Researchers at Fiber Innovation Technology and MMT Textiles engineered a fiber that can curl and uncurl reversibly in response to humidity in the environment.
By Jeff Dugan
In recent years, there has been increasing use of the biomimesis concept in product design, and textile products are among the best-known examples of where this concept is employed. Biomimesis is simply the adaptation of solutions found in nature to solve related problems in the design of man-made products.
Perhaps the best-known example is the hook-and-loop fastener technology popularized by Velcro®-brand products. The hook-and-loop fastener mimics the barbed bristles of certain seed pods that are so adept at hitching a ride on the fur of a passing animal or the pants legs of humans hiking through the brush. Speedo’s LZR swimsuits, made famous in Beijing during the Olympics, seek to mimic the micro-roughness of a shark’s skin to reduce drag. More recently, nanotechnology fabric coatings have mimicked the surface morphology of the lotus leaf, giving rise to the “lotus effect” water-repellence and self-cleaning abilities. And yet to come are potential adhesive surfaces designed to mimic the toes of a gecko, which can climb vertical surfaces because of the fine surface features of its toes.
Pinecone Effect
The natural phenomenon mimicked by Inotek™ products — a fiber and fabric concept conceived by Dr. Veronica Kapsali, technical director of London-based MMT Textiles Ltd.; with fibers developed by Johnson City, Tenn.-based Fiber Innovation Technology Inc. (FIT) — is known as the “pinecone effect” (See Figure 1). In nature, pinecone scales hold the seeds tightly within the folds when the environment is humid. But in dry air, a part of the scale shrinks, causing the scales to open up and release the seeds. Probably not coincidentally, it turns out that dry conditions are more beneficial to pine seed scattering than wet conditions.
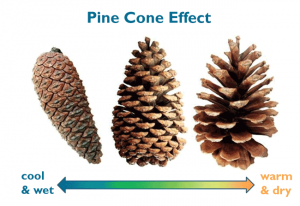
Similarly, fabrics featuring Inotek fibers are engineered to spontaneously and reversibly change their structure depending on the humidity in their immediate environment. At low humidity, there is no need for accelerated vapor transport, and thermal insulation is desirable. Under these conditions, the pores between yarns in the Inotek fabric are conventionally sized, comparable to standard knit or woven fabrics. If the wearer begins to sweat though, even in the early stages before sweat becomes noticeable, the humidity in the fabric increases. As humidity increases, Inotek yarns spontaneously contract, providing larger openings between the yarns and facilitating increased vapor transport through the fabric (See Figure 6). Thus, the body’s natural evaporative cooling is facilitated, rather than frustrated, by the garment.
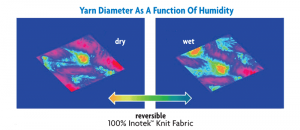
The fabric’s adaptability is enabled by the structure of the fiber from which the yarns are made. It is a bicomponent fiber with an eccentric sheath/core cross-section, which causes the fiber to reversibly curl and uncurl in response to humidity.
Sheath/Core Fibers
Eccentric sheath/core fibers have been used for some time in applications that use heat to cause the fibers to curl. A conventional concentric sheath/core fiber will shrink if heated above the polymer’s glass-transition temperature. The two polymers have different natural shrinkage rates, but the polymer with the higher shrinkage will only shrink as much as is allowed by the lower-shrinkage polymer because the fiber cross-section is concentric, and the higher-shrinking polymer cannot compress the lower-shrinking polymer.
But in an eccentric sheath/core configuration, the force generated by the higher-shrinking polymer is not equally balanced by the lower-shrinking polymer, so the forces are resolved by the curling of the fiber into a helical shape. This functionality is useful in a number of applications, but it is not a reversible process. That is, once heat is applied and the fiber curls into a helix, a subsequent return to lower temperatures does not cause the fiber to uncurl.
Unlike these thermally-curled fibers, the Inotek fiber responds to humidity rather than temperature, and its curling is reversible, repeatedly curling as humidity increases and uncurling as it decreases. Spun into a yarn, the curling action causes the yarn to contract to a smaller diameter, which opens larger pores between the yarns in a fabric.
In the thermally curled example, the curl comes from differences in shrinkage between the two polymers. In the Inotek fibers, curl results from a difference in swelling caused by differences in moisture uptake — commonly known as regain. The fiber’s core is polypropylene (PP), which has virtually no moisture regain even under high humidity conditions. The sheath is made using nylon 6, which has a moisture regain that is dependent on humidity, with a maximum of 4.5 percent by weight at a relative humidity of 98 percent. As the nylon absorbs water, the polymer expands. Only a relatively small expansion, in absolute terms, produces the stresses necessary to cause the fiber to curl.
Fiber-Development Process
The tighter the curl in the fiber, the greater the observed effect in the fabric. Therefore, during the fiber’s development a good deal of effort focused on how to optimize the amount of curl that the fiber would produce.
