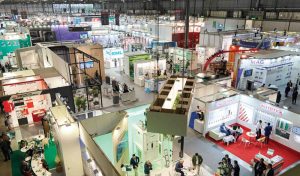
Technology highlights from the industry’s largest textile machinery show mostly focused on sustainability.
By Rachael S. Davis, Executive Editor
For those not familiar with the ITMA tradeshow, it’s hard to accurately convey the sheer magnitude of the event from the expansive exhibit halls filled with technology loaded lavish booths to the huge volume of visitors wandering the halls. In 2023, ITMA — a quadrennial textile trade show owned by the European Committee of Textile Machinery Manufacturers (CEMATEX) and organized by Brussels-based ITMA Services —occupied 200,000 gross square meters of exhibition space with 1,709 exhibitors from 47 countries taking up 118,300 net square meters of exhibit space at the Fiera Milano Rho in Milan, Italy, to showcase their innovations.
The overall theme for ITMA 2023 was “Transforming the World of Textiles.” Under that banner idea, several key ideas critical to defining and ultimately transforming the industry were highlighted including Sustainability and Circularity, Innovative Technologies, Automation and Digital Future, and Advanced Materials. It was clear observing the show floor that exhibitors embraced the sustainability pillar full on. Many of the technologies focused on sustainable manufacturing and recycling processes. Interestingly, the industry is moving on from Industry 4.0 and is already embracing the idea of Industry 5.0 — adding human, environmental and social aspects back into the Industry 4.0 ideas focused on robots and smart machines. This acceptance of robots and smart machines working alongside people in a sustainable and harmonious way certainly does paint a picture of a transformed textile industry.
Approximately 111,000 visitors from all over the globe attended the event over seven days.
No matter how long a visitor spent exploring the show floor — be it one day or all seven days — it would be impossible to visit every booth to view all of the technologies and developments. Similarly, it is impossible for TW editors to identify and select all the unique, eye catching and “cool” things on display at the show. But what follows is a slice of some of the interesting technologies displayed during ITMA 2023 from across the exhibit sectors and presented in no particular order.
There is much, much more to share from ITMA 2023, and in-depth, sector-specific coverage will be presented in future issues of TW beginning in the September/October 2023 issue.
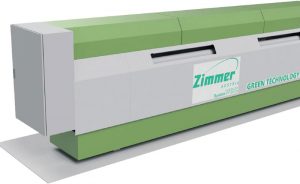
Zimmer Austria: Rotascreen Duplex Printer & STR System WENK
While digital printing continues its evolution and ascent in the textile printing world, by far the majority of textiles continue to be printed using screen printing technologies. Austria-based J. Zimmer Maschinenbau GmbH introduced a modified version of its Rotascreen technology at ITMA that allows duplex printing so a fabric may be printed on the front and the back at the same time. The Rotascreen line now also can be supplied in an open or closed bearing option depending on the manufacturer’s needs.
Zimmer also launched the STR System WENK, a rotary screen stripping and ironing machine also known as the “Green Machine.” The machine uses only water and high-pressure jets to clean photo emulsion from rotary screens so they can be reused up to 20 times. No chemicals or acids are required — just standard fresh water. Stripping time will depend on the emulsion used. The high-pressure jets also remove any creases to effectively “iron” the screens. After treatment, the cleaned screens emerge in a near to new condition. Developed in conjunction with Italy-based partner WENK S.r.l., the Green Machine may be fitted with an optional water recycling system to recapture and reuse the water in an economic and sustainable process.
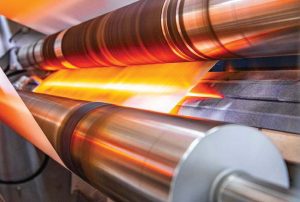
Benninger: SingeRay
Switzerland-based Benninger AG reports its new SingeRay singeing machine has exceeded all expectations selling more units already this year than ever anticipated. The machine was designed with energy savings, natural gas in particular, in mind. Made in Germany, the SingeRay features four singeing positions as well as two special aluminum burners with ceramic flame guiding bricks, which offer higher production speed and higher heat intensity. Its silicium carbide burning chambers with four cooling channels ensure complete combustion and a constant burner temperature, which also helps to keep the nozzle strip straight. The machine can be adapted to accommodate different widths of fabric and rather than just shutting down sections of the flame bar, the actual chamber width can be modified to close the gap on each side thus aiding heat conservation and saving energy.
