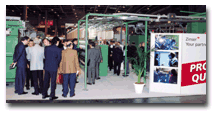
At the outset it should be pointed out that there was nothing eye catching about the short
staple spinning machinery exhibited in Paris, barring a few developments. How the absence of any
revolutionary development and the level of technology exhibited at the ITMA 99 show will mark a
point of departure for a generation of compact spinning systems only time will tell.There was also
an absence of some machinery manufacturers such as Crosrol. Others such as Marzoli and Vouk only
disclosed roundups. But the shining lights were the exhibition of high technology used in the
operation of equipment. New Developments For Ultra-Fine YarnsSKF Spinning Parts demonstrated a
system for spinning a Ne 335 cotton yarn (1.77 tex) from cotton with a micronaire of three. The
yarn had only 14 fibers in a cross section, while a commercial yarn usually requires a minimum of
50 fibers in a cross section. Obviously, such a fine yarn is not viable in a commercial sense.
Nevertheless, it highlights the technical effort that the machinery industry is expending to
advance the technology of short staple fiber spinning.In the area of ring spinning, the concept of
compact spinning process (new products based on the old technology of ring spinning) where a new
drafting unit design and pneumatic suction allows the production of a compact yarn without
hairiness, was very much present. Rieter, Suessen, Zinser and M.A.L. all exhibited this
technology.The Rieter ComforSpin® demonstrated the consolidation of the drafted fiber ribbon
through a rotating perforated roll. Rieter pointed out that there are already 100 machines with
1,000 spindle each operating in the industry.The process works efficiently for combed yarns, and
the yarns produced are less hairy, highly compact, have better evenness and a lower number of
imperfections.The Zinser and M.A.L. systems are based on the action of perforated belts at the exit
zone of the drafting unit while the Suessen system works on the principle of a filtering ribbon on
a vacuum device. The Suessen system can be fitted on conventional ring spinning and is equally
suited for carded yarns also. Rotor Spinning Reengineered With RoboticsIn the area of rotor
spinning the development trend was the renovation of the system by reengineering the rotor spinning
material and automation through robotics. However, the machines based on the 35-year-old technology
of the Czech BD 200 were still in evidence.The Corobox SE II shown by Schlafhorst incorporated a
completely new design, which ensures low energy consumption. This is accomplished by the
introduction of innovative magnet bearings with optimally streamlined shapes.The Autocoro 288 which
incorporates the SEII Spinning box requires less maintenance and has reduced short lot-change times
in comparison to earlier models.The Corolab ABS absorption sensor allows the detection of foreign
fibers directly during the spinning process.Rieter demonstrated a fully automatic R20
rotor-spinning machine capable of making five-kilogram packages, spinning start-up after the
doffing process without additional piecing and offering high productivity automated technology. The
semi-automated BT903 machine equipped with an AMISPIM piecing system is claimed to produce a
high-quality, rotor-spun yarn. This development offers a new machine type that currently does not
face any direct competition in the rotor spinning market.The FRS rotor spinning by Savio
demonstrated an economical solution to the spinning of quality rotor yarns. The auto-vacuum rotor
is claimed to produce soft and highly even yarns.Suessen, a specialist in the development of rotor
boxes with three million units in the field, demonstrated a new box SC-I.The SC-I box incorporates
a bypass in the vacuum system and optimum performance can be achieved for processing of several
types of fibers including man-made fibers. The box is equipped with a reliable trash removal and
offers a completely new design for improved productivity.The development of the box (SC-I) is
particularly suited for upgrading of existing units. Non-Conventional SpinningIn the
non-conventional spinning field, there was not much that caught the attention of visitors.Fehrer
once again exhibited its unique friction-spinning unit. Suessen and Murata reminded everyone that
air-jet spinning is the fastest growing short staple spinning technology.The air-jet spinning
technologies exhibited by Suessen and Murata generated a great interest and promise tremendous
potential for prospects in the development of newer textile yarns.
