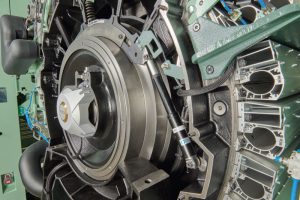
Rieter’s new C 81 carding machine features intelligent sensors for enhanced production and quality.
TW Special Report
With high production rates and excellent sliver quality, Rieter reports its new card C 81 gives spinning mills a strong position in the market. Intelligent sensors — which set the carding gap to the ideal size and monitor the trash level in real time — make this high production rate and quality possible.
The high-performance and innovative card C 81 offers new, intelligent functions in addition to maximum productivity and minimum energy consumption. State-of-the-art sensor technology controls the carding gap (see Figure 1) and monitors the quality of the raw material before and after the carding process. This increases quality and production compared to Rieter’s previous model C 80.
Ten-Percent Higher Productivity Thanks To Carding Gap Control
The carding gap is what determines the carding quality. The more precisely the gap can be adjusted, the better the reduction of neps and the associated yarn quality. The C 81 can inspect the carding gap without contact. Carding Gap Control regulates the carding gap — the distance between the flat and the cylinder — accurately to a few hundredths of a millimeter.
On each of the 116 flats in use, the system detects the distance between the needle tips and the cylinder clothing and monitors this without contact. Intelligent software calculates the ideal carding gap by factoring in further important influencing variables, such as the machine temperature. The electronic, centrally adjustable flat setting constantly keeps this gap in the ideal range.
Comparisons with and without the regulated carding gap have shown an increase in production of Figure 1: Automatic adjustment of the carding gap up to 10 percent while maintaining the same quality level. This produces a card sliver quality that is up to 10-percent better at the same production speed, which means fewer thin places, thick places and neps. Carding Gap Control also has the advantages of higher machine availability and consistent quality, depending on the individually defined limit values. The Rieter card C 80 can easily be retrofitted with this new function.
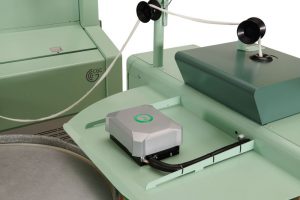
Artificial Intelligence Improves Raw Material Yield
Another innovation of the C 81 is Trash Level Monitor, which continuously monitors the contaminant content of the fiber tufts in the card inlet and the card sliver produced. This is important for customers who process natural fibers, such as cotton. The heart of this function is optical image processing with a new neural net-work developed by Rieter. Sensors in the card infeed and at the sliver coiling section deliver the data for this (See Figure 2).
Trash Level Monitor makes yarn quality predictable within a defined range. Artificial intelligence is used to determine whether the impurities in the card infeed and in the produced card sliver lie within the defined limit value. This makes it possible to take measures to make sure that the raw material is used ideally, even at this early stage of the process. Trash Level Monitor is also available in a modular version and can be retrofitted into existing Rieter carding systems.
July/August 2023