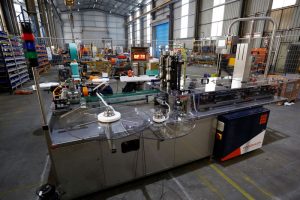
TW Special Report
Faced with the COVID-19 emergency in March 2020, Australia’s Department of Defence (ADF) sought out domestic suppliers to produce 58 million Level 3 surgical masks by November 2020. The ADF offered a contract to MedCon, a Melbourne-based supplier of medical apparel and supplies, which was Australia’s only current domestic producer of Level 3 masks. However, due to the continued influx of low-cost masks from Asian producers, MedCon’s annual production of Level 3 surgical masks had fallen to just 2 million.
MedCon execs told ADF officials that meeting the goal — a 29-fold increase over current annual production to be accomplished in just eight months — would require a major engineering, machine building and implementation effort. The effort would involve revamping three aging mask-making machines and building five new machines. Because no original blueprints were available, components for the five new machines would have to be reverse engineered based on disassembly and analysis of the older equipment, then fabricated and assembled with available engineering know-how.
Citing national urgency, ADF officials issued the production contract to MedCon and stepped in with resources to help. First, they assigned a team of 27 military engineers to provide any necessary assistance to the project. Then, they promised to help MedCon fast-track procurement of components and technology essential to completing the new equipment and ramping up its production to meet the national goal.
As the military engineering team worked with MedCon experts to analyze the mask-production process and begin disassembly of one of the existing machines, one of Australia’s premier machine builders, Foodmach, was contracted to lead the machine-modernization and -building project. Foodmach faced a dual task and a tight timeline. First, it was required to modernize the three older mask-making machines and deliver them within an eight-week period. Second, it had to reverse engineer, build, test and deliver five new machines in a subsequent six-week period. Normally, the job to build a single new machine would take 16 to 20 weeks with drawings, but Foodmach and its supply chain partners had to complete the entire job in a total of 18 weeks from start to finish.
One technology critical to all of the mask-making machinery was ultrasonic welding. Basically, ultrasonic welders convert electrical energy to high-frequency mechanical vibration, which is transmitted through tooling into thermoplastic nonwoven material. The vibration creates frictional heat that melts the material, an operation that can be focused and utilized to:
- Cut or slit a large roll of nonwoven fabric into narrower strips — cut edges are simultaneously seamed/sealed by the heat;
- “Quilt” multiple layers of nonwoven material into a laminated product such as a multilayer face mask; or
- Bond multiple layers of nonwoven fabric into a finished seam — the edge of a face mask — or attach a nonwoven tie strap or stretchable nonwoven ear loop to the edge of a mask.
Project managers requested Branson™ ultrasonic welding technology for the task and contacted Emerson through its regional representative, Consonic Pty. In all, they sought 34 Branson welding units, enough to outfit the eight mask-making machines with four welding stations each, plus two spares. Each ultrasonic welding station would require a 20 Hz Branson DCX power supply, a matched converter and booster, plus an application-specific sonotrode, locally developed and fabricated by Consonic.
At the time the emergency welder procurement order was being developed, Australia’s Department of Defence and project leaders feared that the global surge in demand for medical and personal protective equipment (PPE) — and a secondary demand spike for nonwovens production equipment like ultrasonic welders — could delay welder procurement and delay machinery production. Nevertheless, they proceeded with the order, pressing Emerson and Consonic for the fastest possible delivery.
Emerson responded quickly to the Australian request, ensuring that an initial installment of the welders would be available to ship in 14 days. In response to three orders by Australia’s Department of Defence officials, Emerson’s U.S.-based manufacturing facility assembled, tested and completed 34 units, with each of the three orders staged and ready to ship in about 10 days.
Then, following each overnight shipment to Australia, the Consonic team stepped in, providing Branson technical support for the Foodmach machine builders, who had to integrate the Branson equipment into four welding stations on each of the mask-making machines. When the mask-making machines are in operation, two Branson welders continuously “stitch weld” multiple layers of nonwoven fabric into mask laminates trimmed with fabric tape. The third welder bonds nonwoven tie straps to each side, while the fourth embosses a MedCon logo.
Helped by Emerson’s prompt delivery of the critical ultrasonic welders, Foodmach completed all mask-making machines on or ahead of the tight 18-week schedule. Following delivery of mask-making machines to MedCon, Consonic’s specialists completed welder training for machine operators, putting MedCon on track to meet its ambitious mask-production goal of 58 million by November 2020.
October 15, 2020