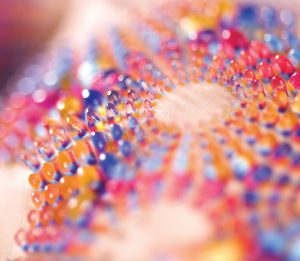
Stratasys: 3DFashion™ Direct-To-Textile 3D Printing Technology
In terms of being “different” and eye-catching, Israel-based Stratasys Ltd.’s 3DFashion™ direct-to-textile 3D printing technology was a stand-out. The 3D printing technology is some 30 years old, but the company said inquiries from customers drove it to develop the idea of 3D printing onto textile substrates. Stratasys offers advanced materials — full-color, translucent, rigid or flexible — that can be adhered to textiles and garments using the J850 TechStyle™ 3D printer. The company was at ITMA to introduce the concept and gauge interest in the technology.
The colors and geometries are basically unlimited and hindered only by the creativity of the designer, although for garment applications, the weight of the 3D printed material has to be taken into account. Initial tests show the resins can last about 20 washes currently, but the company is continuing its research and development for textile applications. Stratasys also is developing a 2D to 3D software tool to help J850 TechStyle printer users to adjust the height, color and texture of 2D images to transform them into 3D printed elements.
Examples of the technology on display at the booth included colorful wall art, embellished denim and bags, as well as technical textiles for auto-motive applications.
“ … Stratasys is ushering in a new era of textile printing that puts 3D printing technology directly in the hands of this community, opening up unlimited possibilities for them to introduce entirely new attention-grabbing added-value applications within their offering and drive new revenue streams,” said Enrico Toson, Stratasys’ marketing manager.
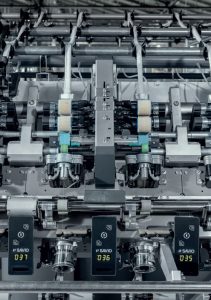
Savio: Lybra Smartspinner® Air-Jet Spinning Machine
Italy-based Savio Macchine Tessili S.p.A., long a specialist in yarn winding technologies, introduced its Lybra Smartspinner® air-jet spinning machine at ITMA 2023. Marketing and communication manager Eva Babbo acknowledged that other companies already do air-jet spinning technology very well and with the existing level of competition, Savio was determined to get it right and has been working to perfect its offering since 2016. In order to bring something to the space, Savio focused on the concept “We spin different.” The Lybra machine takes advantage of the Coanda effect, which is the tendency of a fluid jet to stay attached to a convex surface. As fibers enter the spinning nozzle, high-speed air jets create a helical flow that twists the fibers into a yarn.
One unique feature on the machine is the Multi Blend unit, which allows manufacturers to create mélange yarns as well as blended colors or blended fiber yarns. The flexible unit combines two slivers directly at the spinning unit, so instead of needing to preblend a sliver before spinning, a yarn manufacturer can blend and mix fibers as they are fed into the machine. The system can be adjusted to change the blend — from say a 50 percent white/50 percent blue sliver to a 30 percent white/70 percent blue combination — using the machine’s controls in a practically instantaneous manner. The machine is designed for high production rates, but with versatility and cost savings in mind.
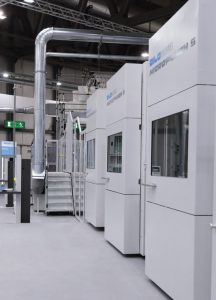
DiloGroup: MicroPunch
Ever the innovator, Dilo-Group did not disappoint with the introduction of its MicroPunch at ITMA 2023. The machine took approximately 20 years of study and research to come to fruition and the demonstration unit was ready just in time for the big reveal at the show.
