More and more customers are also paying attention to sustainability when it comes to fashion and clothing. But garments are more than fabric — after all, there are also yarns, fibers and applications such as zippers. All the better if they are also made from the same biobased solutions: from biobased VESTAMID® Terra.
“The zipper is a rather complicated product,” said Gabriele Mosso, suspecting that his comments will probably surprise some people. This everyday object, that’s so familiar to us all, which we have relied upon for so long to close jackets, bags or bed linen — undoubtedly an ingenious concept, but: complicated, really?
“It’s a fascinating object,” Mosso affirmed. As head of the Italy-based zipper manufacturer Nyguard for 15 years, he calls himself a “zipper maniac” with a wink and knows what he’s talking about. For a zipper to function smoothly a lot of detailed work is required, the right material, the exact shape. The teeth must mesh smoothly, must not get stuck, must not falter. And the fastener must literally integrate seamlessly into the tape. The idea for the zipper was born 125 years ago, at that time using sliding metal clasps. But the first versions all failed because they were cumbersome or quickly snagged. “In recent decades not much has changed about the basic idea for zips,” Mosso said. But the details have. Today, the clasp is mostly made of plastic and the strap is also synthetic.
Circulation Is The Target
This is where material development meets sustainability. More and more consumers feel a lot more comfortable when they feel that their consumption is not contributing to growing mountains of waste. So what could sustainable fashion look like? Recycling garments would be one variant: “Recycling materials is generally difficult when different materials are firmly bonded together,” Mosso said. That’s as true for composite packaging as it is in this case for pants with zippers. Different types of synthetic textiles and accessories are difficult to properly separate.
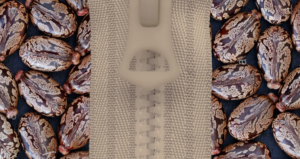
The same applies for certificates of origin for these various individual parts. The apparel industry is well-known for sourcing numerous components from completely different countries and production locations — from yarn, to buttons and zippers. “The latest challenge in textile is to achieve a complete traceability and circularity in value-chain. A process in which all the synthetic textiles and accessories could be recycled together” said Alan Garosi, head of Marketing at Fulgar, the Italy-based manufacturer from which Nyguard obtains the yarn for its zipper tapes.
Aware of that, Mosso added: “Why not make the zipper out of the same material as the tape it’s attached to? From plastic, sure, but why not from a more sustainable, biobased plastic. And even better: from a material that would also be suitable for use to make the complete garment?” This would at least bring us a decisive step closer to the possibility of recycling clothing. Even if there is still a long way to go before this vision is realized, because some details of clothing recycling still have to be invented — the prerequisites on the part of the manufacturers would be created.
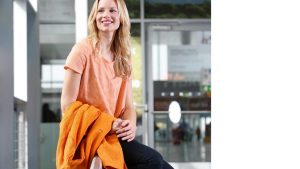
Striking The Nerve Of The Times
It is precisely for orders like these, for outdoor and luxury clothing, that Fulgar also sees the close cooperation with Nyguard’s zipper manufacturers as a real benefit: “After all, we also have to think about the end of life of our products,” Garosi said. “If it becomes easier to recycle a garment, then that’s a meaningful thing for all sides.” That, in turn, pays into the larger issue of sustainability.
“A few years ago, companies were interested in sustainable zippers but not yet willing to pay for them,” Mosso added — an experience that matches that of Fulgar. But now, that has changed, and in 2020 in particular, demand has increased significantly. For Mosso, this is proof that his decision to fully focus on biobased plastics was the right one.
In the meantime, he is increasingly approaching customers with custom-made model designs of combinations of zipper and yarn, both of which are made using VESTAMID Terra. “We’re sort of doubling our sales strength there,” Mosso said. “It’s true co-marketing. And it’s highly successful because it hits just the right nerve.” Especially since, to his knowledge, he remains the only supplier currently offering zippers made from biobased materials. “That’s because we were early adopters of it, and our production process is already very well set up for it.” He winks. The zipper — that is, after all, a thoroughly complicated product in some details.
