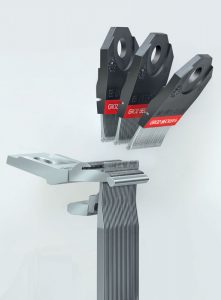
The Groz-Beckert Knitting division produces and distributes more than 50,000 products for the fields of circular knitting, legwear, flat knitting, and warp knitting. Besides high-performance needles and system parts for all kinds of knitting machines, the product range also includes knitting cylinders for large-diameter circular and seamless bodysize machines.
TW Special Report
The clicking sound of knitting needles might be part of some readers’ childhood memories of their grandma making socks. Today, instead of nimble fingers there is a wide range of machines taking over the task of knitting socks and other sophisticated fabrics.
Circular Knitting
Single and double cylinder machines as well as single cylinder machines with dial have become standard for legwear. Transfer techniques used on single cylinder machines with dial additionally allow to produce a variety of patterns. These machines are offered with typical diameters from 3.5 to 6 inches, whereby depending on the gauge, needles with a thickness from 0.26 millimeters (mm) to 1.55 mm are employed. Groz-Beckert offers a range of more than 1,800 high quality needles for socks, hosiery and small diameter circular knitting machines.
Typical application fields in large-diameter circular knitting include the manufacture of outerwear such as T-shirts, leisure and sportswear, underwear and sleepwear, among them bra fabrics, and technical textiles such as smart shirts. These knitted fabrics are manufactured as endless tubular fabric by a circular array of knitting needles. In double-jersey machines, needles are arranged in both the cylinder and the dial, while single-jersey machines use knitting machine needles as well as sinkers. Knitting technologies only show to advantage with quality components in place. That’s why knitters and machine builders like to partner with Groz-Beckert, an industrial machine needle provider. At Groz-Beckert, all the components of a knitting system are precisely inter-coordinated. The perfect interaction between knitting machine needles and system parts guarantees an even, flawless loop formation process.
Warp Knitting
Uniform and flawless quality is a must — and a challenge — in warp knitting. Extreme loads in the loop forming process due to mechanical and chemical influences cause premature wear and rust. The causal factor of particularly pronounced forms of wear are usually abrasive yarns. In the case of natural fiber yarns, these are typically contaminants that are harder than steel, and in chemical fiber yarns, which are treated to induce matting, the culprits are titanium dioxide crystals protruding from the yarn surface and literally sawing into the steel. At Groz-Beckert all components of a warp knitting system are wear and rust protected as well as precisely coordinated with one another. The perfect interaction of needles and system parts guarantees a uniform and flawless warp knitting process.
Apart from high-performance needles, for the warp knitting industry the company also offers system parts for tricot, stitch bonding, Raschel, and crochet machines, available as individual parts and as modules.
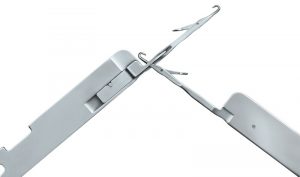
Flat Knitting
Modern flat knitting machines not only carry out complex loop forming sequences, they also have to cope with wide-ranging functional requirements and the most stringent aspirations. Alongside a wide variety of patterning and color possibilities, end customers also demand flexible use of yarn. Latch needles, compound needles and system parts are a vital component at the heart of every flat knitting machine. The surface quality of Groz-Beckert needles in the areas of the transfer clip and stitch support, the inside arch of the hook, and the latch head, guarantees the gentlest possible treatment of the yarn during loop formation. The dimensional accuracy in terms of transfer clip and latch seat positioning, and the latch design itself, ensures a consistently high standard of fabric quality.
What is good for fashion also is good for business: An increase in profitability and productivity can be achieved with the reduced needle consumption and improved process reliability during the transfer process due to surface quality and dimensional accuracy. Furthermore, satisfied customers are guaranteed with consistent, flawless fabric quality and a minimum of subsequent work required. Flexibility in terms of patterning possibilities and yarn input opens up scope for whole new fields of business.
Groz-Beckert’s offer to the knitting industry is completed by detailed services including personal application advice, textile testing as well as needle oil and damage analyses. At the company’s own Technology and Development Center expert support and innovative development partner with know-how and knowledge of the industry. Behind products and services is a workforce of more than 9,000 employees world-wide dedicated to excellence in development and manufacture — and the provision of sound customer support.
October 22, 2020