Technology TrendsBy Jim Phillips, Executive Editor Control Systems Prod Productivity
Automation facilitates production efficiency, product quality, reduced costs. Todays
modern textile plants produce the highest-quality yarns and fabric, with less labor and more added
value than at any previous time in history. The equipment used plays a large role, of course.
High-technology air-jet and rapier weaving machines operate at higher speeds and with greater
efficiency than ever thought possible, as do circular knitting machines, needlepunch looms, cards,
roving frames, spinning frames, twisters, etc.But an increasing role is played by the control
systems employed to keep manufacturing within tolerance and maintain production efficiency and
product quality. From opening through shipping, systems are available that eliminate cost, increase
production and quality, and provide for ease of maintenance and less downtime.The term control is a
broad one that encompasses a wide range of solutions. For the purposes of this article, the term is
defined as a product that adds value by contributing to the automation of the manufacturing. The
equipment reviewed below ranges in cost from just a few dollars for a relatively simple, but
amazingly effective, yarn-tension-control device, to hundreds of thousands of dollars for
high-technology, digital fabric-inspection systems. For this review,
TI provides a look at products from Gaston County, Elbit Vision Systems, Erhardt+Leimer,
IKOS Technologies and Otto Zollinger. Dyeing Controls From Gaston CountyGaston County Dyeing
Machine Co., Stanley, N.C., is known throughout the world for the quality of its equipment for the
dyehouse. What many may not understand, however, is that Gaston County is, as well, among the
worlds largest suppliers of control systems for the dyeing process. The company has a separate
division that manufactures control systems and employs 140 people in a 60,000 square-foot facility.
The companys SuperTex+SQL computerized control system provides supervision of virtually every
dyeing area, according to Harold Wilson, executive vice president. The program runs on a Pentium®
PC-based platform and incorporates high-speed peripheral controllers, printers, tape drives and
other components.
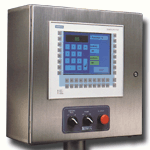
The system is designed for modular installation, which allows a customer to start with just
the basic ControlTex system and then expand with additional software modules as business expands.
Among the processes the system controls are formula management, drug room supervision, boiler surge
control, automated chemical delivery, process analysis, machine control, dye/chemical inventory and
floor scheduling. The system, according to Wilson, increases machine production; reduces dye and
chemical cost and waste; identifies manufacturing inefficiencies; improves formula management,
product uniformity and workflow; and manages utility demand.The dyehouse of the future will be part
of an integrated facility that uses computer technology to capture, distribute and display
performance data for a wide variety of management uses, he said. Thanks to non-proprietary software
designs, SuperTex+SQL can join otherwise isolated control and information systems within the plant
to become an effective and efficient network. As part of this network, SuperTex+SQL will be able to
provide data for production planning and lot tracking, inventory and material cost control, quality
control and quality analysis, maintenance planning, and manufacturing cost control.In conjunction
with the companys MP6000-series machine controllers, the system ensures dyeing processes are
carried out with exacting precision, he said. SuperTex+SQL increases dyehouse productivity by
reducing idle machine time and labor inefficiency; reduces inventory cost by more effectively
managing dyes and chemical consumption; improves product quality by providing precise control over
all aspects of the dyeing process; and improves color kitchen management by overseeing systems that
automate dispensing and batching for dyes and chemicals.A key feature of the system is Sentry-Link,
which provides communications between Gaston County and the customers installation, Wilson said.
With Sentry-Link, Gaston County technicians and software engineers can provide remote assistance
with problem analysis and software changes.SuperTex+SQL users have, typically, enjoyed productivity
gains and cost reductions in excess of 20 percent after installation of the system, Wilson said.
