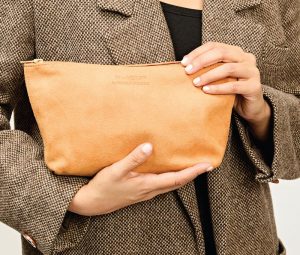
Under intense scrutiny for its ecological footprint, the textile industry is developing ways to combine material science and existing manufacturing processes to pave the way for a more sustainable future.
By Dr. David Williamson
For nearly as long as humans have lived, they have dyed materials. Early craftsmen discovered that natural dyes found in the bodies of insects, mollusks and plants could be isolated and used to transform common textiles into culturally defining works of art. Tyrian purple, for example, was so difficult and costly to produce that few in the ancient world could afford it, and so the color purple became an iconic symbol of Roman royalty. To this day, the significance of color as a medium for personal and cultural expression has not faded. Whether it’s the deep indigo of Japanese textiles or the vibrant reds of ancient Peruvian fabrics, color tells stories — of status, geography, and tradition — that words often cannot.
What began as a niche art has since evolved into a multi-billion-dollar global industry. Modern dyeing practices, powered by synthetic chemicals and large-scale production facilities, allow manufacturers to dye materials at a rate and scale unimaginable to the dyers of antiquity. Yet, this growth has come at a significant environmental cost. The global textile industry is now under intense scrutiny for its ecological footprint. The apparel and footwear sectors alone are responsible for up to 8 percent of the world’s greenhouse gas (GHG) emissions and significant amounts of water used and effluent produced, creating stress on regions given how water is already a diminishing resource. The demand for color has become entangled with some of the most pressing sustain-ability challenges of our time.
Next-generation materials have emerged as a potential solution for the industry. These advanced materials, many created through biomanufacturing, are designed to both reduce the environmental cost of textile production and decrease contribution to landfills. Though there are many exciting applications for next-generation materials, one noteworthy opportunity lies in leather production, where there is opportunity to reduce its environmental footprint and not many alternate solutions exist.
The leather tanning process relies heavily on water- and chemical-intensive processes to achieve the richly dyed hides that are so often associated with luxury. Consumer demand for animal-free, responsibly produced leather has steadily risen, causing many to look to next-generation materials. However, leather is an ancient material that has been crafted by artisans for millennia. The material’s charm comes not from its resilience and water-resistant properties, but from its distinct look and feel.
A viable alternative to leather will thus have to be more than just ecologically friendly, it will have to inspire reverence among consumers, becoming a material that’s worth showing off. Next-generation materials have largely failed to achieve this, in part because the look of leather is so hard to replicate. But where others have failed, Modern Meadow is poised to succeed. Using a protein-based material known as Bio-Alloy® as a starting point, Modern Meadow has developed a leather-like material that not only matches many of leather’s tensile properties but allows tanners to tell their ancient and colorful stories on a new canvas.
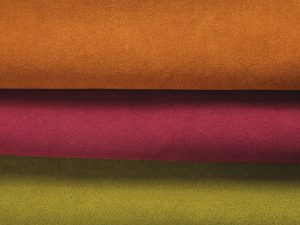
Dyeing: A Dance Between Proteins and Pigments
To appreciate the significance of Bio-Alloy, it’s important to first understand how leather gets its color. The final color of any material is determined by many factors, including the quantity and arrangement of dye molecules that have bound the material, as well as the overall structure of the material.
Leather is rich in type 1 collagen proteins, which provide a unique canvas for dye binding. Collagen’s triple-helix structure, along with the various functional groups present on its amino acid backbone, create ample opportunities for interaction between dye and protein. If this interaction is strong, the dye molecules will be retained in the material and contribute to its final color.
The fastness of the material’s color depends on how the dye-protein interaction is formed, with the strongest occurring through covalent bonds. While leather can be dyed with most types of dye, it is typically done using acid dyes, which carry a net negative charge and are attracted to the positive charge of collagen fibers. This electrostatic force causes the dyes to penetrate far into the material creating an ionic bond and enabling a deep, rich color to be achieved.
This process is a delicate one that requires careful consideration from start to finish. How the hide is treated from the moment it’s received can affect the collagen’s structure and charge, as well as the hide’s permeability — all of which can affect the dye-collagen interaction and subsequent color of the hide. Similarly, contamination of tanning reagents by chelated metals in factory pipes can greatly affect dye properties. Therefore, the quality of the dyeing process — and by extension, the leather — depends on a meticulously designed tanning and post-tanning process.
