape line is designed to be modular, improving its functionality and flexibility in processing and materials used capabilities. Fiber tows of carbon, glass, aramids, and other polymers can be used alone or potentially in combinations along with matrix systems to produce the tapes.
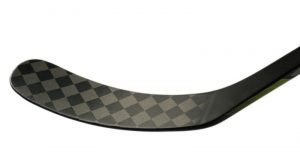
“A variety of thermoplastic polymers as well as fiber types can be processed allowing customers the opportunity to generate customized tapes specific to the application’s needs,” Klingele noted. “Also, because we use melt impregnation technology, granulate material can be used. There is no need for small particle suspensions, organic solvents or films.”
The resultant tapes are then slit or cut to their pre-determined width and wound onto flanged bobbins for subsequent processing.
Given the advancements in technology, today’s spread tow tapes can theoretically be as thin as one fiber diameter in thickness, but realistically will be several fiber diameters thick or more. The thinness and flexibility of these tapes present the composites engineer with new options and alternatives when considering various fiber placement methodologies and tape woven fabric configurations.
PROTOS TW, Dornier’s newly improved tape weaving machine sold separately from the fibrous tape production line, is designed to produce woven fabrics from either binder-fixed or fully impregnated tapes. It is also capable of using ribbon materials, for example slit films, or other tape like configurations of up to 1 inch, or 25 mm, wide in both warp and weft directions as well, separately or in some combination.
“The latest generation features high speed production of approximately 100 rpm for tape weaving and a fabric width of up to 112 inches or 2,870 mm,” Klingele stated. “The machine layout is drastically reduced and incorporates an integrated thermal fixation system with programmable fixation patterning to improve subsequent handling of the tape fabrics. PROTOS TW features an electronic dobby system to freely program weave patterns, coupled with rotating weft scissors to process a wide variety of tapes and rovings, two color zero twist feeder with uninterrupted weaving at color change and a tape creel for easy set-up.”
“Tape weaving effectively combines the advantages of unidirectional fibrous structures and fabric configurations,” Klingele continued. “This produces a woven fabric, or ‘textile structure’ if you prefer, with more consistent areal weights [weight of fiber per unit area (width x length) of tape or fabric] throughout, fewer interstices and virtually no crimp while exhibiting a much lower cross-sectional profile.”
Not only does reduced fiber crimping help to create a thinner and flatter fabric profile, but because the fibers are now straight and in plane, there is an immediate response delivered to any forces applied to the composite part because the fibers do not have to first overcome crimp in order to respond to the stresses and strains being presented. When molded into a composite part, the results demonstrate increased structural performance and reduced resin pooling areas leading to a higher fiber volume fraction — ratio of fiber to resin — in the composite structure when compared to fabrics woven using traditional yarn or roving inputs. Of note, since resin systems make up a large portion of the composite’s cost, any reduction of resin pooling and overall resin usage can lead to notable cost savings. In addition, the flatter fabric profile and reduction in resin pooling areas lead to greatly improved Class A surface finish characteristics, which are highly desirable in many high-performance composite end-uses.
Applications for spread tow and tape weaving technologies continue to grow as the technology improves and fiber reinforced composites in general gain increased acceptance in the various markets. Advantages derived from the PROTOS technologies include in the thin and flat fabric layers; reduced or limited interstices; and consistent, repeatable unidirectional performance from non-crimping textile structures. Composite products made using this technology may provide reduced weight and increased structural performance, improved surface finishes, reduced resin pooling and noticeably higher fiber volumes.
Given that many high-performance fibers are fragile and can break during processing, an additional reduction in production costs can be realized with PROTOS because of the reduced filamentation or broken fibers typically experienced during weaving and subsequent handling of traditional woven fabrics. In these tape fabrics, all filaments are fully encapsulated within the matrix material and are thus, protected. With the thermoplastic resin system already incorporated into the fibrous tapes, resin application is significantly reduced during infusion and molding times are improved — all beneficial in composite applications.
Interest in spread tow technologies is driven by the significant weight reduction or weight savings, and improved structural properties realized by the comparatively thin, flat, and high fiber volume characteristics of these textile structures compared to other materials.
Numerous applications for spread tow and fabrics made from spread tow are either already in production or under investigation. At a minimum, current applications comprise of automotive, marine, and racing/performance parts, battery separators, wind turbine blade concepts, advanced computer components, fire blocking layers, as well as numerous aerospace activities including drones and advanced satellite dish configurations.
