W
ith thousands of looming needles used in the process, tramp metal is inevitable in
textile processing operations. Undetected, these pieces will damage equipment, causing expensive
downtime and product contamination.
That was the situation at Beaumont, Texas-based Clark Felt Co. The manufacturer of high loft
nonwoven material — including cotton, man-made-fiber and fire-retardant batting — was
experiencing frequent shutdowns of its carding machine because of metal entering the unit without
detection.
“We process fiber for use in mattresses and padding and cushioning materials for the
furniture industry,” explained Joe Ramirez, process manager, Clark Felt. “Our carding machine is an
important part of our process.”
The carding machine completes the cleaning of the fibers and arranges the fibers into a web
so that they are mostly parallel. By the time the tramp metal was discovered by workers, damage had
been done to the cylinder wire on the card, according to Ramirez.
The company had hoped that magnets would eliminate the metal contamination. Unfortunately,
they didn’t quite do the trick. “We had problems with metal contamination eluding magnets
previously installed in the system,” Ramirez said. “Sometimes a sideplate would fall off from a
piece of chain or we would get other metal in the fibers.”
“Once the metal passed through the magnets and was not rejected, we couldn’t tell we had a
problem until the metal destroyed the cylinder wire,” Ramirez explained. “We were also relying on
electric current passing through feed rolls of the carding machine. When metal contacted both feed
rolls, it was supposed to create a short circuit and trip the relay,” he continued.
However, metal was still passing through, causing the malfunction in the cylinder wire. Each
occurrence cost $20,000 to $25,000 to fix the problem, so Clark Felt decided to seek an alternative
solution, according to Ramirez.
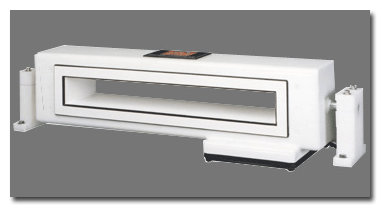
The Eriez® E-Z Tec® Metal Detector
Detecting Metal With E-Z Tec
In the textile industry, metal can enter the production process with the raw material or can
get into the product because of wear or failure of processing equipment components. Detecting these
prevents major damage and equipment downtime, thus increasing productivity.
To help resolve its metal contamination problem, Clark Felt installed an E-Z Tec Metal
Detector with 10-inch-high by 102-inch-wide aperture and special anti-static slider bed
manufactured by Erie, Pa.-based Eriez®, a supplier of advanced technology for magnetic, vibratory
and inspection applications.
Cotton and polyester nonwovens are static-supporting, which is known to cause false trips in
metal detectors. E-Z Tec is equipped with a specialized electronic mode that ignores the high
voltage charge. This feature enables the E-Z Tec to ignore the unipolar static charge and look for
the bipolar signal generated by metal.
“Now, the fiber is passed through the aperture prior to entering the carding machine,
stopping the feed conveyor if metal is detected,” Ramirez explained. “Since we installed the Eriez
detector in 2004, we have not had a single occurrence of metal contamination causing damage to the
card. The Eriez Metal Detector has paid for itself several times over the last five years,” he
commented.
“This was a difficult installation with very limited space and lots of moving parts and
vibration,” Ramirez recalled. “The durability of the system is, without question, more than we
could have expected. The metal detector was struck by a cylinder on one occasion, causing very
obvious cosmetic damage, but the effectiveness was unchanged.”
How It Works
The E-Z Tec Metal Detector uses three coils wound around the aperture to sense metal moving
through it. The center coil emits an electromagnetic field throughout the space within the metal
detector housing. Two receiver coils (placed equidistant on either side of the center coil) are
connected in series so that the energy coupled from the center coil to either of the receiver coils
exactly cancels the energy coupled to the other receiver coil; the net output of this pair is
essentially zero.
Metal passing through this set of coils creates an imbalance which, if the signal’s amplitude
is great enough, will result in detection. The metal detector can be set for a certain degree of
sensitivity. Many factors influence the sensitivity, including characteristics of the product being
screened, type and shape of metal to be detected, aperture dimensions, and the position of the
metal particle within the aperture.
“The Eriez Metal Detector actively seeks metal instead of passively waiting for a condition
to be met,” Ramirez said. “This has totally eliminated metal passing through our carding machine,
reducing downtime and costly cylinder wire replacement. We expect the detector to last 15 to 20
years.”
Editor’s Note: This article was provided to
Textile World by Eriez. For more information, contact +888- 300-ERIEZ (3743)
within the United States and Canada;
eriez@eriez.com;
www.eriez.com.
February 16, 2010