Enter Next-Generation Materials
In recent years, the textile industry has sought alternative materials that can rival natural leather in performance while improving on its environmental impact. These next-generation materials, often made from bio-based or synthetic components, are designed to minimize animal, water and chemical usage during production. However, creating a truly viable leather alternative is no simple task.
One of the biggest challenges is replicating the structure and look of natural leather. The complex collagen matrix in animal hides doesn’t just dictate how dyes bind to the material; it also affects properties like breathability, water permeability and resilience. To be commercially successful, any alternative material must match or exceed these qualities while achieving the rich look of leather. Simply put, leather’s value is more than skin-deep — it’s a product of its structure.
Many leather-like materials are constructed using synthetic fibers, which possess chemical properties very different from those of collagen. To achieve the desired color, such materials would have to be treated with a significantly different dyeing process that may not be compatible with tannery infrastructure. The infrastructure for dyeing and processing leather has been optimized over centuries, with significant investments in equipment and processes. Introducing a material that requires bespoke manufacturing workflows can be prohibitively expensive for manufacturers, leading to slow market adoption. This has been a stumbling block for many synthetic leather alternatives, which, despite their promise, have failed to penetrate the market on a large scale.
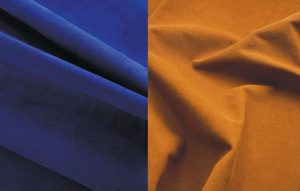
Modern Meadow’s Bio-Alloy: A Game-Changer
This is where Modern Meadow’s Bio-Alloy technology comes in.
Bio-Alloy has a molecular blend composed of biopolymers and plant-derived proteins. Modern Meadow has explicitly designed Bio-Alloy to contain a soy protein blend that is enriched with dye-binding sites, enabling the materials that contain Bio-Alloy to achieve deep and fast color properties.
To emulate leather, Bio-Alloy is combined with a nylon meshwork formed from upcycled rubber and consumer waste. The structure provided by the nylon, combined with the protein matrix of Bio-Alloy results in a remarkably hide-like material, known as BIO-VERA® that can be seamlessly dropped into leather tanning workflows at the dyeing stage.
BIO-VERA offers several advantages for tanneries looking to develop a leather alternative.
Firstly, the material is produced without livestock which greatly reduces the amount of GHG emissions associated with material production. Preliminary life cycle assessment studies show significant reductions in green-house gas emissions with approximately 7 kilograms of carbon dioxide equivalents per square meter of material. Additionally, BIO-VERA is drop-in ready, meaning no bespoke infrastructure is needed — it can simply integrate into existing tannery workflows. Notably, because BIO-VERA does not need to be delimed or tanned, it also requires at least 90 percent less water than natural hides.
As discussed, look is a critical feature of leather. BIO-VERA is capable of achieving a highly-leather-like look and feel thanks in large part to Bio-Alloy, whose protein composition is akin to that of leather’s. This means that BIO-VERA can be dyed using the same acid dyes that work on leather. However, BIO-VERA has also been designed to offer a wider range of dye options for tanners. For example, now it can also be dyed using reactive dyes, bringing an entirely new color palette to the leather industry or the bronze metallic sheen that comes with basic dyes.
Put another way, the availability of different binding chemistries in Bio-Alloy opens up a new level of design flexibility for tanners using BIO-VERA.
A Sustainable Future For Leather Dyeing
The leather industry is at a crossroads. On one hand, the demand for sustainable practices is undeniable. On the other, the challenge of developing a viable leather alternative has proven elusive — until now. With BIO-VERA and its underlying Bio-Alloy technology, Modern Meadow has developed a material that not only addresses the environmental concerns of traditional leather but also meets or exceeds its performance characteristics. By enabling manufacturers to use traditional dyeing techniques, while also opening the door to new possibilities, Bio-Alloy represents a breakthrough in the field of next-generation materials.
As the textile industry continues to evolve, innovations like Bio-Alloy are paving the way for a more sustainable future. By combining the best of both worlds — advanced material science and compatibility with existing manufacturing processes — Modern Meadow’s protein-based technology is set to make a lasting impact on the world of leather dyeing.
Editor’s Note: Dr. David Williamson is CEO of Nutley, N.J.-based sustainable materials company Modern Meadow.
2024 Quarterly Issue IV