The focus of the textile wet processing technology shown at ITMA 2011 was doing more with less —
processing textiles with less water and energy but with greater productivity than in the past. From
high-efficiency washers to extremely low-liquor-ratio dyeing machines to more energy-efficient
tenter frames, the textile machinery industry is embracing the worldwide trend of wise resource
management. The manufacturers mentioned in this article demonstrate the progress made toward the
goal of high-quality production with minimal resource consumption.
Preparation Equipment
Benninger AG, Switzerland, presented knit processing machinery with a focus on
reduced carbon footprints to reduce the environmental impact of wet processing. Wet-on-wet
mercerizing is said to reduce carbon emissions by 40 percent owing to elimination of a drying step.
The high-efficiency Trikoflex drum washer uses less than half the amount of water compared to
conventional washers. Utilizing a cold pad batch dyeing process with the Benninger Küsters DyePad
can produce 60-percent less carbon emissions compared to exhaust dyeing.
Goller, part of Germany-based
Fong’s Europe GmbH — the European arm of
Fong’s Industries Co. Ltd., Hong Kong — displayed the Sintensa Plus, the latest in
the Sintensa line of preparation equipment for knitted goods. A high level of automation and
precise control of fabric tension provides well-prepared fabrics using less water, energy and
chemicals than in the past.
Italy-based
Sperotto Rimar, part of Santex AG, Switzerland, showed the Nova solvent scouring
system. This continuous system uses perchloroethylene to scour fabrics made with natural and
man-made fibers, with significantly reduced energy consumption compared to conventional aqueous
preparation ranges. No additional chemical auxiliaries are required, and increased productivity is
seen.
Dyeing
Alliance Machines Textiles, France, exhibited several dyeing machines with unique
features. The Rotora Y&F is designed to dye yarn packages and beams of fabric at the same time
in one machine, leading to a claimed 50-percent cost savings over conventional processes. For piece
dyeing, the Riviera Eco Green can dye a variety of woven and tubular or open-width knits at a
liquor ratio of 3:1.
Loris Bellini S.p.A., Italy, known for yarn dyeing and drying expertise,
emphasized several products in this area. The APPC-LV, a pressure cabinet for dyeing yarns in hank
form, combines excellent performance with low water and steam consumption; while the ABP, an
automatic spray-dyeing machine, is designed for delicate yarns on hanks. For yarns in package form,
the RBNO-I for horizontal package-dyeing and the RBNV-I for vertical package dyeing provide
shortened processing times and reduced water and energy usage. After package dyeing, the ARSPV
vertical dryer and the ARSPO horizontal dryer can recover 90 percent of the drying energy to
produce hot water for use in the dyehouse.
Brazzoli S.p.A., Italy, showed several innovative piece-dyeing machines. The
InnoEcology machine is able to dye cotton at a liquor ratio of 3.7:1 with lower liquor ratios
possible for man-made fibers. Fabric speeds can be increased by 50 percent, while nozzle pressures
are reduced by up to 40 percent. Effective dyeing of two fabric strands per tube at a liquor ratio
of 3.5:1 is the premise behind the InnoTwin. Dyeing times and energy consumption can be reduced by
20 percent compared to typical dyeing systems. The unique InnoTech machine uses two conveyor belts
to carry the fabric in the machine, allowing for very delicate fabrics to be dyed at liquor ratios
from 3:1 to 5:1.
Flainox S.r.l., Italy, exhibited garment-dyeing machines that were redesigned to
provide a more sustainable, environmentally friendly dyeing process. In particular, the NRG line
has been ISO 14064- and PASS 2050-certified to have reduced carbon emissions. Not only are the
machines capable of dyeing garments at liquor ratios as low as 4:1, they also use 60-percent less
water, 50-percent less steam, and up to 20-percent less chemicals than other garment-dyeing
machines. In addition, Flainox manufactures its machines in facilities powered by renewable energy
sources.
The phrase “One Stop — Green Innovation” was prominently displayed throughout the ITMA
halls. This phrase was Fong’s message to ITMA attendees that Fong’s machinery on display clearly
had an environmentally friendly focus. The Allwin HT package-dyeing machine can dye a variety of
fiber and blends at a liquor ratio as low as 4:1 with 40-percent less energy and water use and
significantly lower chemical costs than comparable machines. Overall production costs are estimated
to be 30-percent lower. The latest generation of the TEC series of high-pressure, high-temperature
dyeing machines is able to achieve high-quality dyeings of natural, man-made and blended fibers
with reduced energy and water usage.
Gaston Systems Inc., Stanley, N.C., showed an upgrade of its Formula N foam dyeing
system. Up to five foam heads can be used to overdye denim fabric with fiber reactive dyes at a
total 30-percent wet pickup. The system can be configured to treat both sides of the fabric if
desired.
