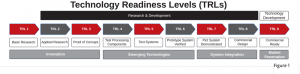
The Nonwovens Institute’s success is driven by creating measurable goals in-line with a long-term vision.
TW Special Report
Technology Readiness Level (TRL) is a measurement system developed by the National Aeronautics and Space Administration (NASA) in the 1970s to manage the process of translating fundamental knowledge into technology ready for deployment. In NASA’s case, the goal was to use TRL to enable the development of “flight-proven” technology ready to stand up to the challenges of space travel. TRL has also been employed by industry to evaluate the maturity of a technology or invention as it progresses along the tortuous path toward commercialization.
A comprehensive description of TRL is one recently articulated by the U.S. Department of Energy (See Figure 1).
The Nonwovens Institute (NWI), based on the Centennial Campus of North Carolina State University in Raleigh, N.C., has leveraged the TRL system to shape its pillar service offerings with the aim of providing value to the entire nonwovens industry value chain.
While university-based programs have historically focused on basic research problems (TRL 1-2), NWI is unique in that it focuses on the full TRL range (TRL 1-9), facilitating collaboration among industry, government, and academia to enable the development of next-generation nonwoven solutions to mission-critical challenges.
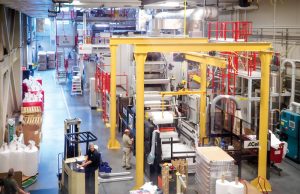
NWI Background And History
NWI is the world’s first accredited academic program for the interdisciplinary study of engineered fabrics. NWI works with experts from industry, government, and academia to facilitate experimental trials and engage in problem-solving for nonwovens-relevant applications, while also providing hands-on training and guidance to the field’s future leaders and industry professionals.
NWI traces its history back to 1991 when the Nonwovens Cooperative Research Center (NCRC) was established at NC State University as a State/Industry-University Cooperative Research Center (IUCRC) with matching grants from the National Science Foundation (NSF), the State of North Carolina, and several industry partners. NCRC was one of the first five State/IUCRC’s funded by NSF, which would contribute more than $2 million over nine years to the Institute.
In 1999, NCRC graduated from NSF and became self-sustaining. NCRC transitioned into The Nonwovens Institute in 2007, establishing the Institute as a university-wide activity that touches at least three colleges and more than seven departments. NWI continued to grow its capability to collaborate with industry and government research agencies to deliver relevant results. NWI’s success is the product of its diligent attention to understanding the needs of the industry and developing the five pillars of NWI’s capability to meet those needs. NWI’s pillar focus areas range from fundamental, pre-competitive research through to technology commercialization.
NWI’s Pillar Areas Of Emphasis
Pillar 1: Knowledge Creation —NWI views education, research, and outreach as critical components of its mission. Pre-competitive research conducted as part of NWI’s Knowledge Creation pillar initiative falls in the TRL 1-3 categories and is often described as “core projects.” These research activities engage the Institute’s network of faculty and students and are a means by which NWI trains the future leaders of the nonwovens and affiliated industries. Graduate students who participate in the NWI research program are equipped with the knowledge required to succeed in the corporate environment, while the results of NWI research projects enable NWI member companies to innovate by finding solutions to grand challenges in nonwovens-relevant subject matter areas.
Pillar 2: Knowledge Transfer/Workforce Development — NWI leverages the insight gained from its Knowledge Creation pillar initiative to inform its extensive array of training content. These training programs are formalized into various course offerings, with regularly scheduled in-person short courses, presented in partnership with INDA, The Association of the Nonwoven Fabrics Industry, custom courses and online training modules available to meet the professional development needs of the industry. NWI’s Workforce Development pillar initiative covers TRL 4-9, with course content ranging from material characterization and testing to product development and commercialization.
Pillar 3: Fabrication and Testing— NWI has continued to build and update its facilities since 2000, and today has the most extensive set of lab- and large pilot-scale nonwoven production equipment found any-where in the world. NWI’s Fabrication and Testing pillar initiative (TRL 3-6) plays a key role in the development and transformation of the latest innovations into marketable fiber-based systems ready for shipment to commercial, consumer, and industrial users around the world. NWI’s facilities include lab-scale systems dedicated to polymer characterization, fiber extrusion, and meltblown, with large pilot facilities for bicomponent spunbond and meltblown, staple fiber, fiber spinning, needlepunching, hydroentangling, thermal bonding, and web composite capability. Analytical and filtration testing facilities offer the ability to analyze and evaluate material performance according to a wide range of industry-specific standard test methods.