The latest offering from Gaston County is the Sentinel Controller, which provides speed and
programming capability to operate dyeing machines and dryers. Based on a Siemens hardware and
software platform and using international communications standards, the Sentinel is easily
serviceable from virtually anywhere in the world, Wilson said.Built-in diagnostics alert operators
to internal component malfunctions or outlying sensor failures. Because of the non-proprietary
interface, the Sentinel Controller can be linked to chemical dispensers made both by Gaston County
and other vendors. The Sentinel system is designed to be linked to a host system or act as a
stand-alone installation. We can literally run a dyehouse anywhere in the world from here in Mount
Holly, N.C., with this system, Wilson said. Inspection Systems From EVSIsrael-based Elbit
Vision Systems Ltd. (EVS), with U.S. offices in Charlotte, N.C., is a company that develops,
markets and supplies web-inspection solutions, products and services to the textile market. EVS
systems automatically detect and categorize spinning, weaving, finishing and other fabric defects;
analyze the shade consistency of fabrics; or monitor printing processes with consistency and
reliability, and at very high speeds.The companys I-Tex program is a family of automatic
fabric-inspection systems based on image-understanding algorithms that imitate the human visual
system. The system can detect defects as small as 0.5 millimeters (mm) on fabric widths up to 600
centimeters (cm) and at speeds that reach 300 meters per minute (m/min). Also, I-Tex detects
diverse spinning, weaving, dyeing, finishing and coating defects on any uncolored fabric.
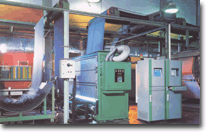
The I-Tex family of automatic inspection systems adapts to a variety of applications and can
be positioned in-line as part of a production process or as a stand-alone unit. In addition to the
standard I-Tex 100 system for greige and technical fabric inspection, the company offers I-Tex
100-Wide for greige and technical fabric; I-Tex 200 for unicolor dyed and finished fabric final
inspection; and I-Tex 2000 for home furnishing, technical, denim and apparel end-uses.The I-Tex
system imitates the human visual system and incorporates an image-acquisition unit, a system
computer, a system workstation and a video album of defects. The inspection process
comprises:Pre-inspection a preliminary learning stage that creates the set of parameters for each
learned fabric/style. The parameters represent statistical features of good fabric.Inspection a
process through which inspected fabric moves through the image acquisition unit; cameras transfer
the fabric image to the system computer; fabric image is scrutinized by a detection phase
algorithm; fabric irregularities are detected as defects, which are grouped according to size,
direction and shape and graded in terms of severity; defect map and images are displayed on a
monitor in real time; information for each defect is recorded; and the defect image is stored. As
an option, an alarm alerting the operator of the defects can be activated on any external
unit.Post-inspection a final phase during which rolls are graded according to predefined
guidelines; an inspection report is printed and sent to the plant computer for immediate or
subsequent action, defect images are analyzed using the incorporated video album; and mandatory
cutting points are regarded and identified.I-Tex monitors a wide range of smooth and rough fabrics.
It inspects fabrics that comprise all types of raw materials and that are designated for diverse
applications including apparel, home furnishing, technical, industrial and others. The system
detects multiple defect types such as: yarn and weaving faults; holes; oil, water and dyestuff
stains; missing threads; starting marks; broken yarn; and dyeing, coating and finishing
irregularities. EVS says virtually any visible defect is detectable.For knitted products, EVS
offers Kni-Tex, an in-line, automatic fabric-inspection system designed for the inspection of
open-width and warp-knitted finished fabrics. Kni-Tex is designed to overcome the knitted fabrics
elastic nature even when Lycra® blends are used. Kni-Tex is designed to inspect fabrics up to 240
cm wide at a speed of up to 60 m/min. Kni-Tex systems can be integrated with stenter frames,
sanfore machines, compactors, or automatic cutting and packing machines. The companys SVA offering
is an in-line system that measures shade variation in dyed fabric. The system uses a calibrated
traversing sensor and proprietary signal-processing algorithm. The sensor readings are compared to
a reading at the beginning of the roll to detect side-to-side and beginning-to-end shade
variations. The SVA is modular and can be accommodated to any fabric width. It is designed to fully
integrate with all I-Tex systems, or to operate as an independent, stand-alone unit.Prin-Tex is an
in-line printed fabric-monitoring and defect detection system that enables on-line detection and
alarm of repetitive printing defects, thus improving fabric quality and increasing printing speed
and efficiency. Printed fabric faults are displayed in real time on a video monitor, which enables
location of the defect and facilitates performing the appropriate corrective action. E+L
Focuses On Process ControlErhardt+Leimer Inc. (E+L), the Spartanburg, S.C.-based subsidiary of
Erhardt+Leimer GmbH, Germany, specializes in system solutions and automation technology for moving
webs and belts. The company offers guides, spreading systems, cutting systems, measuring and
inspection systems, tension-control systems, detwisting and opening systems, entry-frame systems
and exit-frame systems. For this report, TI looks at the companys offerings in wet finishing and
web guiding.In web guiding for wet finishing, the company offers an EGS entry frame system, which
is a compact machine infeed system equipped with pivoting tension rollers, segmented roller guider
systems with split guide plates and a variable-speed pull roll section. Two contra-driven selvage
uncurlers spread out the rolled web edges in front of the segmented roller guider. A wide band
sensor from E+L detects the web position over the full width of the web as a basis for guiding by
the machine center via the segmented roller guider. A pull roll section and compensator roller feed
the web to the washing unit at a set tension.