Gofront Holding Ltd., Hong Kong, showed a variety of very low-liquor-ratio
machines. The Excel GF241XL was designed to dye yarn packages with a liquor ratio of 3:1. For piece
dyeing, the Airforce Extreme machine can process fabrics efficiently at a 2.8:1 liquor ratio. The
savings in water, energy and steam are significant.
Lawer S.p.A., Italy, presented an automated color kitchen system that weighs
powder dyestuff with the Supercolor unit and uses the Dyematic unit to dissolve and dispense the
dyestuff to the dyeing machine. The Dos-Chem system is used to dispense auxiliary chemicals to the
dyeing machine.
MCS Officina Meccanica S.p.A., Italy, exhibited a more efficient piece-dyeing
machine. The Dynamica has proprietary pumping and dosing systems and was designed to run at a
liquor ratio of 3.5:1. Both single-rope and multiple-rope versions are available as well as special
models for upholstery and toweling.
Sclavos S.A., Greece, showed the Athena 2 piece-dyeing machine. This machine boasts
very low water and energy consumption along with minimal tension and abrasion.
Then Maschinen, also part of Fong’s Europe, presented several innovative dyeing machines.
The LOTUS (long tube sensitive) machine was developed to dye sensitive fabrics at the extremely low
liquor ratio of 2:1 using Then’s AIRFLOW® technology. The latest iteration of Airflow development
is the Synergy 600G2, which incorporates a self-cleaning filter system that can save significant
processing time. The TDS dyehouse management system can link an automated color kitchen, dye and
chemical dissolving unit, and dispensing system for complete control and reporting functions.
The iMaster H2O dyeing machine shown by
Thies GmbH & Co. KG, Germany, was designed to dye fabrics with minimum tension
at a liquor ratio of 4:1 while reducing total water and energy consumption. Its adjustable internal
walls and Teflon®-lined chamber allow a wide variety of fabrics to be processed successfully. To
provide companies a link between laboratory-scale and full-production machinery, the miniMaster, a
pilot-plant version of the iMaster H2O, was developed. For package dyeing, the eco-bloc quattro
mini-bloc can dye yarns in quantities down to 50 grams. Treatment of rinsing liquor can be carried
out on the dyeing machine with the Advanced Aftertreatment Process (AAP) system that uses active
oxygen to decolorize rinse water before discharge. The hankMaster provides reduced water and energy
consumption for dyeing yarns in hank form.
Printing
Durst Phototechnik AG, Italy, introduced the Kappa 180, an ink-jet printer that
uses the proprietary Quadro print head system to produce printed goods using acid, reactive or
disperse dyes at speeds up to 606 square meters per hour (m2/hr). All important printing parameters
can be monitored remotely using the Durst Advanced Remote Diagnostics (DARD™) system for process
control.
Forbo Siegling GmbH, Germany, showed the Print 6646-2.15E printing blanket. The
blanket was designed with single-ply construction to allow maximum repeat accuracy with rotary
screen printers.
Jakob Müller AG, Switzerland, unveiled the MDP2 MÜPRINT2, an ink-jet printing
system for narrow polyester fabrics measuring 15 to 400 millimeters (mm). Up to 16 rolls at 15-mm
width can be printed simultaneously at a speed of 0.4 meters per minute (m/min).
Stork Prints BV, the Netherlands, introduced a new digital printer. The Sphene,
with new PrinterServer 7 RIP software, can print eight colors on fabrics 1.85 meters wide at speeds
up to 555 m2/hr with 600 dots per inch (dpi) resolution. The newest printer in the Pegasus line,
the Pegasus EVO, was shown with enhanced flexibility and remote diagnostic capabilities. The
digital drive introduced with the EVO can be retrofitted on older printers, offering customers an
opportunity to upgrade equipment at minimum capital cost.
A milestone in printing speed was reached with the Xennia Osiris digital printer from
Xennia Technology, United Kingdom. The Osiris is capable of printing speeds of 30
m/min (3,330 m2/hr) at 144-dpi resolution, providing a low-cost option for both sample lots and
short production runs. For very wide substrates, the Xennia Emerald digital printer can print
material as wide as 3.4 meters at a resolution of 600 dpi with 600-m2/hr speed.
Zimmer Maschinenbau GmbH, Austria, introduced the Colaris printer, touted as the
most economical digital printer available. This printer can print eight colors on fabrics up to 3.2
meters wide ranging from lightweight silk to heavy toweling, and can be joined to an inline
continuous pretreatment range. Printing speeds range up to 1,200 m2/hr depending on the specific
configuration chosen, and resolution up to 720 dpi can be achieved.
Finishing
Arioli S.p.A., Italy, exhibited an atmospheric pressure plasma unit for surface
cleaning and etching, graft polymerization, and thin film deposition. A modified corona discharge
electrode system provides the helium-based plasma in the roll-to-roll lab and production units.
