I
n order to remain a strong player in the global textile game, Rieter Machine Works Ltd.,
Switzerland, has developed new training systems for its draw frames and has introduced two new
combers.
Computer-Aided Training System
The proper setting and maintenance of spinning machinery are essential for achieving optimum
yarn quality, and require plant personnel with the appropriate know-how. When personnel change,
this knowledge must be reestablished through training.
As an alternative to external training, and in an effort to keep up with rapid technical
changes that make increasingly heavy demands on today’s textile industry, Rieter has developed the
Computer Aided Training System (CATS) for the RSB-D 35 and SB-D 15 draw frames. CATS also will be
available soon for the RSB-D 30 and SB-D 10 draw frames.
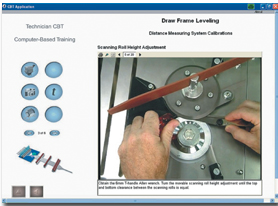
The Draw Frame: A Quality-Defining Machine
Rieter draw frames have set global standards for sliver quality. More than 20,000 RSB and SB
draw frames sold in 98 countries bear witness to the exceptional success of these machines.
According to Rieter, draw frames demonstrably ensure yarn quality and running properties with
minimal capital expenditure, and are reliable and operator-friendly. Rieter reports the machines
operate without requiring any special attention, which means that maintenance may sometimes be
overlooked.
Customer Training
External training on Rieter’s premises has unquestionable advantages. Explanations can be
given and handling practiced with no time constraints while the machine is at a standstill, and
questions can be dealt with individually. The disadvantages of conventional training courses are
familiar, for example, a large amount of information is communicated in a short time. What has been
learned can be practiced, but not always in-depth. Back home, the course file ends up in the filing
cabinet, since there is work to be done. If problems arise, personnel must meet deadlines, and the
file is not referred to. What is more, during day-to-day operations, the barriers to optimizing
machine settings are fairly high. If one ascribes to the motto ‘If it ain’t broke, dont fix it,’
the machine’s potential may not be fully realized in favor of uninterrupted production. New media
technologies enable information and learning processes to be designed with increasing flexibility
for individual needs.
CATS enables complex facts and sequences of motion to be presented and discussed using a
multimedia approach. Explanations using a combination of text, illustration, sound, video and
animation are easy to understand. System users soon find their way around the program and thus
achieve productive learning results.
The student’s knowledge after working through a CATS lesson is often better, more balanced
and firmer than after conventional instruction. Tests have shown that what has been learned with
the help of CATS is memorized better because the student is actively involved in the learning
process. Learning targets are achieved in a shorter time, which reduces the training period by 20
percent or more. Students may also organize their own time at the computer with CATS.
Easy Access To Information
The CATS RSB-D 35 runs on any customary office personal computer. Navigation is easy and
self-explanatory. After entering a personal password, the student may commence individual training.
CATS is organized into three main sections:
Introduction: This provides a comprehensive overview of the purpose and function of the RSB
draw frames.
Training: This includes topics related to the machine as a whole with all relevant
mechanical, electrical, electronic and technological settings, including laboratory testing.
Self-Test Certification: This allows the student to check his knowledge by means of
multiple-choice questions. When he leaves the system, the questions answered to date are
automatically assessed and statistics displayed.
A glossary with all terms relevant to the draw frame may be accessed from any position. The
CATS study package comprises explanations totaling more than 22,000 words, more than five hours of
video and animation, more than 80 glossary entries, and more than 1,000 photographs.The training
program is available in English, Turkish and Chinese and soon will be available in Urdu.
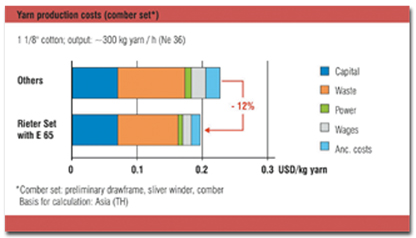
Higher Efficiency Through Good Training
The current training trend is toward modern learning media, which are readily accepted by
students. With well-trained personnel, it is possible to realize the full potential of the RSB-D 35
and SB-D 15 draw frames, as well as the D 30 and D 10 predecessor models. CATS aids in this process
through its easily understandable form.