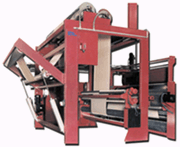
For the steamer outfeed, a flange-type segmented roller guider spreads the web out to its
full width as it leaves the steamer and precisely guides it to the following washing unit. To
optimize the spreading effect, a scroll roller with a contra-driven, pivotable spreader precedes
the segmented roller guider.A high degree of relative humidity, temperature, chemical ambience and
the mounting position make extreme demands on the entire web-guiding system. E+L claims it counters
these effects through the use of superior materials and advanced design. In addition, a drive
reduces bearing and gasket friction so that the web may run free of additional tension sources.
This, the company says, aids in the prevention of undesirable properties such as residual
shrinkage.The companys universally mounted AGS exit-frame system features a variable-speed pull
roll section and a plaiter. A surface-driven winder or reel plaiter is available as well.In
web-guiding framework systems, entry, bridge and exit frame systems may be flexibly designed to
meet specific requirements and permit the optimum positioning of web-guiding devices at the infeed
and exit of textile machines. The stable and modularly designed E+L framework systems are based on
steel or stainless-steel C-shaped sections and, according to the company, are equipped to satisfy
all processing technology demands. The framework systems combine all elements cloth guiders,
steering, rollers, segmented roller guiders, metal detectors, seam detectors, width-measuring or
inspection cameras and more to operate in harmony. Additional components, such as pull roll
sections or tension or dancing rollers, round off the framework system product spectrum, according
to E+L.A fully automated infeed or exit scray (i.e., non-stop web changing) assures the maximum
utilization of the processing system. A roller accumulator at the exit is a solution for
crease-sensitive materials, promoting top processing speeds. Depending on requirements, the final
processing unit implemented on the exit of textile machines may be a surface-driven winder, plaiter
or plaiter-winder combination in conjunction with E+Ls AGS exit-frame system. Software
SolutionsIKOS Technologies Inc., Charlotte, N.C., is a software-solutions provider with a
concentration on business concepts and solutions. The company has developed modules that can be
tailored to specific applications, according to Evan Parissis, president.The companys Locator®
system is a business-enterprise system that has the capability of addressing multiple business
solutions to provide the right combination for a particular industry. The system, Parissis says,
can manage manufacturing, distribution and supply-chain, as well as facilitate time and space
optimization. Among the modules available are those for security, messaging, animation, bills of
lading, employee time tracking, inventory control, invoicing, logging, maintenance, order entry,
product formulation, product procedure, reporting, scheduling, shipping, simulation,
transportation, user activity monitoring, warehouse management and data collection. Yarn
TensionIn an era of increasing technology in virtually every area of business, it is sometimes
refreshing to review a product that is advanced due to the sheer simplicity of its design. Such is
the case with the OZ® Yarn Tension Control system from Otto Zollinger, Inc., Spartanburg,
S.C.
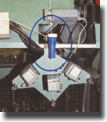
The OZ tension device uses a plastic cylinder or cup and one or more plastic or steel balls
to provide a highly variable response in order to control thread tensions.As the thread runs
through the tensioner, it enters at the bottom of the cup and runs along the surface of a ball,
causing the ball to be set into a rolling motion. The weight of the ball, combined with the thread
partly wrapping itself around the ball, provides a tensioner effect. A major feature of the OZ
system is that it doesnt have to be adjusted once it has been prepared for specific applications by
the inclusion of the correct number of balls and weights. Many machine builders incorporate
sophisticated electronic devices, said Otto Zollinger, president. In theory these are the ultimate.
But they require very expensive installation, complex moving parts and are subject to breakdowns.
Mechanical devices, such as the OZ, are much cheaper and require less maintenance.
April 2001