Needlepunching technologies have traditionally been better suited for medium to high fabric weight ranges in part because the needles leave a mark in the resulting nonwoven structure, which is more apparent at lower weight ranges. Hydroentanglement is most suited to weight ranges less than 100 grams per square meter — resulting in fewer applications for these types of fabrics, although they have a stronghold in wipes making up approximately 85 percent of the market. However, the water and energy requirements for hydroentangling are great. Enter DiloGroup’s MicroPunch, a new option for lightweight needlepunched nonwovens ranging from 30 to 100 grams per square meter. The machine features an insane 45,000 needles per meter per board made possible with an innovative needle and needle board design developed in conjunction with Groz-Beckert. The needles move in and out of the fiber web in a manner that minimizes as much as possible any needle marks in the finished nonwoven. The machine runs at 160 to 170 meters per minute and the company reports up to 50 percent savings in energy per kilogram of fabric depending on the product. Fabrics made using the MicroPunch are strong and have more volume than a lightweight hydroentangled fabric. DiloGroup CEO Johann Philipp Dilo said interest in the machine was overwhelming during ITMA.
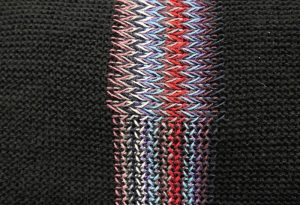
Stoll by Karl Mayer: ADF Concept Machine
Germany-based Stoll, a member of the Karl Mayer Group, introduced a prototype concept machine at ITMA 2023 — the ADF 530-16/4 ki WWK E7.2. The technology fuses flat knitting, warp knitting and weaving into one machine. The inno-vative yarn guides capable of 3D movement along with corresponding yarn feeding modules on this ADF model enable structures with sectoral poly-directional reinforcements and zones, which in con-junction with special and standard yarns can produce unique designs and functional structures with decorative seam effects. In particular, the machine offers interesting possibilities for medical structures, according to Matt Llewellyn, director of sales and marketing. Stoll also introduced the ADF 530-32 ki BcW E20 ultrafine gauge machine.
In addition, Stoll reports all its machines are 12-percent more efficient than previous models thanks to new needles and optimized cams, and feature a new oiling system that is easier to clean and allows the oil to be filtered and reused.
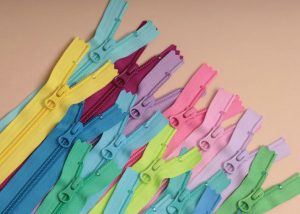
Erca Textile Chemistry Solutions: REVECOL® Textile Auxiliaries
Italy-based ERCA Textile Chemistry Solutions introduced a new generation of auxiliary chemicals made from used vegetable oil. The REVECOL® (Recycle Vegetable Cooking Oil) by ERCA product line features a complete range of chemical auxiliaries — such as dyeing pretreatments, leveling agents, softeners, and emulsifiers/detergents among other products — that may be used on all fiber types including virgin and recycled fibers. ERCA’s safe and environmentally friendly manufacturing process takes the waste oil and transforms it into high-performing auxiliaries with circular DNA. All products are certified by Global Recycled Standard, Recycled Claim Standard, bluesign®, Global Organic Textile Standard and listed in the ZDHC Chemical Gateway. Additionally, a bluesign Product Carbon Report revealed that REVECOL LV-TS has a 72-percent lower carbon footprint than the conventional chemical auxiliaries ERCA manufactures. ERCA recently collaborated with Patagonia® and YKK Corp. to successfully implement the use of REVECOL in YKK’s dyeing processes at Vietnam-based production sites.
“We at ERCA are always looking for innovative solutions through the development of products that are increasingly high performing, competitive and sustainable at the same time,” said Fabio Locatelli, head of ERCA’s textile business unit. “REVECOL is the perfect example of this and it represents the ‘so far missing piece’ for the production of textile materials that enable the approach to an increasingly responsible and certified supply chain without any compromise in performance.”
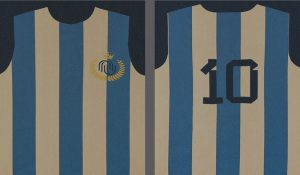
Pailung: AlterKnit/Vanguard Pailung: High-Speed Production Machine
Taiwan-based Pailung Machinery Mill Co. Ltd. launched the AlterKnit™ circular knitting technology at ITMA. This upgraded version of inverse plating knits alternate yarns into the fabric’s structure allowing yarns of different colors or composition to be knit together within the same row. Intricate patterns with sharp borders are possible and the fabric is reversible. The finished fabric may be highly patterned and does not need to be dyed or printed for colorful effects, which saves energy and resources. Both a single-knit and double-knit machine are available. The process also does not result in yarn floats that may make a fabric uncomfortable to wear and reduces yarn waste.
