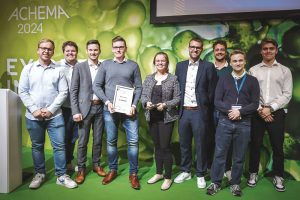
Textile supply chain practices in Germany are poised to be positively impacted by the country’s precarious energy supply situation.
TW Special Report
It’s notable that major developments in the textile manufacturing supply chain are at present to be found at either side of the basic yarn spinning and fabric formation stages of production.
Software advances for all technologies aside, one major focus is currently on the development of more sustainable new feedstocks, fibers and chemicals — both natural and synthetic — while another is on dyeing and finishing processes, which for a long time have been the most resource draining stage in the manufacturing chain in terms of energy, water usage and waste.
ACHEMA 2024
Fittingly — given the current major interest in the recycling of synthetic fibers — re.solution, a spin-off from RWTH Aachen University, has just claimed the ACHEMA 2024 Start-up Award.
ACHEMA, held every three years, is a trade fair for the processing industries, and the latest edition recently took place in Frankfurt attracting 2,842 exhibitors from 56 nations and 106,000 visitors from 141 countries.
The event showcased the latest developments in the chemical, pharmaceutical and food processing industries — including the production of synthetic fibers — and also featured a total of more than 900 lectures, discussion panels and workshops.
Start-Ups
The fact that start-ups are now an integral part of all major processing industries was demonstrated not only by the number and quality of the applications for the ACHEMA’s 2024 Start-up Award, but also by their range — although all generally reflected the major manufacturing trends of sustainability and digitalization.
Re.solution has developed a new chemical process based on hydrolysis for recycling PET polyester with renewable energy and low water and chemical consumption.
The robust process has been further designed to overcome textile-specific recycling challenges such as accommodating fiber blends and the removal of impurities, resulting in high product quality.
The start-up has also developed a salt-waste free downstream recycling method of dealing with the hydrolysis depolymerization technology’s consumption of vast amounts of auxiliary chemicals. With the successful recycling of these additives, re.solution reports it can produce feedstock that is sustainable and price competitive with virgin feedstock.
Re.solution is currently being funded by Germany’s Federal Ministry of Economics and Climate Pro-tection (BMWK) and the European Union as part of a research transfer program and plans are now underway for rapidly scaling the process up.
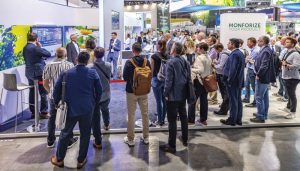
Green Hydrogen
One of the major themes of this year’s ACHEMA was the potential of green hydrogen as a key element of the energy transition, which given Germany’s precarious energy supply position, is being taken very seriously by the country.
Hydrogen is a versatile chemical feedstock and energy carrier that can be used to secure energy supplies for many sectors and if produced in a climate-friendly way, has the potential to significantly reduce carbon emissions and ultimately contribute to bringing them down to zero.
However, the production of hydrogen is comparatively energy-intensive, which is why it should be used for applications where renew-able electricity cannot be utilized directly. In addition, the costs of producing hydrogen are currently still high, and the capacities for generating it are insufficient. This means that large investments need to be made in developing electrolysis capacities, compensating for higher operational production costs, as well as ensuring stable conditions for selling green hydrogen at an economically viable price.
Germany’s government is supporting these efforts through its National Hydrogen Strategy which has made several billion euros available from federal funds to promote hydrogen generation, build the necessary infrastructure and enable its use.
WasserSTOFF
Funded projects are now underway across the entire value chain, including the use of hydrogen as an alternative fuel for energy-intensive industries, and one such industry is certainly the dyeing and finishing of textiles.
Since November 2022, Germany-based A. Monforts Textilmaschinen GmbH & Co. KG has been leading a consortium of industrial partners and universities in exploring all aspects of this fast-rising new industrial energy option in a three-year WasserSTOFF project. The aim is to establish to what extent hydrogen can be used in the future as an alternative heating source for textile finishing processes.
Monforts specializes in advanced technology for fabric finishing based on successive industry developments over many decades and is celebrating its 140th anniversary this year. It was founded in 1884 in Mönchengladbach, Germany, where it is still head-quartered today, which is also where its Advanced Technology Centre (ATC) is situated.
Monforts Montex tenter frames —for processes such as drying, stretching, heat-setting and coating — are an industry standard for the fabric finishing industry, particularly in the denim and home textiles sectors, providing a number of advantages in terms of production throughput and especially in energy efficiency and savings. The other key technologies in the company’s range include relaxation dryers, Thermex dyeing ranges, Monfortex compressive shrinking ranges and Montex Coat and coaTTex coating units.
Concern
The cost of energy remains a major concern for textile manufacturers and for the latest Monforts Montex tenters, the MonforClean heat recovery system with air/air or/and air/water is fully integrated into the tenter chamber. In combination with other new features, the heat recovery system results in energy savings of up to 43 percent.
The company also offers a number of options for retrofitting to existing lines such as the Monforts universal Energy Tower — a flexible, free-standing air/air heat exchanger for recovering the heat from the exhaust air flow of thermal processes. It can result in a 25-percent reduction in the energy consumed by a line, depending on the exhaust air volume and operating temperature.
A Monforts Eco Booster, integrated into the chamber design of the Montex tenter, is another retrofitting option. As a single heat recovery system with automatic cleaning, it can be added to existing ranges and up to 35-percent energy costs can be saved. In addition, the Eco Booster consumes only minimal amounts of water during the cleaning cycle and the entire process is controlled and monitored automatically.
Options
Within the WasserSTOFF project, tests on laboratory equipment together with associated partners have already been carried out and the results are now being transferred to an industrial-scale pilot tenter frame at the Monforts ATC in Germany.
The next stage in the project is to compare the results of trials powered partially or fully by hydrogen, with those of existing energy combinations of electricity, gas and steam, as well as fully analyzing the full impact of the various energy-saving technologies that have already been developed.
“Green hydrogen’s potential as a clean fuel source is tremendous, but there is much we need to explore when considering its use in the textile finishing processes carried out globally on our stenter dryers and other machines,” said Monforts Managing Director Gunnar Meyer. “Everybody knows that textile finishing is a high energy consuming process and to make the processes more efficient, we already offer several solutions, but as a technology leader we are also rising to the challenge of exploring alternative heating options to be ready for the future.”
2024 Quarterly Volume III