SDS-ONE APEX series design system is used for efficient development of the world’s finest knitwear.
TW Special Report
John Smedley Ltd. is the oldest continuously operating knitwear manufacturer in the world, producing fine gauge knitwear from its Lea Mills, Derbyshire factory since 1784. Crafted from the finest noble fibers of extra-fine merino wool, John Smedley’s Sea Island cotton and other luxury blends, the company is known as creators of the “World’s Finest Knitwear” that is designed to last, made in England and distributed the world over. Its menswear and womenswear ranges are available worldwide via its stand-alone retail stores in the St James’s, Mayfair and Marylebone districts of London; and the Tokyo, Yokohama and Kyoto areas of Japan. Exports are made to more than 47 countries worldwide via international wholesale partners such as Mr. Porter, Selfridges, Harrods, Harvey Nichols, Isetan, Bergdorf Goodman and Le Bon Marche.
Brilliant History Of Achievement
John Smedley holds two Royal Warrants for ‘the manufacturer of fine knitwear” from Her Majesty The Queen & His Royal Highness The Prince of Wales. In Her Majesty The Queen’s Birthday Honors List 2020, Ian Maclean, managing director of John Smedley Ltd. and eighth-generation family member, was awarded an MBE for services to the UK textile industry and the COVID-19 response. John Smedley collaborated with The Emergency Design Network to design and manufacture medical grade scrub garments which were distributed to more than 30 different hospitals, GP surgeries and care homes in the London and Derbyshire areas.
John Smedley has one of the largest knitted garment archives in the world and has counted the likes of Marilyn Monroe, Audrey Hepburn, The Beatles, Sean Connery, Kate Winslet, Robert DeNiro, Ed Skrein, Eva Longoria and more amongst its celebrity fans. Over the years, John Smedley has supported and collaborated with many leading designers to champion British manufacturing including Vivienne Westwood, Paul Smith, Lou Dalton, Sacai, Fragment, Comme Des Garcons and Holly Fulton.
Digital Encounter
By implementing Japan-based SHIMA SEIKI’s SDS-ONE APEX4 design systems and APEXFiz Design software, the company has been able to shorten lead time for development and prototyping as well as to reduce sampling costs, and is now able to spend more time for creativity.
Shima Seiki spoke with Design Director Pip Jenkins about the company’s development process. “We are using SDS-ONE APEX series for both swatch developments and product prototyping,” Jenkins explained. “Before using SDS-ONE APEX series, multiple stitch and pattern developments were done on the production machines before prototyping and every colorway swatch was knit down for the wholesale presenters, which could pan over one month from programming and knitting to washing. From a cost standpoint, there were also a lot of problems with high waste in re-knitting prototypes and swatch development, the need for using high-priced yarns, the need for using programmers to realize designers’ ideas, and the need to use knitting machines for high volume development which prevented them from being used for bulk production.
“After seeing the knit simulations, we decided to stop knitting real swatches for the wholesale side of our business and start producing them digitally using SDS-ONE APEX series. We could also bridge the gap between designer and programmer, meaning product pattern development was correct the first time around. In addition we could develop ideas and check colorways without having to knit anything. Development is now done on the SDS-ONE APEX series, after which we go straight in to prototyping and in most cases we are right the first time. All colorways are now digitally simulated within a few days for our wholesale presenters. This change contributes to reduced waste and lead times, less yarn used during development, fewer programmers, and increased development efficiency due to less use of knitting machines.”
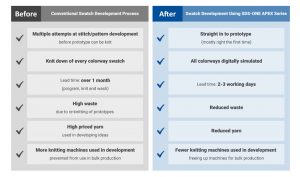
Clear Results
Using SDS-ONE APEX4 and APEXFiz Design software has greatly improved John Smedley’s work process (see Figure 1).
“With virtual samples we are able to see the development of our ideas without having to use a machine for production,” Jenkins added. “And our programmers feel it is clearer what they need to develop, and our designers feel their ideas have been translated correctly. SDS-ONE APEX not only helps our company to go digital, but it also allows for shorter development times, less waste of high value yarn, less time spent on production machines during the prototype, swatch, and colorway developments, as well as more time to exercise our creativity.”
December 14, 2023