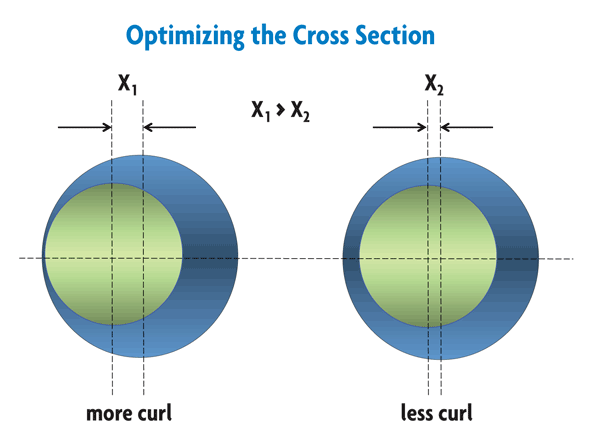
The degree of curl is most strongly influenced by the distance separating the centers of mass of the two polymers (See Figure 2). So the highest degree of curl is produced not by an eccentric sheath/core cross-section, but by a side-by-side cross-section. However, a side-by-side cross-section was not an option for the Inotek fiber because in the side-by-side cross-section, the two polymers have only the adhesion between the two polymers at their interface to maintain their unity as a single fiber, which is required to achieve curling. Unfortunately, nylon and PP do not adhere well, and the stresses resulting from the swelling of the nylon are sufficient to split the two polymers into separate fibers, thereby destroying the forces that produce the curl. Beyond destroying the curl, if the two components separate prior to carding and yarn spinning, it also may not be possible to efficiently convert the fiber into a yarn.
So while a sheath/core fiber cannot achieve as great a distance between the two components’ centers of mass, it does offer the advantage of physically encapsulating the PP within the nylon, thereby preventing fatal delamination. Then within the constraints of the sheath/core cross-section the next design consideration was how to maximize the degree of eccentricity. Pushing the core too far to one side of the cross-section however risked breaching the outer wall of the sheath at its thinnest point, giving rise again to delamination of the sheath from the core. FIT researchers needed to find a way to push the core as far off-center as possible, without creating a section of sheath so thin that eruption of the core from the sheath was favored.
Examining the fiber cross-section after extrusion, it was possible with some cross-sections to observe fibers with a vanishingly thin sheath section, or even a minor breach of the sheath by the core that nevertheless appeared to be fully unitary with little incidence of delamination. But there is a good deal of physical agitation downstream from extrusion including mechanical crimping, carding, yarn spinning, knitting or weaving, and even laundering and repeated curling and uncurling in the garment. These forces exacerbate the tendency toward delamination, if the “retaining wall” of the thinnest part of the sheath is too thin.
In seeking to optimize the cross-section, the first option FIT explored was, of course, the easiest — it made fibers with smaller cores. While the center of the core remains in place, and its separation from the center of the sheath is maintained, the reduced diameter means that the thickness of the retaining wall is increased. However, testing revealed that the curling performance of these fibers was reduced. FIT researchers continued to work to find a way to keep the retaining wall in place, while maximizing the separation of the polymers’ centers of mass without reducing the total mass of the core. This structure required some highly challenging modifications to the shape of the PP core.
Fortunately, FIT has an exceptional capability to achieve very subtle and precise changes in bicomponent cross-sections, and the company was able to improve both the curling performance of the fiber and its resistance to delamination.

Employing precise control of the cross-section, FIT evaluated fibers with an elliptical core (See Figure 3). Converting the core’s cross-section from a circle to an ellipse offers a way to move more of the mass of the core farther from the fiber’s center without breaching the sheath. In this evaluation, though, the company discovered that while an elliptical core was an improvement over a circular one, nevertheless there still were a couple of points at which the outer edge of the ellipse did not conform well enough to the circular outer edge of the fiber resulting in “pinch points” where the sheath was dangerously thin.
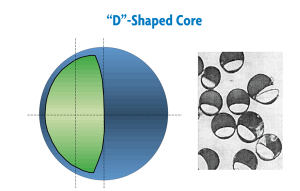
FIT sought to overcome these pinch points with a nominally D-shaped core, with a nominally circular outer edge (See Figure 4). This configuration did a good job of maintaining a sheath of constant thickness along its thinnest section. The core in this fiber had an opposite edge that was nominally flat, which maximized the separation of the centers of mass of the polymers. However, the relatively sharp corners where the shape transitioned from circular to straight resulted in tear points where abrasive forces could concentrate and cause breaches in the sheath at those points.
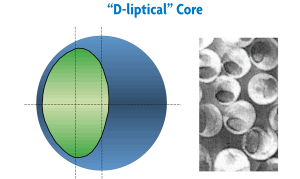
Finally, FIT made a small compromise with regard to the separation of the centers of mass, by rounding out the corners and relatively flat edge of the D-shaped core. The result was a core with an outer edge that is circular, but which curves gently away to transition to an elliptical inner edge. This shape could be called a “D-liptical” cross-section (See Figure 5). This cross-section produces a high degree of reversible curl that is a function of humidity, and survives downstream processing without delamination problems.
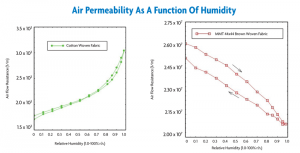
Fabrics made from these fibers exhibit adaptive breathability, with significant changes in open pore area and corresponding changes in fabric air permeability as a function of humidity.
Editor’s Note: Jeff Dugan is vice president of research at Johnson City, Tenn.-based Fiber Innovation Technology (FIT). This article is based on Dugan’s presentation given at the 2015 Textile World Innovation Forum.
July/August 2016