Fabrics can be treated in 2.4-meter width at 25 m/min.
Brückner Trockentechnik GmbH & Co. KG, Germany, introduced several additions
to its Techno-Line coating line. New applicators were shown that allow simultaneous coating of
bi-elastic knitted fabrics on upper and lower sides of the fabric inline with a tenter frame.
Erhardt + Leimer GmbH, Germany, showed several useful tenter frame add-ons. The
ELCut BTA 80 trims the glued edges of fabric at the tenter exit and suctions away the trim
automatically. The ELCount system uses high-resolution cameras to automatically measure the pick
count of fabric as it enters and exits the tenter. Fabric temperature and residual moisture as well
as exhaust moisture and tenter temperature can all be monitored with the ELMat system.
Fibroline, France, presented its D-Preg™ dry powder impregnation system for
composites and technical textiles. Dry thermosetting, thermoplastic or functional powders are
imbedded in the textile with the aid of a high-voltage electric field. Further thermal processing
produces the final finished textile without the need for water or solvent evaporation.
Kusters Calico Machinery Ltd., India, exhibited the TwinNip, a new padder for
wet-on-wet finishing. The compact padder has a low footprint for reduced space requirements and can
be used as both a double- and single-dip padder. An S-Roll is employed to provide the maximum
dewatering of incoming wet fabric.
Mahlo GmbH & Co. KG, Germany, displayed the Orthopac CRVMC-12, a
web-straightening system featuring a patented concept that automatically measures the web and
adjusts the drives to maintain the input parameters. The system can process a wide range of fabrics
from carpets to technical textiles.
A. Monforts Textilmaschinen GmbH & Co. KG, Germany, offered several new or
improved products for fabric finishing. The redesigned Montex 8000 tenter frame has improved air
flow to reduce chemical or dye migration during drying, as well as the Eco Booster HRC that uses
exhaust air to heat incoming air. The Matex Eco-applicator is a kiss roll chemical applicator for
wet-on-dry or wet-on-wet finishing that can treat both sides of a fabric with minimum wet pickup
while automatically adjusting the kiss rolls to maintain the desired wet pickup. The redesigned
Monfortex 8000 provides compressive shrinkage to fabric at 20-percent-higher speeds with
40-percent-less water usage and 20-percent-longer belt life.
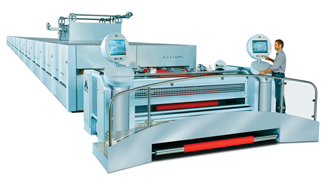
Monforts’ redesignedMontex 8000 tenter frame offers improved air flow to reduce chemical or dye
migration during drying.
Morrison Textile Machinery Co., Fort Lawn, S.C., exhibited a closed-loop Sanfor
machine, the SanforTROL™. This compressive-shrinkage machine measures shrinkage continuously
online, and controls temperature and moisture levels to automatically maintain the desired
shrinkage within set parameters.
Oerlikon Textile Components GmbH, Germany, highlighted an improved belt for
compressive shrinkage. The Daytex® Shrinkage Belt is seamless and has unique curved edges to
increase belt life significantly.
Ontec, Germany, showed a complete line of coating systems. Coating units are
available for offline coating as well as coaters that mount directly on warp knit or looms.
Cintex-Pleva, Switzerland, offered the ECO-OPTIDRY® controller for drying and
heat-setting processes. Actual energy consumption is calculated in real time and displayed for use
in process optimization. Energy savings of 30 percent can be realized.
Santex introduced three innovative products. The ESC-Energy Saving Chamber is an
additional drying zone that when installed on an existing tenter frame utilizes the heat of exhaust
air to increase dryer capacity by 15 percent. A new coating/laminating machine, the Cavi 2 Coat, is
designed to coat substrates with any of four different coating heads for hotmelt applications. The
Synpact compacting machine combines a rubber belt shrinkage unit with a felt blanket shrinkage unit
to yield a process that offers twice the speed realized on traditional felt shrinkage machines.
Stalam S.p.A., Italy, exhibited the RF 180 kW dryer. This radio-frequency dryer for
yarn packages has the capacity to dry more than 9 tons per day of cotton yarn.
The X-treme XEB shown by
Xetma Vollenweider AG, Switzerland, is a new brushing, sueding and emerizing
machine with higher speed — 100 m/min — and greater energy input to provide higher productivity. A
unique quick-change system allows rapid replacement of components. The new X-plore XCS shears
carpets up to 6 meters wide with special heavy-duty units.
Zimmer’s Triplexcoat machine can coat fabric with either knife-over-air, knife-over-roll, or
rotary screen technologies. In addition, slot nozzle and foam coating options are available.
Substrates up to 3.4 meters wide can be accommodated at speeds up to 100 m/min.
November/December 2011