Monroe, N.C.-based Vanguard Pailung also introduced a newly designed circular knitting machine for high-speed production. The machine is now driven from the bottom to reduce torque and stress on the knitting elements; and the knitting elements are elevated further from the ground to accommodate fabric rolls up to 500 pounds for customers that dye fabric in large batches. The machine housing also was redesigned in a square format, which is cheaper to build for a more economical machine. In addition, the square design saves floor space. Vanguard reports four of the new machines can fit in the footprint that previously held only three machines.
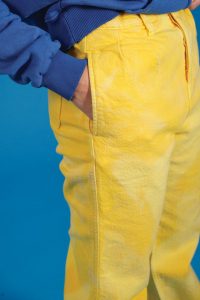
Officina39: Recycrom™ Dyestuffs & Ecobinder R
Italy-based Officina39 operates under the tag line “Chemistry Plus Creativity,” and the company has certainly found some creative resources to use as starting mate-rials for its Ecobinder R Series and Recycrom™ dyestuff products. The Ecobinder R Series is a binder suitable for printing, spray, coating and dyeing applications that is made using 100-percent post-consumer recycled polymer obtained from recycled windshields and other types of laminated and safety glass.
In 2018, the company introduced its Recycrom pigment powders — derived from 100-per-cent recycled used clothing, fibrous material and textile scraps. The waste textiles are processed using an upcycling process developed by Officina39 to create the pigment dyes. The company has continued to develop and refine this process and at ITMA 2023, launched the Recycrom Ready to Dye Dark and Bright line. The line offers 15 standard, in stock colors made using a minimum of 65 percent recycled textile pre- and post-consumer materials. The Ready to Dye pigments are suitable for use on cotton, wool or nylon as well as any cellulosic and natural fiber or blends. According to the company, 100 kilograms of textile waste can produce enough Recycrom Ready to Dye pigment to dye 20,000 T-shirts. Recycrom Pure allows manufacturers to partner with Officina39 to create custom dyes using their own scraps and textile waste.
According to Officina39, Ecobinder R can be combined with Recycrom pigments for a circular solution.
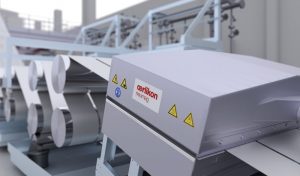
Oerlikon Neumag: EvoSteam
While the demand for recycled yarns continues to grow, so does global demand for polyester staple fiber. The EvoSteam process introduced at ITMA by Germany-based Oerlikon Neumag is aiming to revolutionize the polyester staple fiber production process and make it economical, resource- and environment-friendly. According to the company, the EvoSteam process offers a 12-percent increase in efficiency, a reduction in production waste of up to 50 percent, energy savings of up to 8 percent, and a reduction in carbon footprint by up to 20 percent, compared to conventional staple fiber systems. Instead of using a liquid immersion bath, a coordinated setup of godets and pulsed spray nozzles adds only the precise amount of moisture needed to the process, which results in water savings of up to 10 million liters a year. The process also reduces the amount of spin finish needed, and energy required to produce the fiber is reduced since the fiber requires less drying at the end of the process.
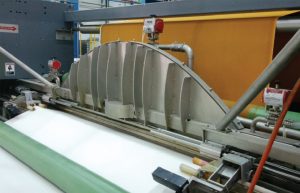
Navis Tubetex: Gaston Systems Chemical Foam Solutions (CFS®)
The President and CEO of Lexington, N.C.-based Navis Tubetex, Will Motchar, noted there was a lot of interest at ITMA in the company’s Gaston Systems’ foam technology for applying a low water foamed chemistry onto or into a substrate. The technology was originally used for chemical finishing where the precision applicators allow one chemical to be applied to the front of a fabric while a different chemical is applied on the back. But further applications for this proprietary technology are developing because of the ability to reduce chemical waste, as well as water and energy consumption.