Pillar 4: Problem Solving — NWI’s Problem Solving pillar initiative is rooted in sponsored research that is funded by industry or government agencies. The work performed in this area of NWI’s service offering is confidential to the sponsors and provides an option to license any intellectual property (IP) generated using a standard joint development agreement (JDA).
NWI conducts activities in the Problem Solving area utilizing the stage-gate development process (TRL 4-6) with a focus on bridging sponsors from innovation development to practical demonstration and the reduction of engineering risk — the so-called developmental “valley of death.” Working hand-in-hand with NWI’s in-house production, testing, and product development team —who bring decades of experience in the full range of nonwovens production processes and test methods — sponsors can elevate exciting new discoveries relevant to nonwovens.
Pillar 5: Product Incubation — In the Product Incubation pillar area, NWI has created a non-profit affiliate entity of NC State University called Leaders in Nonwoven Commercialization (LINC LLC). LINC helps commercialize new products and technologies with manufacturing capability, specializing in small-to-medium scale production runs. In parallel, LINC works with companies to establish long-term supply chains and transfer the technology to sup-port their ongoing operation. In this way, attention is focused on TRL 7-9— effectively bridging the valley of death and validating market acceptance for new products. LINC adheres to the highest standards of quality under NWI’s Quality Management System.
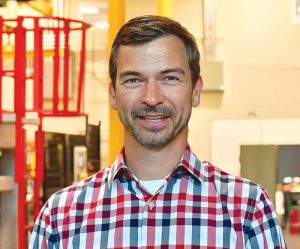
NWI Positions For A Bright Future: Raoul Farer Joins NWI
Aligning with NWI’s plans for growth going forward, the Institute recently announced the appointment of Dr. Raoul Farer to the role of executive deputy director.
Farer, who will also serve as a professor in NC State’s Wilson College of Textiles’ Department of Textile Engineering, Chemistry and Science (TECS), joins the Institute’s leadership team and will work closely with NWI’s Executive Director Dr. Behnam Pourdeyhimi and Operations Director Tom Daugherty to manage the implementation of NWI’s strategic vision.
Farer comes to NWI and NC State following a 24-year career with Freudenberg Performance Materials with various assignments in Ger-many, Spain and the United States. Farer brings extensive knowledge in textile technologies with a specialization in nonwovens.
He earned his Master of Science in Textile Management and Technology in 1996 and a doctorate in Fiber and Polymer Science in 1999 from NC State. Farer also participated in NWI’s fundamental nonwovens research program as a student, studying novel dispersion technologies for wet-laid nonwovens and the formation of 3D meltblown structures via a robotic system.
During his tenure at Freudenberg Performance Materials, Farer also served on NWI’s Industrial Advisory Board (IAB), most recently as chair of its Executive Committee (2022-2024).
“Having worked with Raoul from the time he was a student researcher at NC State and watching him progress in his career with Freudenberg Performance Materials, I am thrilled to have him join us here at NWI,” Pourdeyhimi said. “I look forward to working with Raoul once again and seeing NWI continue to grow with the benefit of his contributions.”
“Returning to my alma mater and NWI is a dream come true,” Farer said. “After a long career in industry at one of the world’s leading nonwoven manufacturers, I couldn’t be more excited about the opportunity to give back to the students, NWI, the Wilson College of Textiles, and NC State. Nonwovens have been my passion from the moment when I first took an introductory course as an undergraduate student. I feel very fortunate to be able to join the teams at NWI and TECS and look forward to helping our students learn and grow in their journeys toward becoming future researchers and innovators and to further strengthening our industry partnerships to help build the NWI of the future.”
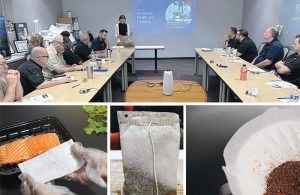
NWI Pursues Food Packaging Safety Certification
NWI continues to build upon its strong foundation of quality-based manufacturing practices by pursuing the Brand Reputation Compliance Global Standard (BRCGS) Certification for Packaging Materials, which is recognized under the Global Food Safety Initiative (GFSI). NWI is on schedule to complete this certification process in 2024, enabling the Institute to meet the needs of producers of nonwovens for food packaging.
