Finishing RoundupBy Gary N. Mock, Ph.D., Technical Editor Finishing TouchNew developments in wet and dry finishing produce value-added products for a discerning public. I t is often said that finishing is the most important step in the textile operation because the next set of eyes to see the product are those of the customer. New finishing products are continuously developed around the world, but special emphasis is placed on them during big show years. While 2001 was not an ITMA year (the next show will be held in Birmingham, United Kingdom, in 2003), there were three important shows this past year: ATME-I (Greenville, S.C.) in April, and OTEMAS (Osaka, Japan) and the new ITMA Asia (Singapore), both held in October. ITMA Asia was organized by the European Committee of Textile Machinery Manufacturers (CEMATEX) to offer a major show in the important Southeast Asia market with the specific goal of minimizing the numerous small and large fairs that had sprung up in the ITMA off-years. The cost of showing at all of these venues was becoming prohibitive.Chemical finishing has been shown to be extremely important when used in synergy with developments from machinery manufacturers. Partnerships abound. Following is a brief look at developments this past year. Wet FinishingAquatex, a new development that sprang out of the nonwovens field, has been released by Germany-based Fleissner GmbHandCo. A curtain of water jets 0.1 to 0.15 millimeters (mm) in diameter with 40 to 80 jets per inch, operating at a pressure of 20 MPa, and jet speed of 200 meters per second (m/s) impinge on the textile substrate as it moves underneath. The substrate is supported on a perforated belt or drum and is transported under the water curtain. Water is removed by suction and recirculated. The resulting fabrics are softer and can be constructed with fewer ends per inch than fabrics finished by other means. Upholstery has similar cover with fewer ends per inch and without a latex backing. Denim fabrics made with fewer ends and lower chemical content are more stable and shrink less during compacting. Because more than 3 billion denim articles are manufactured worldwide every year, there is a tremendous opportunity to make more surface with less woven product.For more than 30 years, fluorocarbons have been used in the textile industry to achieve water-, oil-, and soil-repellent properties. New chemical systems released by Rudolf Chemie GmbHandCo. KG, Germany, have enabled finishers to achieve these same results in an environmentally friendly, emission-free way. The reduction of the emission load by about 90 percent is dramatic. Results are achieved using booster chemicals that protect the reactive polyurethanes until temperatures are above 110°C. Surface coating and film stability are dramatically improved. Further, garments washed and air-dried are able to restore the important reorientation of the fluorocarbon tails without tumble drying or ironing.The consumer expectancy for easy-care finishing of cotton has been extended to woolen garments. There are two ways to negate the felting action of wool scales. The oldest and most common method involves the use of active chlorine to erode the scales by oxidation. The surface is subsequently masked by an epichlorhydrine resin. Ciba Specialty Chemicals, Switzerland, has released Dicrylan WSR, a new polyurethane system for washable wool fabrics. The new polyurethane pre-polymer allows crosslinking between the isocyanate group and the wool fiber, thereby masking the woolen scales that cause felting. A silicone rubber additive imparts a softer handle that can withstand tumble drying.Recently, phase change materials (PCMs) have been made possible using products developed for the National Aeronautics and Space Administration (NASA) to protect astronauts from extreme variations in temperature. More than 500 PCMs are known. Frisby Technologies, Winston-Salem, N.C., has been a pioneer in the development of technologies for microencapsulation of these various materials. Coating systems such as the Ciba Dicrylan PMC/PHR, in combination with PCMs, have been shown to offer comfort over a wide range of conditions.Cavitec AG, Switzerland, has been a leader in the development of technical textiles. The improved quality and application flexibility, together with a tremendous drop in cost, make hotmelt the most advisable adhesive for composites in general. The meltprint and screenprint methods use either an engraved roller or a specially designed screen to apply the hotmelt onto a substrate that is subsequently laminated with another substrate to form a composite. Cost, weight reduction and recyclability have put additional pressure on the automotive industry to find new ways to build cars. Comfort, durability and fogging are important in the design of automotive interiors. Hotmelt lamination offers clear advantages. Laminating and coating technology was given a boost when Schaetti AG, Switzerland, manufacturer of thermofusible powders, took over the lamination technology of Kannegiesser and now offers a complete range of thermofusible adhesive products.The worldwide boom in the use of elastane fibers has led to new technologies to safely handle these elastic fabrics without damage. Growth is estimated at 12 to 13 percent for the foreseeable future. It has been estimated that nearly 50 percent of the garments being produced today contain some elastane to help with shape retention. The EcoFix/2 tubular finishing system by Lindauer Dornier GmbH, Germany, stabilizes by heat-setting in tubular form. Two separate chambers allow the goods to be set with minimal selvage marks from being rolled on the knitting machine. If goods are processed soon after knitting, the roll edge is nearly invisible following finishing.Bianco S.p.A., Italy, has also developed a new Linea apritubolare, or tubular opening line, to handle and stabilize tubular goods at speeds of 60 to 80 meters per minute (m/min).