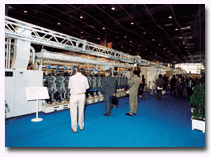
In addition to its Vortex Spinning System, Murata also showed numerous refinements for its
Mach Coner winders. The conventional spinning processes have benefited from these recent
improvements. The direct sliver-to-yarn spinning in the ring system has adopted the sliver cans
developed for air-jet spinning systems.The (MVS) Murata Vortex Spinning System, first shown in
Osaka two years ago, is based on the insertion of twist in a part of the fiber bundle by an air
vortex. This produces a yarn structure and consequently, properties that are closer to that of a
ring or a rotor yarn than that of an air-jet yarn.The spinning machinery builders did not exhibit
many roving frames, although, it is much too early to discount the use of roving in yarn
spinning. Sliver Preparation Gets FasterA processing speed of 1,000 meters per minute on
drawframes made history at ITMA. It has been possible due to mechanical controls. Rieter,
Trutzschler and Vouk have achieved these speeds due to unique machine designs.Trutzschler exhibited
a four-over-three roller drafting system with a pressure bar, while Vouk displayed a
three-over-four roll drafting system. Rieter and Trutzschler also showed the CUBICAN rectangular
section cans system. Combing Speeds Increase DramaticallyCombing speeds have gone up by nearly
30 percent in the past ten years. Rieter demonstrated a new concept, which allowed the speed to
increase to 400 nips per minute, instead of the earlier version of 350 nips.M.A.L, the German
machinery manufacturer also claimed similar combing speeds while Marzoli and Toyota exhibited
combers with 350 and 360 nips per minute speeds, respectively. These increased speeds have been
possible due to improved design achieved through new CAD techniques.Rieter and Marzoli also
exhibited completely automated systems for the supply of ribbon laps. New Cards Give Optimized
PerformanceThe machine manufacturers have demonstrated improvements in the carding process, which
are primarily due to optimization of the cylinder/flat coupling.Rieter has had a self-grinding card
on the market for the past two years. In Paris, the company introduced an integrated flat grinding
system called IGS-Top. This system is presumed to reduce nep count in the card sliver as compared
to similar cards and also increase the life-expectancy of the card wire.Trutzschler exhibited a
grinding process (PFG) which acts on the ends rather than on the sides of the wire. This process
includes a control system that is dependent on nep rate (determined by NEPCONtrOL NCT and card
sliver weight).Trutzschler also displayed an electronic control system for gap between cylinder and
flats during rotation in addition to a card adjustment system, which helps control bow in a flat
with an actuator. These developments have allowed the machinery manufacturers to achieve production
rates as high as 100 kilograms per hour. The new Marzoli C501 Card also meets this
performance.Trutzschler exhibited an auto-regulated drafting system with three pairs of rolls
installed at the end of the card to produce a pre-drafted sliver. The system is capable of a
drafting rate of 300 percent with an exit speed of 500 meters per minute.This system is unlike the
prevalent short-term regulating systems installed at the delivery end of a card. This is definitely
a departure point from the traditional carding and drawing short staple systems, and its
introduction will influence the open-end rotor spinning process.It will be important to keep in
mind the new sliver preparation process in short staple spinning systems. Opening And Cleaning
Optimized By ComputerThere was a conspicuous absence of carousel bale openers and not all the
opening and cleaning machinery manufacturers exhibited their wares. Trutzschler exhibited a
detailed version of the cotton opening and cleaning (bale to sliver) and the carding system.The BDT
020 machine remains the star among the automatic bale openers. The gradual tuft extraction and the
progressive forward movement of the cotton bales allow for a continuous supply of material in the
process. A specific supply cart for the bale opener is also proposed.Speeds of 800 kilograms per
hour were claimed for the CLEANOMAT (CXL) and the TUFTOMAT cleaning machines.Rieter announced that
the UNI Clean BII cleaner integrated with the Vario Set System should reach production speeds of
1,200 kilograms per hour.Rieter and Trutzschler also displayed a computer control system that helps
to manage the optimization of the cleaning process and the extraction of trash.Editors Note: Marc
Renner is a professor at ENSITM, Mulhouse, France, and Bhuvenesh C. Goswami is a professor at
Clemson University, School of Textile, Fiber and Polymer Science.
October 1999