Create A Targeted Niche
After some market research, Gabriele Mosso found what he was looking for at Evonik. The specialty chemical company’s VESTAMID Terra is a nylon made entirely from biobased material, castor oil to be precise. This is a raw material that is inedible for many animals so is not used as a food source, or as animal feed. Additionally, since the plant known as the “miracle tree,” tolerates dry soils and drought, cultivation of the renewable raw material does not compete with land used to grow food. This makes it an ideal plant for use in biobased solutions. At Nyguard, the decision was made about four years ago to move consistently in this direction. “We can’t compete with really big companies anyway — so we purposefully created a niche for ourselves,” Mosso said. Nyguard still occasionally produces zippers from plastic that is not biobased: “But the proportion of renewable raw materials is moving strongly toward 100 percent.”
Cooperation With Yarn Producer Fulgar
Another special idea of Mosso’s, also contributes to this successful conversion: He has sought cooperation with textile manufacturers in order to help convince his customers of using only products that are made of just one material. In this case, with Fulgar.
“The plastic from Evonik was an extremely good match for the polyamide we had been using,” Alan Garosi said. That’s because spinning a yarn from plastic requires detailed knowledge and expert experience. “Especially for high-quality textiles, plastic yarns need a high level of quality and purity,” he adds. Fulgar entered into a close exchange with Evonik, and both sides learned from each other as he describes: ”After a whole series of trials, we had found the formulation that worked best for us.” As a marketing executive with twelve years of experience at Fulgar and a long-term commitment to sustainability in textiles, he adds, “I’m watching the market and noticing a significant shift toward sustainability in the fashion and apparel industry in recent years.”
Textiles Made Using Bio-Based Fibers: Is It Possible?
Initially, it was just a curious interest from Fulgar’s customers: Textiles made from biobased solutions — would such a thing be possible and what would it look like? “But for about three years now, the topic has been picking up enormously,” Garosi noted. This is especially the case in the premium segment. Fulgar produces 36 million kilos of yarn per year, and here it has made a name for itself in the high-tech yarn sector, as well as with sustainable materials — even if these still make up a comparatively small share. The yarn that Fulgar produces from VESTAMID Terra is marketed under the brand name “EVO® by Fulgar”, an elegant, artistic nod to Evonik.
“Fulgar was the first company to recognize the opportunities for textiles made from VESTAMID Terra,” said Johannes Krampe, manager, Filaments, at Evonik’s High Performance Polymers business line. Evonik, in turn, was the first company on the market to think more broadly about the possible areas of application for a biobased plastic such as VESTAMID Terra: “We are really noticing how much the sustainability topic is now present in the industry,” Krampe said. More and more companies are responding to this desire on the part of their customers “not to be part of the throwaway society,” as Krampe puts it.
Plant Products From The Factory
“Particularly among customers, the term polyamide is still anchored in their minds as something artificial,” Garosi noted. After all, the term “plastic” already expresses that. “For many, it’s not very easy to understand that something made in a factory is actually a thoroughly plant-based thing.” In this regard, Fulgar was particularly excited about the fact that VESTAMID Terra is a 100 percent biobased material — and that its cultivation is not in competition with food production. “Many other fibers are made from sugar cane or similar materials that do place demands on the land. That’s one of the really central strengths and advantages of VESTAMID Terra,” Garosi said.
But for a yarn producer, VESTAMID Terra offers even more advantages. “The synthetic fiber is also extremely good in moisture management and also in coverage,” Garosi elaborates. With a comparatively lightweight fabric made from it, the wearer feels better protected from the wind and cold. In addition, moisture evaporates better with VESTAMID Terra than with comparable petrochemical-based nylons. This makes VESTAMID Terra an interesting alternative for sports and outdoor clothing, among other things, as well as for underwear. “But we also now have enquiries from producers of evening wear and luxury fashion,” Garosi said. In this segment, Fulgar is also well connected due to its high-quality production. Two years ago, Fulgar even supplied its EVO yarn to a shoe manufacturer.
June 15, 2021