Schematic of Dornier’s EcoFix/2 heat setting machine for tubular knitwear. DryingThe yellowing effect of elastane-containing fabrics caused by direct gas and oil-fired drying has been eliminated with Germany-based A. Monforts Textilmaschinen GmbHandCo.s Exxotherm indirect gas heating system. Hot combustion air is fed from the gas burner through an isolated heat exchanger within the tenter and exhausted by a secure exhaust duct. No combustion gases contact the fabric. Exxotherm is available for the Montex 5000 and as a retrofit for all Montex 4560 (F configuration) machines. Dry FinishingSoftening denim by surface abrasion during garment finishing is time-consuming and can destroy the garment-finishing machines. The Petra machine developed by Biancalani S.p.A., Italy, and first shown at ITMA 99 in Paris, has been made more reliable and delivers higher productivity. Operating at 10 m/min, the Petra uses abrasive cylinders combined with water. The moistened fabric is fed directly into a compressive shrinkage machine for final finishing.The latest development from Comet S.p.A., Italy, is the Pegaso-X11 napper. The active surface uses four silicone carbide brushes and four sandpaper sueding rolls to soften or sand without raising a noticeable pile.The CIBI Compactex, a new compacting machine by Cibitex S.r.l., Italy, is capable of handling widths up to 3.4 meters. The line was developed to soften and stabilize bed sheeting and home furnishing fabrics.SperottoRimar, Italy, a member of the Switzerland-based Santex Group (American Santex Inc., Spartanburg, S.C.), has recently added the Decofast continuous-steam decatizing system to its product line. The objective of Decofast is to exceed the results of traditional batch decatizing machines that use the continuous-atmosphere decatizing process. The machine features adjustable steam under pressure up to 3 bars at temperatures up to 135°C. Decofast is suited for pure wool worsted fabrics, stretch fabrics in wool and poly/wool blends, woolen fabrics in wool/wool blends and pile fabrics, as well as cellulosic and silk fabrics. Applications included for the process are as a final decatizing treatment, as a preparation of fabric before kier decatizing, and as a finish decatizing treatment after kier decatizing. Santex has developed a new Santa brush machine that uses abrasive brushes. In singeing, Menzel, Spartanburg, offers the high-velocity singer (HVS). The machine is the result of a complete reengineering project and, according to the company, performs at three times the speed of traditional singers. The firing rate of the burners is automatically proportional to line speed, keeping the singeing rate constant. ParksandWoolson Machine Co. Inc., Springfield, Vt., has introduced a new Phoenix Polybrush sueding machine for knitted or woven fabrics of all weights (See DP&F News, TW, January 2002). The sueding machine produces a drapeable fabric with a soft hand, according to the company.Eduard Kusters Maschinenfabrik GmbHandCo. KG, Germany (Zima Corp., Spartanburg), has redesigned its two-roll calender with the Swimming Roll to create a more compact and maintenance-friendly machine. The calender features new, up-to-date components, is service-friendly, and can be used in a small space. As well, it features an optimized piping system for lubrication, a cardan shaft drive, decentralized I/O wiring, a Siemens operator panel and easy change of the Flexroll sleeve.Glenro Inc., Paterson, N.J., recently purchased some of the assets of Burlington Textile Machinery Corp. (BTM), also in Paterson. The technology and manufactured product lines of BTM Corp. that were purchased include: fabric-guiding and spreading systems; Tru-Wind Surface and A-Frame winders; accumulators; Spraymiser low-moisture applicators; Tru-Brush lint-removal and pile-orientation systems; laboratory padders; automated comforter filling ranges; roto-brush wet-lint filters; and BTM designs of many auxiliary machines.Glenro also has new offerings in the area of flatbed fabric-laminating machines. Glenros systems place the materials under precisely controlled heat and pressure. A continuous pane of heat from the top and bottom with pneumatically adjusted pressure produces finished materials with complete adhesive coverage for a strong bond. The process eliminates wrinkling, as well.
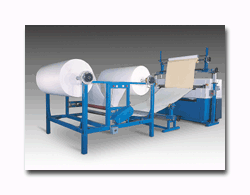
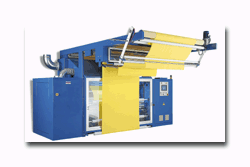
Two new machines were introduced recently by Lafer S.p.A., Italy. The first machine, Ultrasoft, was designed to create a dense and low-cut brushed-suede finish on knitted fabrics. The UltraSoft is supplied with six brushes in drum configuration, which create a multiple action effect. Both the drum and the brushes can rotate in different combinations to achieve the desired surface finish on different fabric types. Originally developed for knits, the UltraSoft also has been shown to work well on woven fabrics, according to the company. Lafers second new finishing machine introduction, Microsand, incorporates synthetic diamond emery on 24 rollers. It is suitable for all types of fibers and structures, but it has proven popular on shirtings and synthetics.March 2002