The company recently collaborated with biofabrication company Modern Meadow who was searching for a partner that offered an application technology suitable for its Bio-FREED™ powered by Bio-Alloy™ plant-based protein and biopolymer. When used as a dyeing pretreatment, the bio-based technology makes the fabric much more receptive to dyes. Research is continuing, but the process is interesting for its ability to reduce energy, water, and dyes and chemicals use during dyeing. When applied to a blended textile substrate using the Gaston Technologies foam equipment, Bio-FREED results in an estimated 95-percent reduction in water, 75-percent reduction in energy, and an 80-percent reduction in the amount of dyes and chemicals needed. A partnership to develop the technology among Navis TubeTex, Modern Meadow Bio-FREED and Italy-based manufacturer Limonta was one of the three finalists for the 2023 ITMA Innovation Award. “We believe that sustainability should be at the fore-front of every industry, including textile manufacturing,” Motchar said.
“Teaming up with Modern Meadow allows us to offer our clients cutting-edge solutions that align with their sustainability goals. Together, we can drive meaningful change and shape the future of the textile industry.”
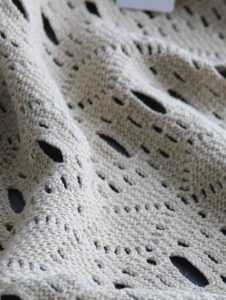
Karl Mayer: RSJFS 4/1 EL Warp Knitting Machine
ITMA made it clear that the interest in natural fibers and especially recycled natural staple fibers is on the rise. In some instances however, these recycled and natural yarns can present problems in manufacturing. The latest Raschel crochet machine from Germany-based Karl Mayer— the RSJFS 4/1 EL, 130” E14 “Crochet-Knit” model — features enhanced knit-ting parts as well as a synchronized suction and blowing system that helps manage excess lint so recycled yarns may be processed with ease. The machine can produce dense and complex patterns in crochet or knitted styles for handmade looks suitable for fashion applications. The machine features a fall plate as well as double switching technology in the jacquard bars to enable a wide range of floating designs and complex patterns. The Crochet-Knit machine will be available in early 2024.
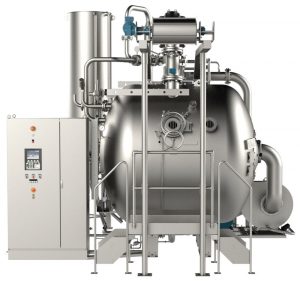
Thies: Signature Series Jet-Dyeing Machine
Germany-based Thies Textilmaschinen GmbH & Co. KG debuted the Signature Series machine, which was developed to dye cotton fabrics at the lowest possible liquor ratio using no salt. The jet-dyeing machine operates at an ultra-low liquor ratio as low as 1:2.3. For each batch, the liquor ratio is determined based on the fabric’s adsorption level plus a small quantity of water roughly equal to 0.6 liters per kilogram to ensure the pump used to circulate the dye liquor remains flooded. By removing water from the process, more of the dyestuff goes on to the fabric instead of hydrolyzing and ending up as a waste product. The machine delivers small amounts of highly concentrated dye throughout the dye cycle to ensure a level dyeing.
The machine can be used in three modes to dye using full salt, low salt or no salt. No salt dyeing reduces the effluent, which helps companies in countries with strict effluent policies; and both no and low salt processes save dyestuff and chemicals for both cost savings as well as environmental advantages.
The Signature Series prepares, dyes and rinses the fabric without the need for intermediate processes or machines. As a high-pressure vessel, the machine also can be used to dye polyester and is a great option for a company that handles a variety of fabric substrates. An adjustable, curved J-box also means the machine can handle light and heavy fabrics in full and reduced loads.
“Thies is opening a new chapter in fabric coloration,” said Verena Thies, managing shareholder, Thies. “Signature’s innovative ultra-low liquor ratio significantly enhances dye effectiveness, resulting in up to 20 percent decrease in dyestuff consumption. By combining Thies’ cutting-edge advancements, water usage is minimized by 25 percent.” These decreases are based on a comparison with Thies’ iMaster, the Signature’s predecessor.