NWI has been following good manufacturing practices (GMP) requirements since 2019, and its most recent audit resulted in a rating of “Excellent” with a score of 962/1000, according to an independent third-party auditor. NWI’s Analytical, Filtration Testing, Spunbond and Hydroentangling, and Meltblown labs are all ISO 9001:2015 accredited.
“Here at NWI we are continuously striving to improve our quality measures,” said Jamie Plummer, lab research specialist. “Over the past several years, we’ve implemented a full suite of standard operating procedures, not only in our labs, but across all our operations. Our goal with BRCGS Packaging Materials Certification is to align our business with GFSI to meet the needs of our current and prospective customers who are serving the food and beverage industry.”
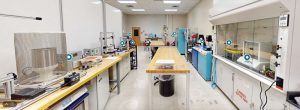
NWI Introduces Expanded Filtration Testing Lab
NWI also recently announced its newly expanded Filtration Testing Lab, featuring services for facemasks and respirators, along with filter media for automotive, HEPA, and HVAC applications, among others. Importantly, NWI’s Filtration Testing Lab is outfitted with equipment to perform ASTM F2299 testing for the measurement of Particle Filtration Efficiency (PFE) at 0.1 microns.
Testing equipment available in NWI’s Filtration Testing Lab includes:
• PALAS MFP-3000-S fractional aerosol filter test;
• Two TSI 8130 machines for filtration efficiency;
• Two TSI 3160 machines for filtration efficiency;
• Two offline charging and discharging units;
• Two environmental chambers for aging and conditioning masks and filter media;
• TSI Portacount respirator fit tester;
• Testex TN 139 synthetic blood tester;
• Testing apparatus for the measurement of fluid resistance for surgical masks; and
• Prototyping facility to produce masks per NIOSH Standard Test Protocol.
NWI’s Filtration Testing Lab is managed by Amy Minton, who has more than 20 years of experience in administering a wide variety of analytical, physical, and filtration test methods for nonwoven materials.
“NWI’s Filtration Testing Lab is an important addition to the Institute’s impressive nonwoven fabrication and testing capabilities,” said Minton, who also manages the NWI Analytical and Physical Testing Lab. “Our decades of testing experience and our strict adherence to GMP and Standard Operating Procedures provide our industry partners assurance that the tests they conduct at NWI will be executed with the highest level of quality and accuracy.”
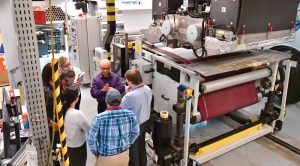
NWI, INDA Sign Collaboration Agreement on Training Programs
NWI recently announced a collaboration agreement with INDA, the Association of the Nonwoven Fabrics Industry, to provide continuing education to the nonwoven industry. This agreement expands upon the ongoing partnership between INDA and NWI, whereby the two organizations have successfully presented training programs, covering the full spectrum of the nonwovens value chain from raw materials to processes to products.
Under the terms of the agreement, INDA and NWI will develop and present a full roster of training courses, featuring a combination of classroom learning supported by hands-on activities in NWI’s world-class nonwoven production and testing labs.
“As we enter into this new phase of our partnership, NWI and INDA are excited to leverage our diverse perspectives and industry contacts to create an unmatched training and education program,” Daugherty said. “This will ensure the nonwoven industry remains competitive and is equipped with the latest skills. With the pace of change in our industry heightened due to the rapid rise of such megatrends as sustainability and machine learning, we believe continuing education in nonwovens is more important than ever — and NWI and INDA are well positioned to serve the needs of our industry in this regard.”
The Future
“The Nonwovens Institute is the most successful non-medical research institute that began with NSF funding based on longevity and research, education, and industry service impact,” Pourdeyhimi said. “This success is driven by creating measurable goals that are consistent with NC State and NWI’s long-term vision.
“As we’ve recently completed our ‘2030 Strategic Plan,’ we have set ambitious targets in each of our pillar service areas, and we are already making positive strides toward these goals,” Pourdeyhimi continued. “We look forward to continuing to serve nonwovens-affiliated organizations, with high-value offerings that touch on the full range of our industry’s needs from fundamental understanding to technology commercialization.”
2024 Quarterly Issue IV