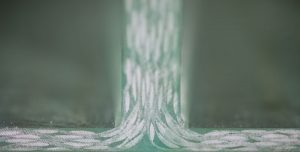
TRITOS® PP
Dornier’s TRITOS PP 3D weaving system is focused squarely on the opposite end of the composite spectrum where depth and fully integrated complex 3D woven structures are preferred. Three-dimensional weaving machines, typically paired with one or more jacquard heads, provide composite designers and engineers with a viable methodology for manufacturing woven billets and near net shape preforms that are stable and uniform. The technology incorporates traditional or modified warp- and weft-insertion systems that, along with the jacquard’s patterning capabilities, create precise fiber placement and strand paths through the thickness resulting in a cohesive textile structure.
In the past, these 3D weaving machines have either been created from highly modified traditional 2D weaving machines or designed and created as purpose-built one-offs. The TRITOS PP is one of the first 3D weaving machines to be offered by an established textile machine manufacturer. It is simple, yet complex, in its ability to weave 3D textile structures. Dornier takes the basic rapier weaving process and fortifies it with flexible shed geometry and a rigid rapier motion providing low filamentation with limited guiding elements. Weft or filling waste is greatly reduced using Dornier’s Weft Saver system, which improves production economics. Digital weave pattern programming coupled with the jacquard’s capabilities, creates the complex shed formations required for these intricate woven structures. For thicker fabric structures, Dornier also offers a horizontal take-up system as well as an integrated fabric guide. Additional add-ons and machine customization specific to width and unique applications also available.
Applications for 3D woven structures remain largely focused on areas where consistent, reliable, and repeatable component performance is critical to the product’s intended use. Situations where weight reduction, typically when compared to the incumbent products, likely produced from metals, and the ability to dictate orientated fiber placement to mitigate weak or high stress areas, enhance flexibility and/or provide foundational support are beneficial and potential delamination of the composite structure is a high concern. A growing concern associated with crack propagation in metal components also gives composite structures an advantage over comparable metal components. To date, crack propagation has not been identified as a concern in composite parts because of the integrated fibrous reinforcement structure and nature of the woven fabric yarn systems to bunch up as directional force is being applied.
Probably the most visible current application for 3D fabrics is the aerodynamically efficient 3D woven fan blade configurations incorporated into the LEAP jet engine systems produced by Cincinnati-based CFM International. These composite blades, complex 3D woven and shaped structures with fully integrated fiber orientations molded to shape, have demonstrated increased fuel efficiency, reduced carbon dioxide emissions, lower operating costs and improved reliability in service. Other applications include heavy artillery ballistic panels and complex structures where the desired fiber architecture is not easily attainable through other means, such as through the thickness reinforcement in specific locations. However, do keep in mind that 3D weaving opportunities are not necessarily always limited to composite applications. Products may also include complex fabric systems where integrated layers of different components — maybe even metal strands, monofilaments, filler strands or sacrificial inclusions — could be introduced to create complex filtration systems, biomedical surgical implants, spacer structures, and other innovations yet to be discovered.
P2 Roving Weaving Machine
Dornier’s P2 roving weaving machine is a natural extension of Dornier’s proven rapier weaving technologies and has become the workhorse of fabric production for composite applications. Available in several production widths, the P2 is capable of weaving from warp inputs fed by beams or creels or in some combination, and can be adapted to effectively handle heavy tows of glass, carbon, aramids, or other high-performance fibers as necessary. Hybrid and multi-material structures may also be accommodated as the application requires. Low twist filling thread guides and weft waste saving devices have been incorporated into the machine to aid in controlling costs and enhancing quality and reliability.
Technology And Training
In an effort to compliment these expanding technical capabilities and assist those unfamiliar with them, Dornier established a Composite Systems Technology Center at its facility near Lindau, Germany. The center is fully equipped with the technologies mentioned as well as the technical services and support to operate them. The center is available for existing and potential customers to trial new designs and concepts, or simply to witness these unique technologies in action.
“We can test new process variants, build mock-ups, perform pre-production evaluations and commission customer specific activities,” Klingele said. “This center allows us to advise customers on selecting the correct tools suited to their needs while also being able to demonstrate the turning of their ideas into real products.”
Given Dornier’s years of experience in developing and producing technical fabrics on its equipment, the company is easily able to provide consulting services to customers on developing applications, proof of concept samples, exclusive equipment modifications, and bespoke manufacturing technologies specific to unique applications. It also offers several iterations of comprehensive training programs and workshops to aid customers in the implementation and ongoing support of these new systems.
For Dornier, a company that introduced its first rapier weaving machine in 1967 and its first air-jet weaving machine in 1989, exploring the extremes of weaving technologies is simply a continuation of its engineering legacy and business philosophy. The Composite Systems suite is a natural extension of Dornier’s heritage and forward-thinking approach. As Klingele summarized, “We intend to continue advancing our technical offerings in order to provide equipment and technical support to the American and global composites industry with our offerings.” The potential is certainly there.
September/October 2021