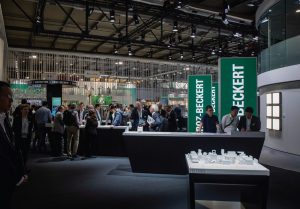
Groz-Beckert: Needle “Innovation Through Cooperation”
Needles may seem like such a small part, but they are an extremely important component of any knitting or nonwoven machine. Germany-based Groz-Beckert is an experienced and accomplished producer of needles for various industries. At ITMA, the company unveiled several new needles and needle systems developed in conjunction with industry partners under the motto “Innovation Through Cooperation.”
As noted earlier in this feature, the right felting needle was instrumental in DiloGroup’s development of the MicroPunch needlepunching machine. The design embeds Groz-Beckert needles as a module in a plastic mold. A new intensive needling technology developed especially for light grammages results in felting needle modules with very high deformation resistance and offers new dimensions in needle density. The modules also were designed for easy and economical assembly and replacement.
In the knitting sector, Groz-Beckert also collaborated with Vanguard, Santoni and Mayer + Cie. on new products.
Germany-based Mayer + Cie’s Relanit 3.2 HS circular knitting machine features the new LCmax™ needles and SNK-SF sinkers. The modified wave shape shank geometry of the LCmax simplifies handling and reduces friction. The needle reduces energy costs up to 20 percent through minimal power consumption and reduced machine temperatures. The SNK-SF sinker was designed to be much more wear resistant and can reduce dirt deposits to extend machine cleaning intervals.
The Innotas system, comprising the SAN™ DUO needle and SNK DUO-OL sinker, was developed for Italy-based Santoni’s Innotas large diameter, single jersey machine. Both components feature a low shank — to minimize soiling when using abrasive yarns — and a predetermined breaking groove, which enables controlled needle breakage at the desired place in the event of wear. The system is self-cleaning and does not need to be over-hauled and cleaned every eight weeks; and open cam parts allow fluff to be expelled, which reduces machine downtime.
Groz-Beckert also engineered a new compound needle for Monroe, N.C.-based Vanguard Pailung’s high-speed circular machines, which was designed for high productivity and high process reliability while reducing stress on the yarn. The needle, exclusive to Vanguard for now, can operate at a speed factor of 2200.
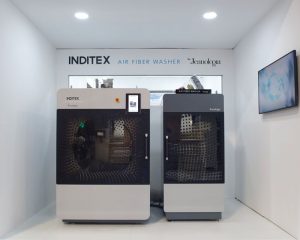
Jeanologia: Atmos & Air Fiber Washer
Spain-based Jeanologia S.L. was founded in 1994 with the mission of transforming the textile industry, and developing technologies and eco-efficient production models. At ITMA, the company launched a number of technologies in the “era of air” — so called as it aims to enter a new era of denim production with no water, no waste and zero discharge. The new Atmos atmospheric washing process pairs its G2 ozone technology with the new patented INDRA system to produce a stonewashed, authentic vintage look on denim without using water, chemicals or pumice stones. “Thanks to INDRA, we can achieve perfect control of the humidity and atmosphere temperature to achieve exceptional garment abrasion and discoloration,” said Carmen Silla, global brand & marketing director, Jeanologia. “We attain the same effects that were previously only possible with water, chemicals and pumice stones, while ensuring perfect reproducibility and enhanced productivity in a more efficient, sustainable and safe way.”
Jeanologia also collaborated with Spain-based apparel giant INDITEX to come up with a solution to reduce the release of microfibers from garments. Their development — the Air Fiber Washer — is based on testing that shows the majority of fiber fragments are released in the first three washes at home. To combat this, the Air Fiber Washer features a polyhedric drum and uses air flow to extract microfibers from the garments. According to Jeanologia, the Air Fiber Washer extracts up to 60 percent of microfibers during the process, which are captured using a microfiltration system and may be repurposed or recycled. Estimates indicate each Air Fiber Washer will collect up to 325 kilograms of microfibers per year. “Working with Inditex is a great experience and source of pride,” said Enrique Silla, Jeanologia president. “This initiative is just the first step in the mission we have set for ourselves to minimize the impact of microfiber shedding in textile manufacturing and in the product life cycle.”
July/August 2023