However, CATS RSB-D 35 not only is a training medium; it is a comprehensive reference work
about the draw frame as well. It also is possible to print out individual subjects with a click of
the mouse.Together with Rieter’s Sliver Professional expert system, CATS ideally complements the
performance package of the machine, and ensures the efficient production of high-quality yarns,
according to the company.
New Comber Models
The new E 65 and E 75 (ROBOlap) comber models are the world’s first combers to achieve a nip
rate of 450 per minute in mill operation, and thus a daily output of more than 1,500 kilograms (kg)
of combed sliver per machine.
Several thousand E 62 and E 72 combers currently are in operation, mostly with nip rates of
between 370 and 400 per minute. Rieter reports it has demonstrated that its combers can be operated
continuously at nip rates of up to 400 per minute while maintaining superior technological values.
This experience, together with Computer Aided Process Development (CAPD) – computer simulations of
the combing process specially developed by Rieter – formed the basis for further production and
quality improvements. By utilizing proven elements of the predecessor models and incorporating
further optimizations of various combing process parameters, the new CAPD+ process has boosted the
nip rate to 450 per minute and output to up to 68 kg per hour.
Despite the significant increase in production of some 13 percent, no compromise has been
made with regard to raw material utilization and running properties, according to Rieter. As with
the predecessor models, these latest-generation machines also feature improved fiber selection and
thus up to 3 percent higher raw material utilization.
The stress on the mechanical elements has been further reduced by CAPD+. This means reduced
stress on the fiber, optimum web formation, constant combing quality, lower power consumption,
reduced wear of the combing elements and longer service life of the installation.
The running properties of the E 65 and E 75 allow these machines to achieve efficiencies of
up to 96 percent, according to Rieter.
Combing Technology Components
The combing elements also have been adapted to the new combing process. The Ri-Q-Top top
comb developed by Rieter and the new Primacomb 8014 and 8015 circular combs guarantee maximum
combing efficiency at any production level, according to the company. The self-cleaning effect
means soiling of the top combs, and therefore maintenance, is reduced by up to 75 percent. This
improvement in cleanliness has a positive impact on the machine’s running properties and quality
consistency.
Drafting Technology
Various elements of the technology featured in Rieter draw frames are utilized in the E 65
and E 75 combers. Variable break draft and main draft gaps facilitate ideal fiber guidance in the
drafting zones.These improvements enable optimum combing results to be achieved with 1-inch cotton
fibers. A newly developed web consolidation feature guarantees faultless sliver formation, and
precisely positioned suction elements ensure maximum cleanliness of the drafting system, according
to Rieter. These innovations improve the spectrograms and reduce the coefficient of variation value
by an average of 0.5 percent.

and main draft gaps.
Unique Combing Automation
Rieter still is the only supplier of a fully automated combing set with proven qualities in
a large number of installations. Almost 1,000 combers with automatic lap change and batt piecing
system (ROBOlap) and automatic lap transport system (SERVOlap) currently are in operation
worldwide. Growing numbers of spinning mills, even in low-wage countries, now are opting for
automation in the combing room. The deciding factors are an increase in efficiency of up to 3
percent, more consistent quality and reduced space requirements.
Higher Output, Lower Costs
The new E 65 and E 75 combers offer various advantages that have an immediate impact on
production costs. For a correct comparison of production costs, lower energy consumption and
savings on raw materials and ancillary costs must also be included in the calculation alongside
capital and labor costs. Only then does it become apparent that, compared with other manufacturers,
combers costs per kilogram of combed sliver produced using the E 65 and E 75 combers are lower
thanks to the higher performance of these machines.
In order to ensure Rieter’s product quality, a large number of machines were tested in the
field in continuous operation under a wide range of conditions for several months before the
companys market launch of the new combers commenced. The tests confirmed the significant increase
in productivity and the quality improvements achieved with the new combers.
March 2005